High Pressure Lip Seal A Critical Component in Industrial Performance
High pressure lip seals, also known as radial shaft seals, play an indispensable role in various industrial applications where high-pressure fluid containment is paramount. These seals are designed to prevent leakage and maintain system integrity in demanding environments, making them essential components in sectors like automotive, hydraulic machinery, and oil and gas industries.
A high pressure lip seal consists of a primary sealing lip that contacts the rotating or static shaft, a secondary sealing lip for environmental protection, and a support ring that provides stability and prevents deformation under pressure. The lip, often made from resilient materials such as nitrile rubber or polyurethane, is designed to conform to the surface of the shaft, creating a tight seal even under extreme pressure.
One of the key features of these seals is their ability to withstand high pressures without compromising their sealing efficiency. They can handle pressure ratings up to several thousand bars, depending on the material and design. This robustness makes them ideal for use in heavy-duty machinery where high pressure is a standard operating condition.
Moreover, high pressure lip seals also offer excellent resistance to wear and tear, ensuring a long service life. Their ability to maintain sealing effectiveness despite continuous friction with the shaft surface is a testament to their durability. Additionally, they can effectively seal against a wide range of fluids, including oils, fuels, and even water, further broadening their application scope Additionally, they can effectively seal against a wide range of fluids, including oils, fuels, and even water, further broadening their application scope
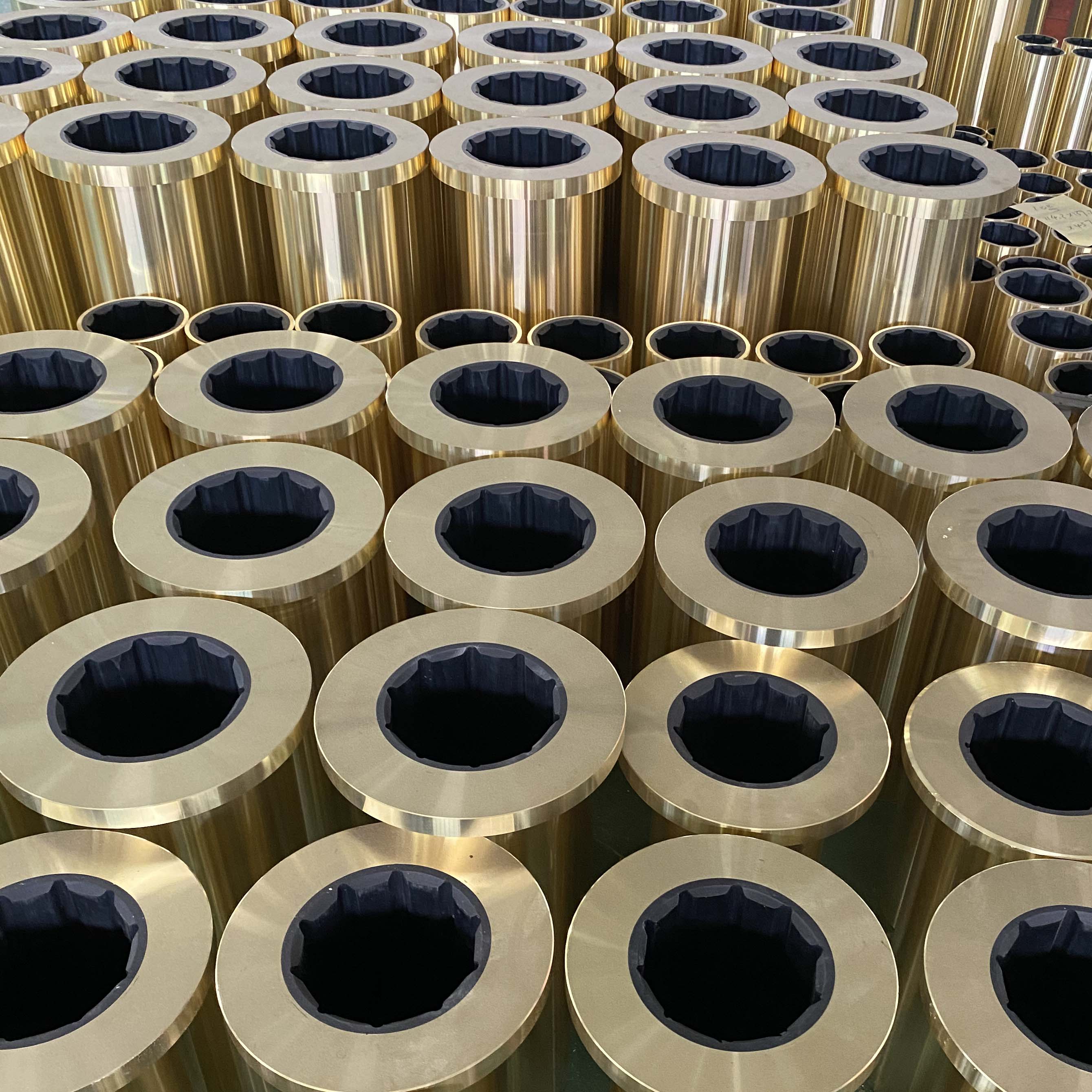
Additionally, they can effectively seal against a wide range of fluids, including oils, fuels, and even water, further broadening their application scope Additionally, they can effectively seal against a wide range of fluids, including oils, fuels, and even water, further broadening their application scope
high pressure lip seal.
However, proper installation and maintenance are crucial for optimal performance. Misalignment, over-tightening, or contamination can lead to premature failure, highlighting the need for careful handling and regular inspection. It's also worth noting that each application may require a specific type of lip seal, considering factors such as pressure, temperature, and chemical compatibility.
Innovations in material science and engineering have continually pushed the boundaries of high pressure lip seal capabilities. Today, we see seals with advanced materials that offer better heat resistance, increased chemical compatibility, and enhanced sealing performance at even higher pressures.
In conclusion, high pressure lip seals are the silent heroes in many industrial operations, ensuring the efficient and safe functioning of complex systems. Their importance cannot be overstated, as they safeguard against costly leaks, minimize downtime, and contribute significantly to overall system reliability. As technology advances, we can expect these seals to become even more effective, adaptable, and integral to the future of high-pressure fluid management.