The importance of selecting the right gasket for a flat face flange cannot be underestimated in industrial settings. A gasket serves a critical role in sealing and preventing leaks between two surfaces—commonly, pipe flanges. In the context of flat face configurations, certain considerations emerge based on expert experience and technical requirements.
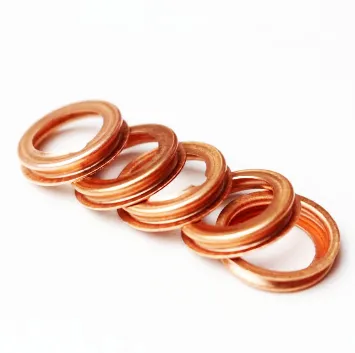
Flat face flanges are designed with the contact surface at the same level as the bolt circle. Unlike raised face flanges, they provide a consistent, broad surface area for the gasket to sit on. For this reason, non-metallic or composite gaskets are typically recommended to ensure a robust and reliable seal. Understanding which type of gasket material suits your needs requires not just technical knowledge but an understanding of the operational environment.
A widely recognized product in this domain is the non-asbestos gasket, favored for its adaptability and resilience under various conditions. Non-asbestos gaskets are produced from a composite of fibers and elastomers formulated to match, if not surpass, the properties of traditional asbestos gaskets, making them a more environmentally friendly choice. Engineers and operators in the industry trust these gaskets for their excellent compressibility and recovery, vital attributes for maintaining a seal across fluctuating pressures and temperatures.
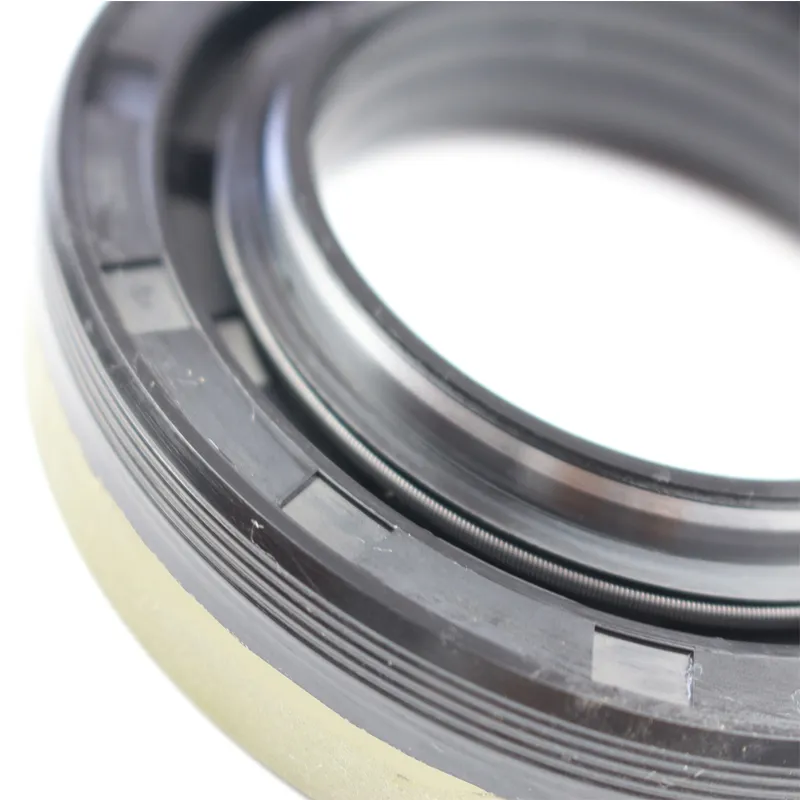
When discussing expertise and authoritativeness, one must explore the engineering behind these products. Each non-asbestos gasket is manufactured to withstand specific pressures and temperatures, commonly ranging up to 150 PSI and temperatures of 300°F or beyond, depending on the materials used. They can be made from materials including graphite, PTFE, or a combination of synthetic fibers. Graphite, for example, is prized for its thermal resistance, making it ideal for applications involving high heat or steam.
In situations requiring a more specialized approach, composite gaskets with PTFE surfaces provide superior chemical resistance, ensuring that the integrity of the seal is not compromised by harsh or reactive substances being transported through the piping system.
gasket flat face
Real-world experience in applying these gaskets reveals that over-tightening is a common installation pitfall, which can lead to premature failure of the sealing material. Proper installation involves gradually tightening the bolts in a star pattern to distribute the pressure evenly across the gasket face. This technique minimizes the potential for warping or uneven compression, which are leading causes of leaks.
Companies operating under stringent regulatory compliance often prefer to source gaskets from manufacturers certified to ISO or API standards. Such certifications imply that the gaskets produced meet high benchmarks of quality and safety, instilling trust and reliability in their performance.
Apart from technical specifications, an often-overlooked factor is the cost-efficiency linked with correct gasket selection. Improper choice can lead to frequent maintenance shutdowns, increased operation costs, and even the risk of safety hazards. Therefore, experienced engineers advocate for thorough analysis and consultation with gasket specialists during the design phase.
For organizations looking to optimize their operational integrity, partnerships with reputable manufacturers or suppliers who provide thorough testing and technical support could signify the difference between mediocre and high-efficiency performance.
Ultimately, success in industrial operations often hinges on the trustworthiness of components as foundational as gaskets. They may be small, yet their role in ensuring seamless operations and safeguarding against leaks is monumental, underscoring the value of informed selection anchored in experience, expertise, and an unwavering commitment to quality and reliability.