High-pressure O-rings are an essential component in a myriad of industries, revered for their remarkable ability to create leak-proof seals in challenging environments. These small but mighty rings boast properties that make them indispensable for applications ranging from automotive to aerospace, manufacturing to marine.
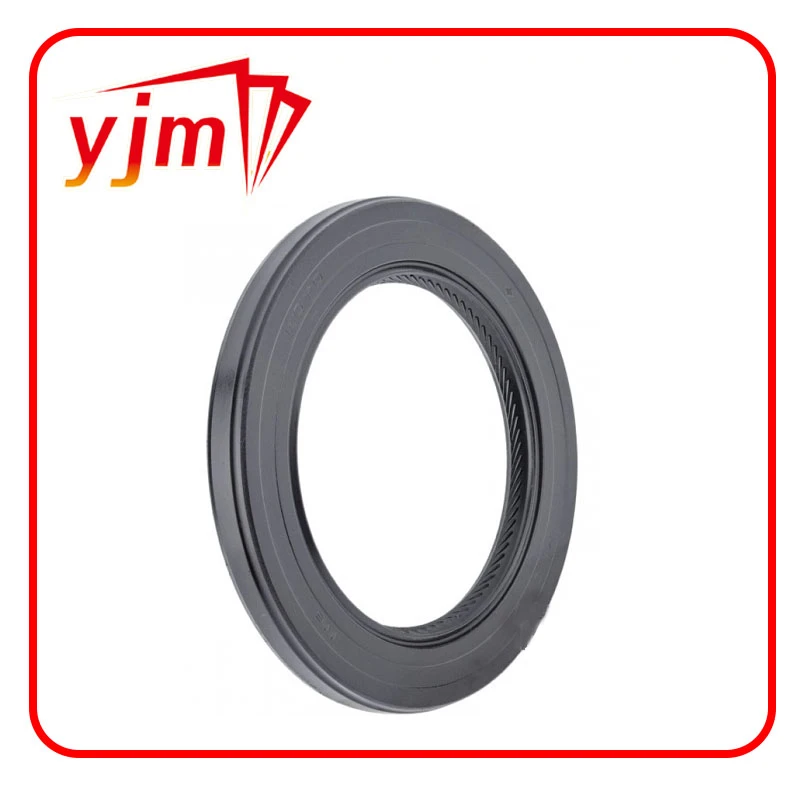
Understanding the intricacies of high-pressure O-rings begins with their material composition. Most are crafted from robust elastomers like Nitrile, Viton, or Silicone, each selected for its resilience to specific environmental factors. For instance, Viton is highly resistant to high temperatures and corrosive chemicals, making it a favorite in industries that demand both chemical and thermal stability. Meanwhile, Nitrile is often chosen for fuel and oil applications due to its impressive resistance to petroleum-based fluids.
The engineering behind high-pressure O-rings focuses heavily on precise sizing and material selection, which directly influence their efficiency and lifespan. Experts know the importance of not just selecting the right material but also understanding the dimensional tolerances critical to high-pressure applications. An O-ring that's too small or made from an inappropriate material can lead to disastrous consequences, including system failures or hazardous leaks. Thus, thorough knowledge of the application's operating conditions, including pressure, temperature, and fluid type, is vital for selecting the correct O-ring.
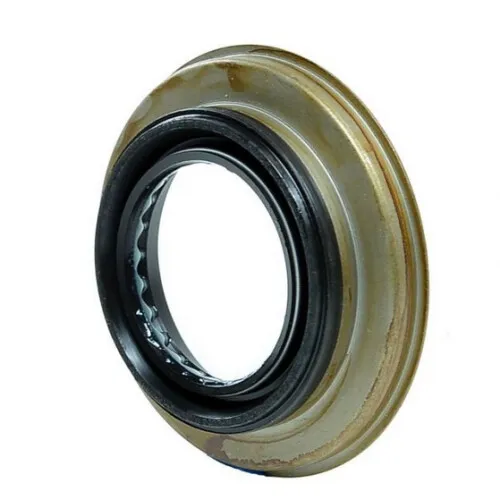
An invaluable tip from seasoned engineers is the practice of selecting O-rings with a durometer rating that corresponds to the specific demands of the application. The durometer rating, which measures hardness, can drastically impact the performance under pressure. For high-pressure applications, using a higher durometer can provide the stability required to maintain a durable seal without losing elasticity.
high pressure o rings
Installation technique also merits significant attention. One common cause of premature O-ring failure is improper installation, leading to issues like extrusion or chemical erosion. Professionals advise meticulous greasing of the O-ring and the sealing surfaces, ensuring no twisting or pinching occurs during assembly. Additionally, when replacing or installing O-rings, it's essential to avoid stretching them beyond their tolerances, as this can compromise their structural integrity.
Another critical aspect is maintenance. Regular inspections can prevent unexpected failures by identifying wear or compatibility issues before they escalate into larger problems. Advanced predictive maintenance software now allows for monitoring the conditions that affect O-ring performance, such as pressure fluctuations and temperature variations, enabling timely replacements and adjustments.
Trust in high-pressure O-rings is built upon years of successful application and continuous research into material science and engineering techniques. Leading manufacturers are constantly investing in innovative technologies to enhance O-ring performance, such as new elastomer blends that promise increased durability and resistance to extreme conditions. These advancements are guided by stringent industry standards that ensure every O-ring produced is capable of meeting the rigorous demands of high-pressure environments.
In conclusion, high-pressure O-rings are a high-tech solution to preventing leaks and ensuring safety in equipment operating under intense conditions. Their effectiveness lies not only in their high-quality materials and precise manufacturing but also in the knowledge and expertise of the engineers who select and manage them. With a focus on material selection, installation procedures, and maintenance practices, high-pressure O-rings will continue to be a cornerstone in the efficient, safe operation of systems across various industries.