Heavy seals are integral components in a myriad of industries ranging from maritime applications to construction and industrial machinery. Their robustness and reliability are crucial to maintaining the integrity and efficiency of systems that require an airtight or fluid-tight seal. With the growing demand for durable sealing solutions, understanding the nuances and applications of heavy seals is vital in ensuring optimal performance and longevity.
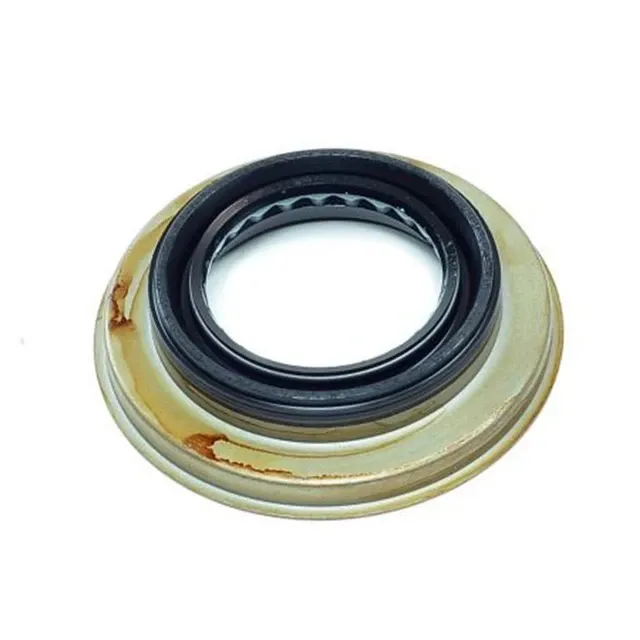
Heavy seals are engineered to withstand extreme environments. They are utilized in situations where conditions are harsh, such as those involving high pressures, temperatures, or corrosive substances. These seals are constructed with materials that provide superior resistance to wear and tear, ensuring they maintain their sealing capabilities over extended periods.
In the field of maritime engineering, heavy seals play a crucial role in maintaining the watertight integrity of vessels. The marine environment is notoriously challenging due to the constant exposure to saltwater, varying temperature conditions, and mechanical stresses. Heavy seals in this setting must prevent the ingress of water while allowing for the movement and vibration that ships naturally encounter. EPDM rubber, Viton, and other synthetic polymers are frequently chosen for their excellent resistance to salt and UV radiation, extending the lifespan of seals under marine conditions.
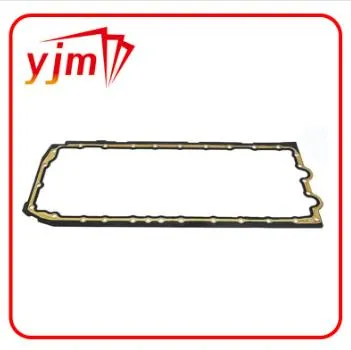
In industrial machinery, heavy seals are vital for protecting hydraulic systems. In construction equipment such as excavators and loaders, these seals must ensure that hydraulic fluids remain contained within their systems to allow for precise and powerful movement of machinery. The failure of a heavy seal in such applications can lead to costly downtime and repairs, highlighting the need for seals that offer both durability and precision. Polyurethane and PTFE (Polytetrafluoroethylene) are popular choices due to their balance of flexibility and toughness, which is essential for enduring the dynamic operational loads.
Expert manufacturers of heavy seals employ cutting-edge technologies in their production processes. Advanced computational tools allow for the simulation and analysis of seal behavior under various conditions, enabling the development of designs that maximize effectiveness and durability. Additionally, the adoption of rigorous testing protocols ensures that seals can perform beyond the outlined specifications, providing users with a product they can rely on.
Authoritativeness in the production of heavy seals derives from an organization's adherence to industry standards. Accreditation by bodies such as ISO (International Organization for Standardization) ensures that products meet global expectations for quality and reliability. This credibility is crucial for users who depend on the consistent performance of heavy seals in critical applications.
heavy seal
Trustworthiness is further cemented by transparency and customer support. Leading manufacturers offer detailed documentation on the materials and processes used in seal creation, as well as providing customer education on the proper installation and maintenance of seals. Comprehensive warranties and responsive service teams are vital in building long-term relationships with clients who require assurance beyond the point of sale.
For businesses requiring heavy seals, the selection of a supplier should involve careful consideration of the provider's experience and reputation. A supplier with decades of industry experience can offer invaluable insights into seal selection and application, tailoring solutions that meet the specific requirements of different environments. Expertise is demonstrated through a comprehensive understanding of material science, engineering principles, and a commitment to innovation in seal design.
Real-world experience and case studies can further enhance the credibility of a supplier. Documented success stories involving the implementation of heavy seals in challenging projects provide prospective clients with concrete evidence of a product's performance. This narrative approach to demonstrating success instills confidence in the capabilities of a supplier to handle unique challenges that a customer may face.
The future of heavy seals promises continued innovation, driven by advancements in material sciences and engineering practices. The integration of smart technologies into seals — such as sensors that monitor seal integrity in real-time — offers exciting possibilities for predictive maintenance and enhanced durability. This shift not only improves the operational efficiency of systems reliant on heavy seals but also underscores the importance of selecting seals that are at the forefront of technological advancement.
Conclusively, heavy seals are indispensable to the functionality and safety of countless systems. Their design and material composition are critical factors in their effectiveness within specific environments. As the demands placed on these seals continue to evolve, selecting a knowledgeable and reputable manufacturer can make a significant difference in the performance and reliability of heavy seals.