Mechanical shaft seals play an essential role in various industries, serving as crucial components in rotatory equipment that ensure efficient operations across sectors. Trusted and widely implemented in systems such as pumps, compressors, and mixers, these seals prevent leakage of fluids, enhancing both performance and safety.
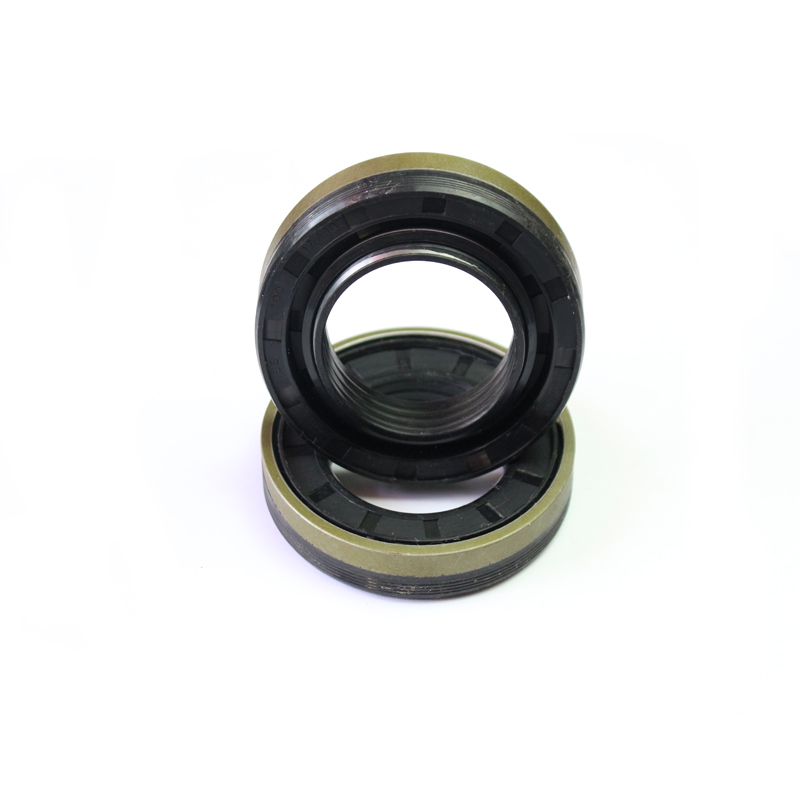
The core function of a mechanical shaft seal is to join systems or mechanisms that house or transfer fluids without letting any contaminants or fluids escape, thereby maintaining system efficiency and longevity. This requires a delicate balance of precision engineering and advanced materials, which distinguishes superior shaft seals from subpar variants.
Experience with shaft seals shows that successful implementation largely depends on choosing the right seal for specific applications. The array of choices includes pusher seals, non-pusher seals, balanced seals, unbalanced seals, and more specialized versions such as gas seals and cartridge seals. Each variety features unique design attributes that cater to specific operational needs or conditions such as pressure, temperature, and chemical compatibility. For instance, pusher seals are noted for their versatility and ability to accommodate misalignment, whereas non-pusher seals typically excel in high-temperature applications where component resiliency is critical.
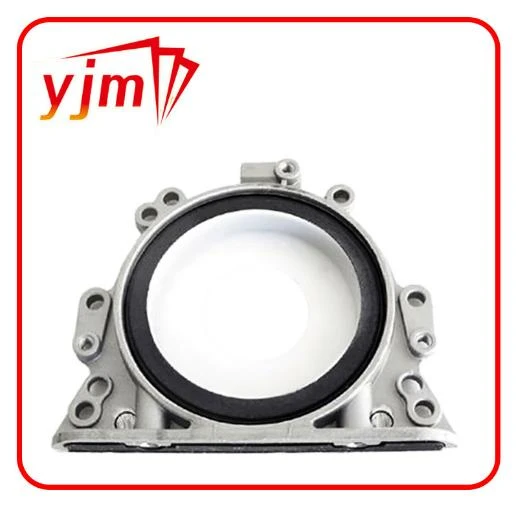
From an expertise standpoint, acknowledging material composition is necessary as it impacts both functionality and durability. Common materials include stainless steel, ceramic, and carbon, each offering distinct advantages. Stainless steel provides excellent corrosion resistance and structural integrity, making it suitable for harsh environments. Ceramic materials, known for their hardness and wear resistance, are typically chosen in abrasive fluid applications. On the other hand, carbon's self-lubricating properties render it a favorite in high-speed applications where friction management is paramount.
Authoritative sources in the field emphasize the importance of installation and maintenance as key determinants of a shaft seal's performance. Adequate training and adherence to manufacturer guidelines significantly reduce the risk of premature failure. Regular inspection and maintenance routines, such as monitoring for leaks, examining seal faces, and checking for wear, are vital practices. When problems arise, informed troubleshooting that considers factors such as misalignment, pressure fluctuations, and thermal distortions will help in diagnosing and rectifying issues effectively.
mechanical shaft seal
Furthermore, selection based on authoritative industrial standards like those from the American National Standards Institute (ANSI) or the International Organization for Standardization (ISO) can instill trustworthiness and reliability in the chosen product. These standards ensure that seals meet rigorous safety, performance, and quality criteria, critical for high-stakes applications like chemical processing or petroleum extraction.
Based on real-world feedback from end-users, the adaptability and ease of replacement offered by cartridge seals stand out. They streamline the installation process, reduce downtime during maintenance, and lower the possibility of operator error. This aligns with the increasing industry trend of favoring user-friendly designs that enhance operational efficiency.
Overall, mechanical shaft seals epitomize a fusion of engineering precision and material science. Their development is driven by continuous innovation that addresses the evolving demands of modern industrial applications. Acknowledging the intricate balance between design, material selection, installation, and maintenance is fundamental for maximizing the operational lifespan and efficiency of mechanical shaft seals.
In an industry where downtime can result in significant financial losses and compromised safety, investing in high-quality mechanical shaft seals emerges as both a strategic and essential choice. By adhering to best practices guided by experience and expertise, supported by authoritative standards, industries can ensure their processes remain seamless, powerful, and, above all, secure.