Flat sheet gaskets play a crucial role in various industrial applications, offering reliability and efficiency in sealing mechanisms. Often underappreciated, these components are vital in ensuring the safety and efficiency of systems involving fluid and gas containment. Understanding the intricacies of flat sheet gaskets is paramount for professionals aiming to leverage their full potential.
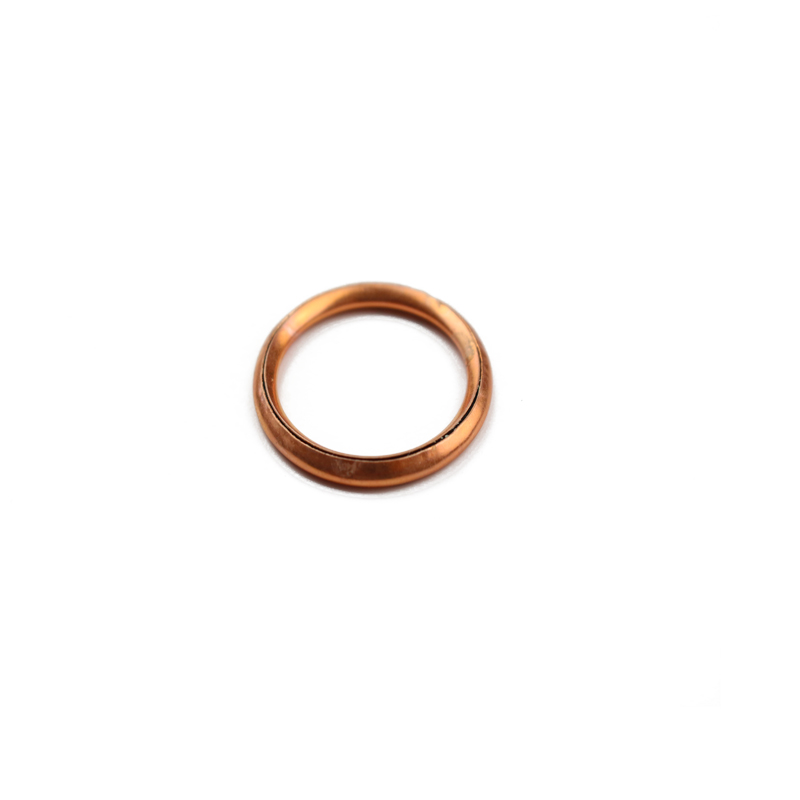
In the realm of mechanical and chemical industries, ensuring a robust seal is critical, and flat sheet gaskets, composed typically of non-metallic materials, fulfill this need. The choice of material is pivotal, given that it impacts the gasket’s temperature resistance, chemical compatibility, and longevity. Common materials include graphite, PTFE (Polytetrafluoroethylene), and fiber composites, each offering distinct advantages tailored to specific environments.
Graphite gaskets stand out for their exceptional temperature tolerance, capable of withstanding extremes from cryogenic levels to upwards of 500°C. This makes them suitable for diverse applications, from power generation to petrochemical processing. Their inherent chemical inertness further enhances their applicability in harsh environments.
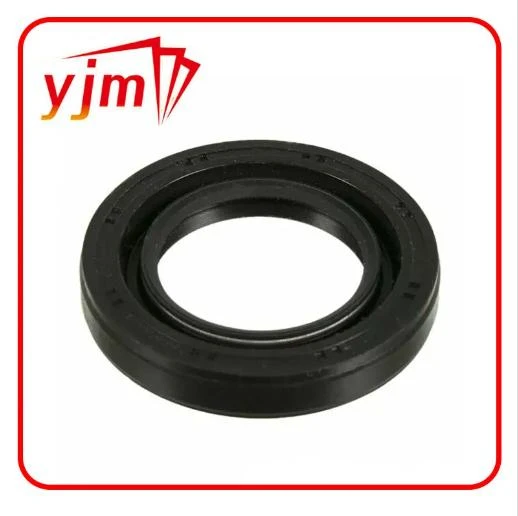
PTFE gaskets, on the other hand, provide unmatched chemical resistance, making them the go-to choice in industries where harsh chemicals are prevalent. Their non-reactive nature ensures that they maintain integrity and performance over prolonged periods, even in the presence of corrosive agents.
Fiber composite gaskets are appreciated for their versatility and cost-effectiveness. They offer a balanced performance, suitable for moderate temperature and chemical resistance conditions. This makes them an economical choice for general industrial use, balancing performance with affordability.
Expertise in selecting the appropriate type of flat sheet gasket significantly impacts operational efficiency, safety, and cost. Professional assessment should consider factors such as application pressure, temperature cycling, and the nature of the containment substance. This thorough analysis is crucial to prevent localized gasket wear, material degradation, or, worse, catastrophic seal failure, which could lead to safety hazards and costly downtime.
flat sheet gasket
Furthermore, the expertise extends to installation.
Proper alignment and torque application during installation ensure the gasket creates an optimal seal. Misalignment or uneven pressure can lead to leaks, highlighting the need for specialist skills and tools in handling these components.
From an authoritativeness standpoint, industry standards such as those put forth by ASME and ISO provide frameworks for gasket selection, testing, and application. Adherence to these standards not only ensures compliance but also boosts the credibility of operations relying on flat sheet gaskets. Leveraging these standards is a mark of professionalism and commitment to quality.
Real-world experiences underline the importance of routine inspections and maintenance schedules. Periodic evaluations prevent overlook issues like compression set or creep relaxation, which can compromise seal integrity over time. Implementing a proactive maintenance culture is vital for extending the life span of gaskets and ensuring uninterrupted operations.
Trustworthiness in using flat sheet gaskets is augmented by selecting reputable manufacturers and suppliers who adhere to stringent quality controls. These entities often provide guarantees and certifications that assure the reliability of their products, allowing industrial players to focus on their operations with confidence.
In conclusion, flat sheet gaskets, often viewed as peripheral components, are lynchpins in maintaining the integrity of fluid handling systems. Their selection, application, and maintenance require a synergy of experience, expertise, authority, and trustworthiness to fully realize their benefits. As industries evolve, so too must our approaches to these seemingly simple yet complex components, ensuring they meet emerging demands and standards.