In the realm of industrial and commercial applications, the reliability and durability of components are paramount. Enter the heavy-duty seal, an unsung hero in countless machines and systems, essential for ensuring operations run smoothly and efficiently. Such seals are not merely functional accessories; they are critical components that address the unique demands of heavy-duty machines.
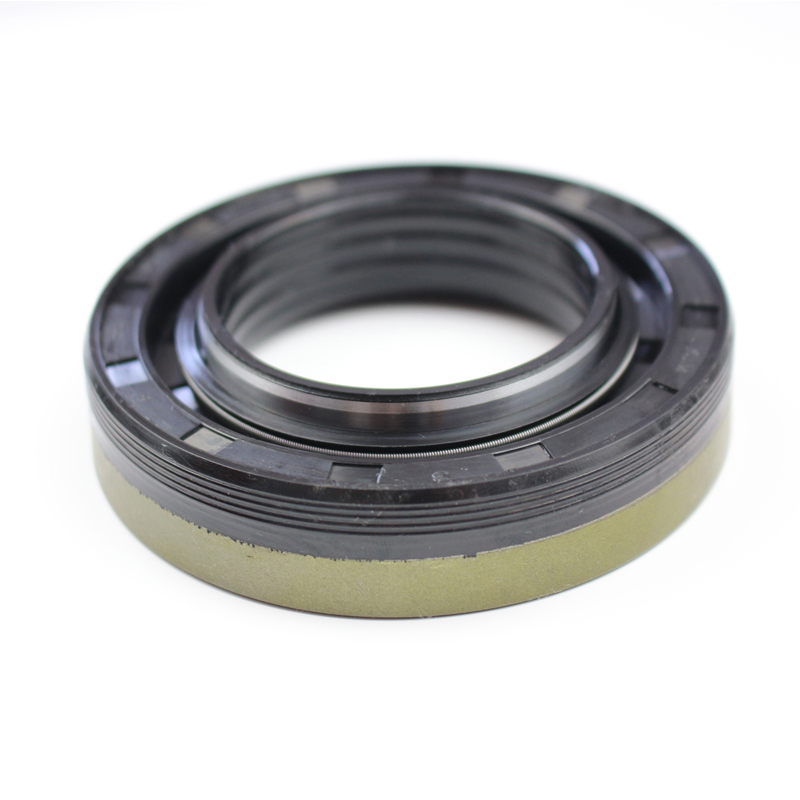
Heavy-duty seals are employed across various industries, from automotive to aerospace, heavy equipment, and oil & gas sectors. They fulfill a crucial role in preventing leaks of fluids and gases, maintaining pressure, and excluding contaminants to protect machinery and enhance performance. Unlike standard seals, these are engineered with superior materials and design innovations to withstand extreme pressure, high temperatures, and abrasive substances.
The materials used in heavy-duty seals are a testament to their robustness. From elastomers, which provide excellent resistance to chemical and thermal degradation, to metal and PTFE composites that withstand high-pressure environments, every material is selected for optimum performance. The choice of material affects not only the seal's effectiveness but also its longevity, ensuring that machinery downtime is minimized and maintenance costs are kept low.
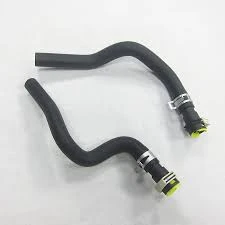
Design is another area where expertise in heavy-duty seals shines. Engineers focus on ensuring the right balance between tight sealing and minimal friction. This is achieved through advanced geometrical designs that account for varying pressures and temperatures. By utilizing modern computer-aided design (CAD) software and simulation tools, manufacturers can predict and enhance the seal performance under different conditions before the product is even manufactured.
heavy duty seal
In practice, the impact of using quality heavy-duty seals is profound. Enhanced sealing solutions directly translate to improved safety and efficiency. For instance, in the automotive industry, where engine components are exposed to high temperatures and pressures, reliable seals prevent potential failures that could lead to catastrophic outcomes. Similarly, in hydraulic systems used in construction and mining equipment, heavy-duty seals ensure systems function optimally, preventing oil leaks that could halt operations and cause environmental hazards.
The trustworthiness of heavy-duty seals is validated by rigorous testing and adherence to strict standards. Manufacturers subject these components to exhaustive testing, including pressure resistance, thermal cycling, and abrasion endurance, to ensure they meet the high demands of their intended applications. Third-party certifications further bolster the reliability of these seals, providing assurance that they have been tested and verified by independent organizations.
Experience has shown that improper seal selection or poor-quality seals often lead to premature failures, causing significant downtime and repair costs. Therefore, companies are advised to consult with seal experts during the design and maintenance stages of their machinery. Such collaborations ensure that the selected seal will match the application's requirements, addressing both the operational conditions and the specific challenges faced.
In conclusion, heavy-duty seals play a vital role in industrial and commercial machinery, highlighted by their design complexity, material resilience, and performance reliability. Companies looking to improve equipment efficiency and operational longevity should prioritize the adoption of high-quality heavy-duty seals. Leveraging the expertise and authority of established manufacturers and industry experts can guide informed decisions, ensuring that the chosen seals offer maximum durability and trustworthiness for years to come. As industries continue to demand higher performance and reliability, the evolution of heavy-duty seals will remain central to meeting these challenges.