A flat ring gasket is an indispensable component in various industrial applications, revered for its ability to provide a reliable seal between two surfaces. Drawing on years of experience across multiple sectors, it becomes evident that selecting the right flat ring gasket can make a significant difference in operational efficiency and safety.
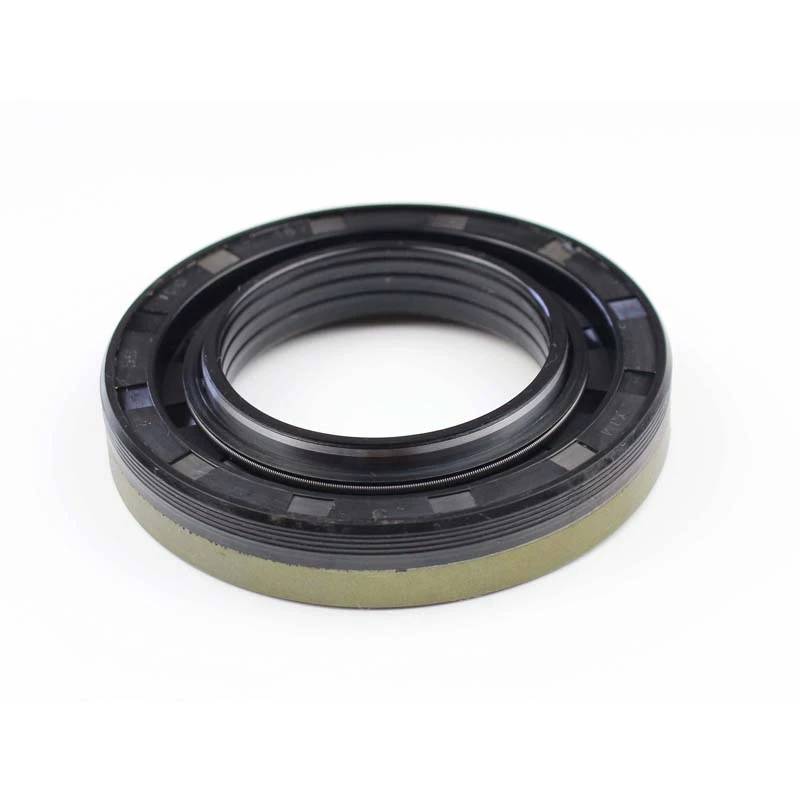
Flat ring gaskets are integral to machinery's optimal functioning, from manufacturing plants to automotive engines. These circular sealants are designed to withstand diverse pressures, temperatures, and chemical exposures, ensuring that leaks and systemic failures are prevented. But beyond the surface-level understanding, the depth of expertise required to select and implement the right gasket should not be underestimated.
One of the primary considerations when choosing a flat ring gasket is the material composition. Material selection is critical because it directly impacts the gasket's resistance capabilities and durability. For example, gaskets made from rubber elastomers such as Nitrile or Neoprene are commonly used for applications involving lower temperatures and non-aggressive chemicals. Meanwhile, PTFE gaskets are advantageous for environments that require high chemical resistance and temperature ranges. This expertise in material science underlines their application suitability, aligning with the specific needs of every sector.
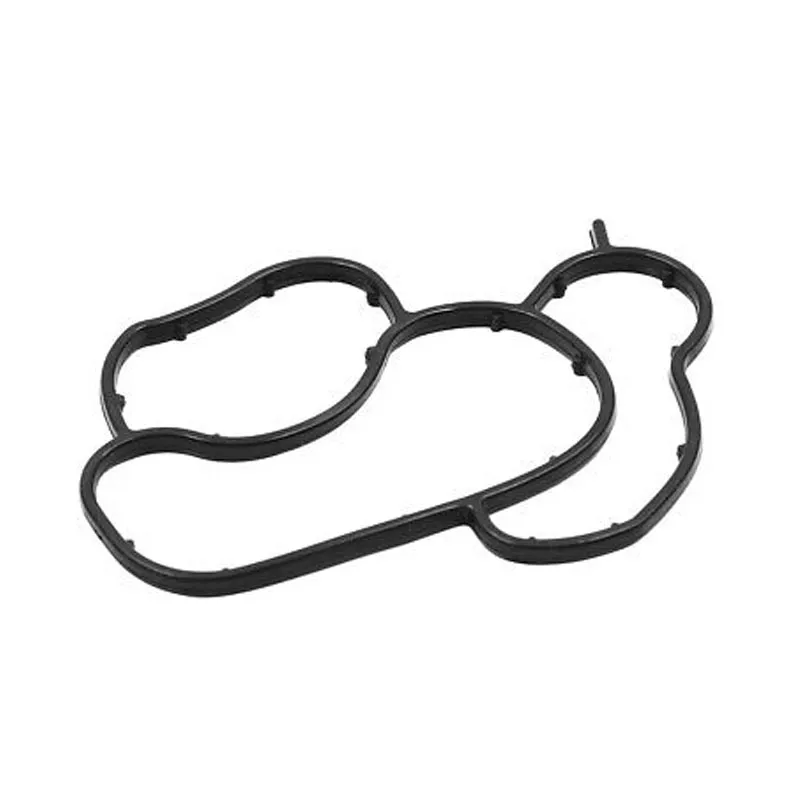
Furthermore, the integrity of a flat ring gasket is influenced significantly by its manufacturing process. Advanced techniques, such as CNC machining or waterjet cutting, produce precision-engineered gaskets, ensuring a perfect fit and superior seal. This precision in manufacturing is paramount, especially when used in critical applications like aerospace or pharmaceuticals, where even the smallest leaks can lead to catastrophic consequences. Hence, the authoritative knowledge in selecting manufacturers who employ cutting-edge technology and adhere to stringent quality standards is invaluable.
Trustworthiness in a gasket's performance is also closely linked to adherence to industry standards. Reputable gasket suppliers ensure that their products comply with international standards such as ASME, DIN, or ISO. This compliance not only certifies the gasket's quality and performance but also reinforces trust in safety-critical applications. Engineers and procurement managers must prioritize suppliers that provide full transparency regarding their compliance certifications.
flat ring gasket
In practical terms, the installation of a flat ring gasket demands more than just placement between two flanges. Expertise in installation ensures that the gasket is seated correctly and achieves full face contact without any undue stress on a particular section. Proper torque application during bolting is essential to achieve uniform compression, preventing deformities that could lead to leaks. This process requires a high level of expertise and often benefits from use of advanced tools such as hydraulic tensioning systems.
Moreover, flat ring gaskets are not immune to degradation. Real-world experience has shown that regular maintenance checks and timely replacements are crucial for long-term reliability. Attention must be paid to visual inspections for signs of wear and tear, such as cracking or flattening, which can compromise gasket integrity. Leveraging experience in preventive maintenance can extend the lifespan of equipment and prevent costly downtimes.
The integration of technology in monitoring gasket performance is an emerging trend. Some industry leaders are experimenting with IoT devices that monitor temperature, pressure, and vibration levels in real-time, offering predictive analytics on gasket health. This confluence of technology and expertise enhances the trustworthiness of the operational processes, positioning them at the frontier of innovation and reliability.
In conclusion, the selection, installation, and maintenance of flat ring gaskets demand a robust understanding of material science, engineering principles, and technological advancements. With expert guidance and adherence to industry standards, businesses can safeguard their operations, mitigate risks, and maximize longevity and efficiency. Therefore, investing in high-quality flat ring gaskets and competent expertise is not just a necessity but a strategic priority for any industry reliant on robust sealing solutions.