Flat round rubber gaskets are small yet pivotal components used in various industries, delivering essential sealing solutions that protect machinery, maintain safety, and enhance performance. These gaskets, often overshadowed by more prominent machinery parts, provide an unparalleled utility. Understanding their application, material composition, and the factors influencing their selection can lead to substantial improvements in operational efficiency and cost savings.
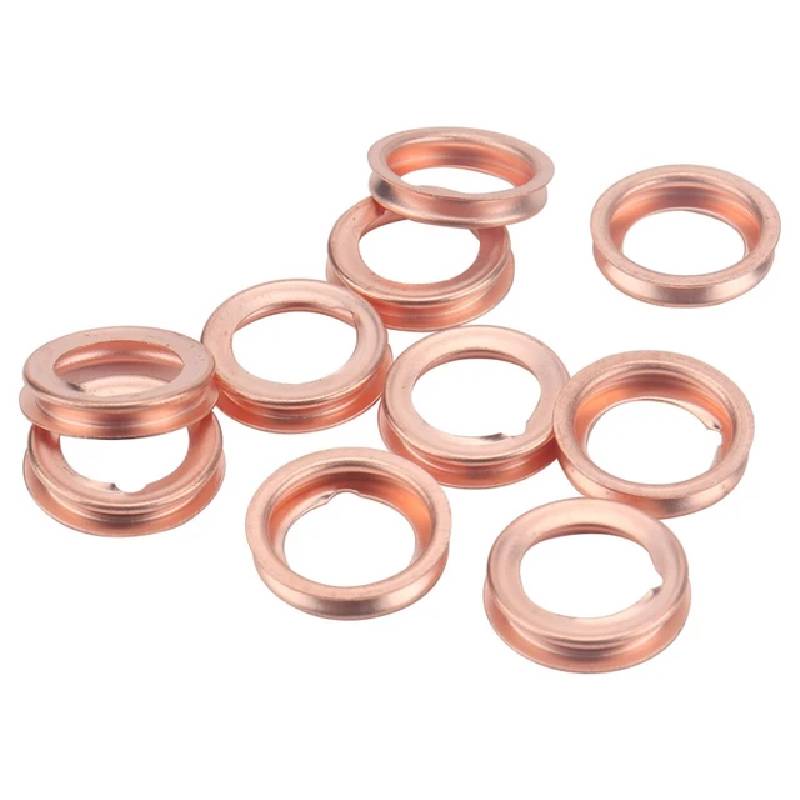
Industries ranging from automotive to plumbing extensively utilize flat round rubber gaskets. In automotive engines, these gaskets act as a crucial barrier against fluid leaks, preventing oil, coolant, and air from escaping. The unique property of rubber to flex and return to its original shape allows it to create a near-perfect seal. When crafting high-performance engines, using precisely engineered rubber gaskets helps maintain peak performance and cut down on emissions by ensuring no adulteration of fluids or gases.
In the plumbing industry, rubber gaskets are indispensable in maintaining water-tight seals in pipes and fixtures. The resilience of rubber to withstand high pressure and diverse temperature ranges makes these gaskets suitable for both hot and cold water systems. By choosing the right rubber gasket, plumbers can avoid potential leaks, ensuring the sustained integrity of piping systems without frequent maintenance.
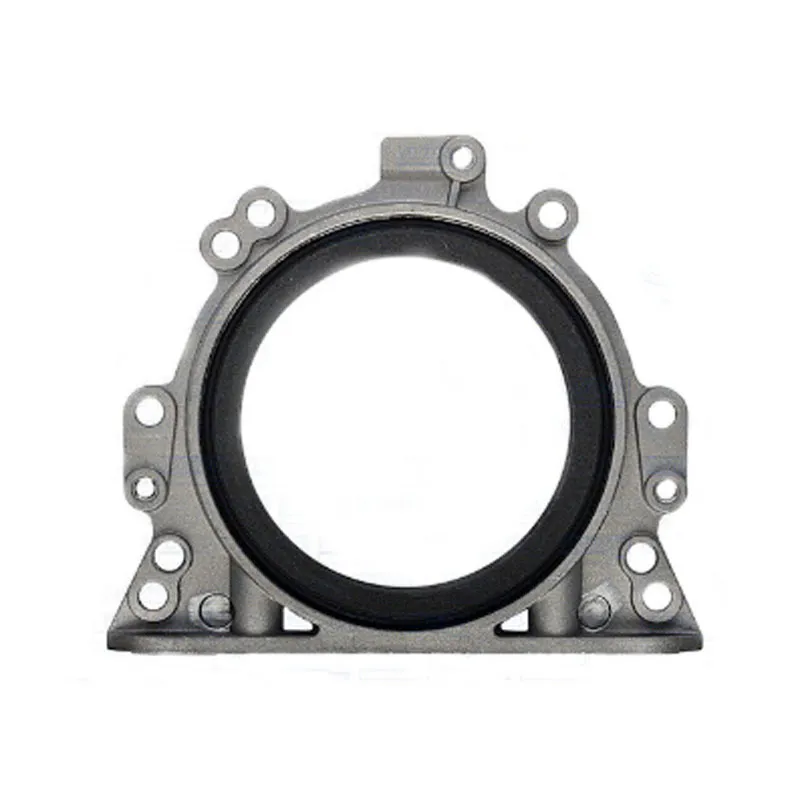
The selection of the appropriate rubber material is crucial in ensuring the longevity and effectiveness of the gasket. Common rubber types used for gaskets include neoprene, nitrile, EPDM, and silicone, each offering distinct advantages. Neoprene, for instance, is renowned for its resistance to oil and ozone, making it ideal for automotive and outdoor applications. Similarly, nitrile is preferred for systems where resistance to oil, fuel, and other chemicals is necessary. EPDM is famous for its excellent resistance to weather, ozone, and UV rays, making it a prime choice for outdoor and automotive applications. Silicone gaskets are employed where high-temperature resistance is crucial, often appearing in food processing and medical industries.
flat round rubber gaskets
Choosing the right rubber gasket also hinges on understanding the specifics of the application, such as the pressure, temperature, and the nature of the substances involved. For example, in high-temperature applications, a silicone gasket may outperform other options by maintaining its properties without degradation. This expertise ensures that industries selecting the appropriate gasket type can enhance the durability and functionality of their systems.
Attention to detail in the manufacturing process further increases the reliability and performance of rubber gaskets. Quality control procedures, including testing for tensile strength, hardness, and compression set, help ensure that the gaskets meet the required specifications. Manufacturers with a reputation for high-quality production and compliance with international standards offer increased assurance of gasket reliability.
Moreover, sustainable practices in the manufacturing process of rubber gaskets are gaining traction, with many companies seeking to minimize their environmental impact. Using recyclable materials and eco-friendly production methods not only cuts down on waste but also enhances the brand's image and trustworthiness in eco-conscious markets.
In conclusion, flat round rubber gaskets, although seemingly minor, are indispensable in a wide array of applications across multiple industries. Their role in ensuring safety, efficiency, and longevity of systems cannot be understated. With advances in material science and manufacturing technology, the future holds further enhancements in the capabilities of these unsung heroes, promising even greater reliability and efficiency. Understanding the nuances in gasket selection and application can lead to significant operational improvements, setting the standard for excellence in industrial applications.