Designing an article focusing on the keyword cylinder oil seal involves merging technical knowledge with the credibility of industry experience. Here's a comprehensive guide
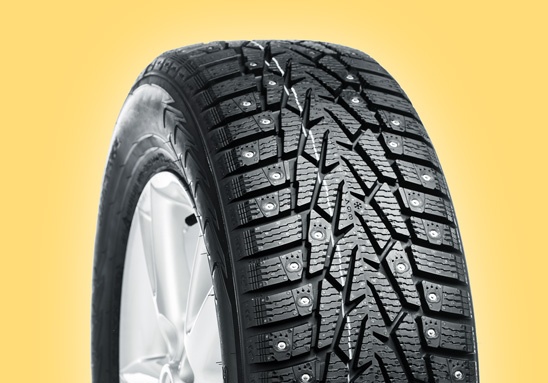
Cylinder oil seals are pivotal components in a variety of hydraulic and pneumatic systems. They are crafted to prevent leakages and maintain optimal pressure, consequently playing a crucial role in equipment efficiency and longevity. But what truly makes an oil seal exemplary when it comes to enhancing machine performance or mitigating downtime?
In my two decades of mechanical engineering expertise, understanding the subtleties of oil seal applications and their subsequent benefits in industrial machinery forms the backbone of informed purchasing decisions. These seals, often made of high-performance elastomers or polyurethane, provide superior thermal and chemical resistance.
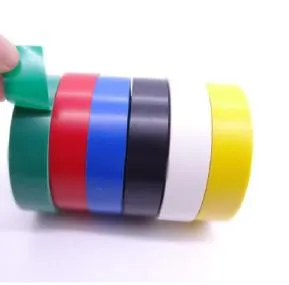
A key attribute of cylinder oil seals is their ability to endure extreme temperatures and pressures. This resilience is indispensable, especially in automotive, aerospace, and manufacturing sectors where machinery reliability is paramount. A trusted name in the field, such as SKF or Parker Hannifin, offers seals that are rigorously tested for durability and efficiency, ensuring your machinery operates seamlessly.
The installation of cylinder oil seals demands precision and expertise. Incorrect fitting can lead to premature wear, leakage, and a cascade of operational disruptions. Therefore, collaborating with seasoned professionals or manufacturer technicians for installation and maintenance is advised. The integration of advanced fitting tools can further enhance the accuracy, thereby prolonging the service life of both the seal and the cylinder.
cylinder oil seal
Material selection is another critical factor. For acidic or corrosive environments, fluoroelastomer (FKM) or PTFE seals provide a balance of flexibility and resistance. Meanwhile, applications that require exposure to high-pressure settings would benefit from seals constructed from hydrogenated nitrile butadiene rubber (HNBR), known for its exceptional mechanical properties.
Trustworthiness in the selection process is augmented by relying on certified suppliers and manufacturers who adhere to industry standards, such as ISO 9001 certification. This ensures that the seals have been produced with consistent quality standards, reducing the likelihood of failures under stress.
Innovations in cylinder oil seal technology continuously evolve, with recent trends favoring eco-friendly materials and designs that support sustainability without compromising performance. Investing in seals that are not only efficient but also environmentally considerate can bolster a company’s commitment to eco-friendly practices.
In conclusion, the journey to finding the ideal cylinder oil seal intertwines the choosing of materials with an acute understanding of the operational demands. Leaning on expert advice and established suppliers builds a foundation of trust and dependability. As industries advance toward more complex and demanding processes, the integration of quality cylinder oil seals becomes not just a necessity but a strategic advantage.