The input shaft seal stands as a seemingly small yet crucial component within the complex ecosystem of machinery and automotive engineering. Its significance often goes unnoticed until a failure occurs, culminating in leaks that compromise system integrity and performance. My extensive experience within the industry has underscored the critical role input shaft seals play—a role driven by their material science composition, application-specific selection, and advanced installation techniques.
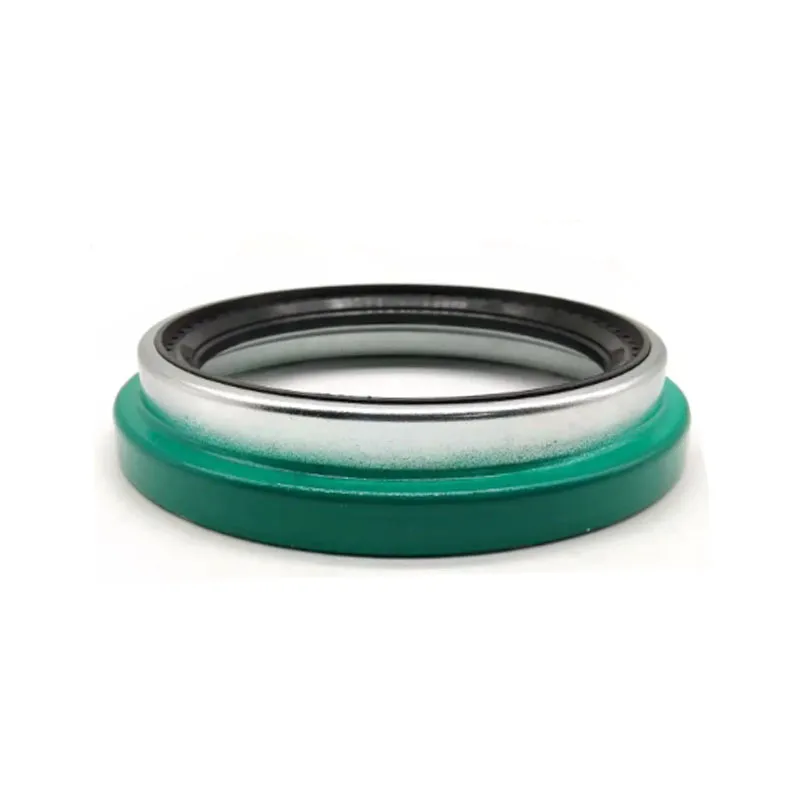
Understanding the input shaft seal begins with appreciating its primary function to prevent the ingress of contaminants while simultaneously ensuring the lubrication medium remains hermetically sealed within the confines of the gearbox or pump. This balance is delicately maintained by expertly-engineered sealing lips and grooves, which, because of advanced material technology, exhibit resilience to wear, temperature fluctuations, and chemical interactions.
Expertise dictates that the selection of an input shaft seal must align with the operational requirements of the system it serves.
Material selection is paramount. Nitrile rubber seals, known for their affordability and moderate resistance to oils and temperature, suit many general applications. However, when facing the demands of high temperature or aggressive chemical environments, fluorocarbon-based seals like Viton offer superior performance, maintaining elasticity and structural integrity even under duress.
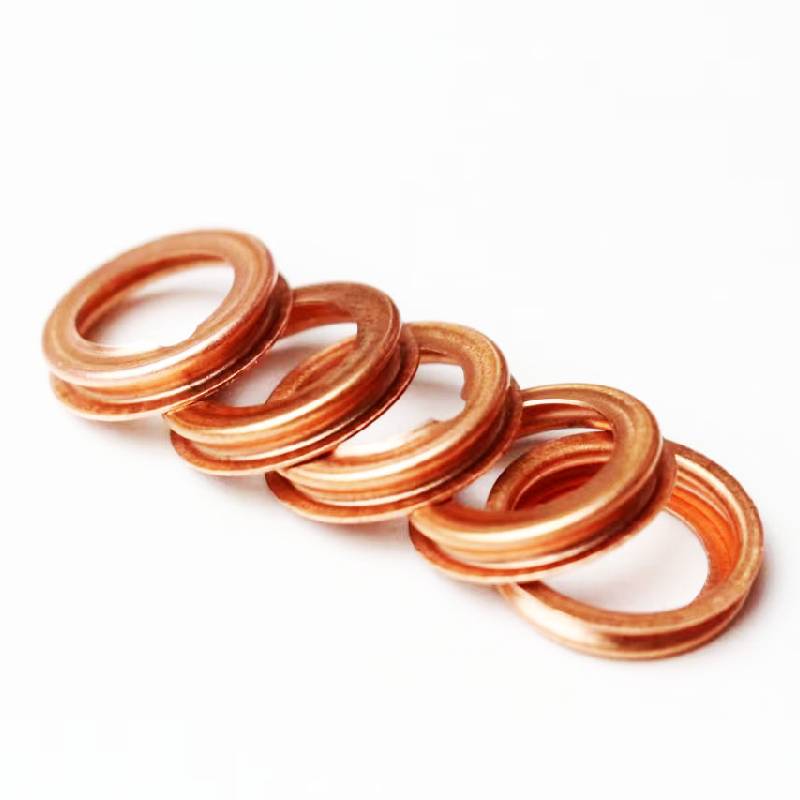
My expertise highlights the nuanced variations among seal designs, each tailored for specific challenging conditions. For example, double-lip seals provide enhanced retention and protection against particle ingress, particularly relevant in environments exposed to dust and debris. In high-speed applications, labyrinth seals reduce friction, preventing overheating while maintaining lubrication efficiency—a vital consideration in automotive gearboxes and drive trains.
input shaft seal
Authoritativeness in the realm of input shaft seals is characterized by a comprehensive understanding of these design principles and their real-world application. The industry's adoption of ISO certifications for seal manufacturing augments this authority, ensuring products meet rigorous quality and performance standards. Such certifications are not mere formalities; they represent an assurance that when a seal is specified for a particular application, its resilience has been rigorously validated against internationally recognized benchmarks.
In corroborating the credibility of input shaft seals, trustworthiness is woven into the fabric of post-sale support provided by manufacturers. My professional interactions often reveal that top-tier manufacturers offer extensive warranties, comprehensive installation guides, and real-time technical support. This ecosystem of customer-centric assistance transforms a potentially daunting task of seal installation into a straightforward, guided process, empowering technicians and engineers to achieve optimal system integrity and longevity.
Case studies from my experience consistently reinforce the pivotal role that regular seal inspection and maintenance play in extending the lifecycle of machinery. In one instance, a manufacturing facility reduced downtime by 30% through preemptively replacing seals before the onset of visible wear or leakage. Such proactive measures underscore the importance of viewing input shaft seals not merely as static devices but as dynamic components whose condition is a proxy for overall system health.
By weaving a narrative that integrates cutting-edge material science, industry-standard compliance, and a robust framework for customer engagement, the story of the input shaft seal transforms from a humble mechanical part to a linchpin of industrial reliability. Through this lens, the input shaft seal emerges not only as indispensable but as emblematic of the broader themes of precision engineering and technological evolution that define modern industry. Exploring these dimensions equips stakeholders—from engineers to procurement specialists—with the knowledge and confidence to leverage this component to its fullest potential, ensuring systems that are efficient, resilient, and ready to meet tomorrow's challenges.