Flat rubber seals play a crucial role in various industrial and domestic applications, offering an exceptional level of sealing effectiveness and durability. As someone who has spent years delving into the intricacies of sealing technology, I can confirm that choosing the right seal is imperative for ensuring long-lasting performance and preventing leakage-related issues.
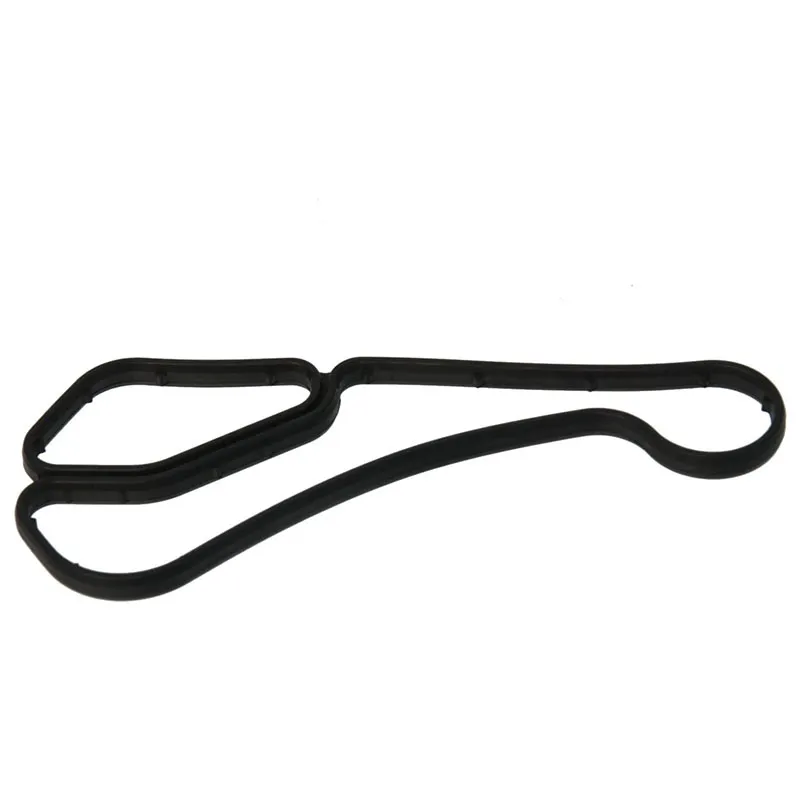
Rubber seals are particularly valued in automotive, plumbing, and machinery applications, owing to their flexibility and resilience. The flat rubber seal, in particular, stands out due to its versatility in providing airtight and watertight solutions. These seals are fabricated from high-quality materials such as EPDM, Nitrile, or Silicone, each offering unique properties suited to specific environments. For instance, EPDM is known for its superior resistance to UV and ozone, making it ideal for outdoor applications, while Nitrile is preferred for oil-resistant applications.
To ensure optimal utilization of flat rubber seals, it is essential to understand the specific requirements of your application. From my expertise, I've noticed that a common mistake is overlooking the environment where the seal will be used. Factors such as temperature fluctuations, exposure to chemicals, and pressure conditions can significantly impact the performance of the seal. For example, a seal that works well in low-pressure systems might fail in high-pressure environments due to inadequate compression resistance.
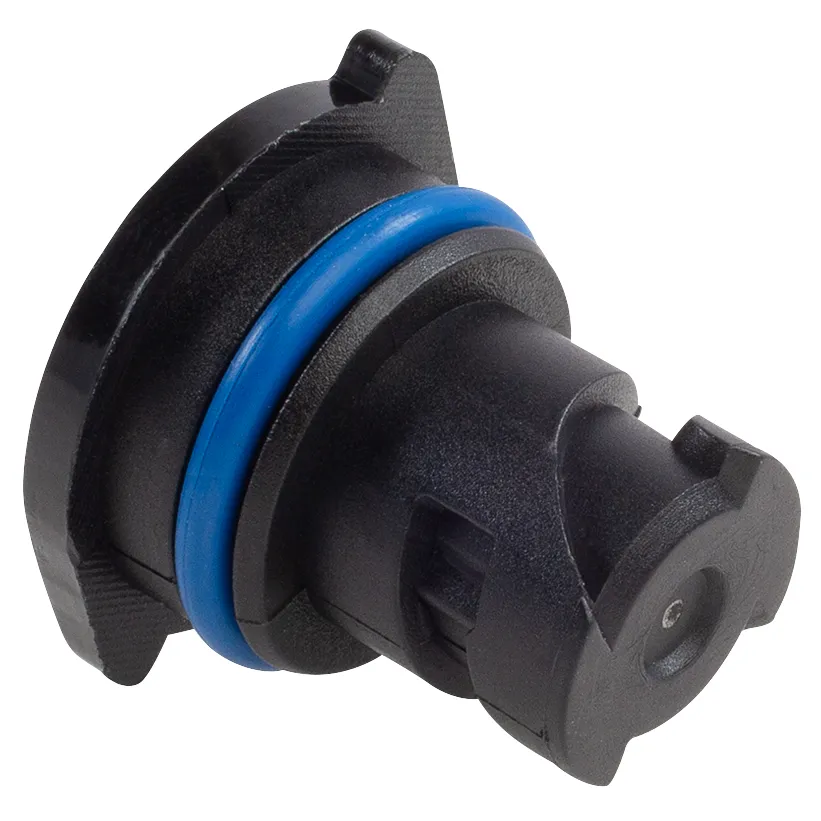
Newer advancements in rubber technology have further enhanced the performance capabilities of flat rubber seals. Some manufacturers now offer seals with advanced coatings that enhance chemical resistance and reduce friction, leading to prolonged lifespan and efficiency. Keeping abreast of these technological advancements is crucial for professionals looking to optimize their sealing solutions.
When selecting a rubber seal, consider the compatibility with the substances it will come into contact with. Seals that are not compatible can degrade quickly, leading to failures and costly downtime. My professional experiences underscore the importance of consulting material compatibility charts and, when in doubt, seeking expert advice or contacting the manufacturer. Not only does this ensure the durability of the seal, but it also fortifies trust in the product's performance.
flat rubber seal
Performance testing is another critical aspect that should not be overlooked. Reliable manufacturers typically subject their products to rigorous testing protocols to guarantee quality assurance. These assessments may include tensile strength, elongation, and compression set tests. Having access to test certificates or performance data can provide peace of mind and is often a mark of the seal's credibility and the manufacturer's authority in the market.
In addition to functionality, installation practices must also be precise to avoid compromising the seal's performance. Proper alignment and even distribution of pressure across the seal's surface are fundamental to achieving the desired sealing effect. It's advisable to refer to installation manuals or engage with professional installers to ensure every step is meticulously followed.
Investing in high-quality flat rubber seals not only guarantees sealing efficiency and longevity but also mitigates potential risks and costs associated with maintenance and replacements. By leveraging your understanding of material properties, environmental conditions, and installation techniques, you can achieve optimal sealing solutions tailored to your specific needs.
The importance of flat rubber seals can't be overstated, given their multifaceted applications and the myriad solutions they offer across industries. Selecting the right seal involves more than just understanding material properties; it combines expertise, authoritative knowledge, and a trustworthy approach to achieve exceptional application results. As these seals continue to evolve, staying informed about the latest innovations and standards can significantly impact their successful deployment in any project.