Flat gaskets have increasingly become a vital component in various industrial and consumer applications due to their ability to provide effective sealing solutions. Their efficiency in sealing makes them paramount across sectors such as automotive, plumbing, aerospace, and manufacturing. As someone deeply entrenched in the world of gaskets and seals, it is evident that the choice of a flat gasket must be informed by a sound understanding of their characteristics, material composition, and the specific needs of your application.
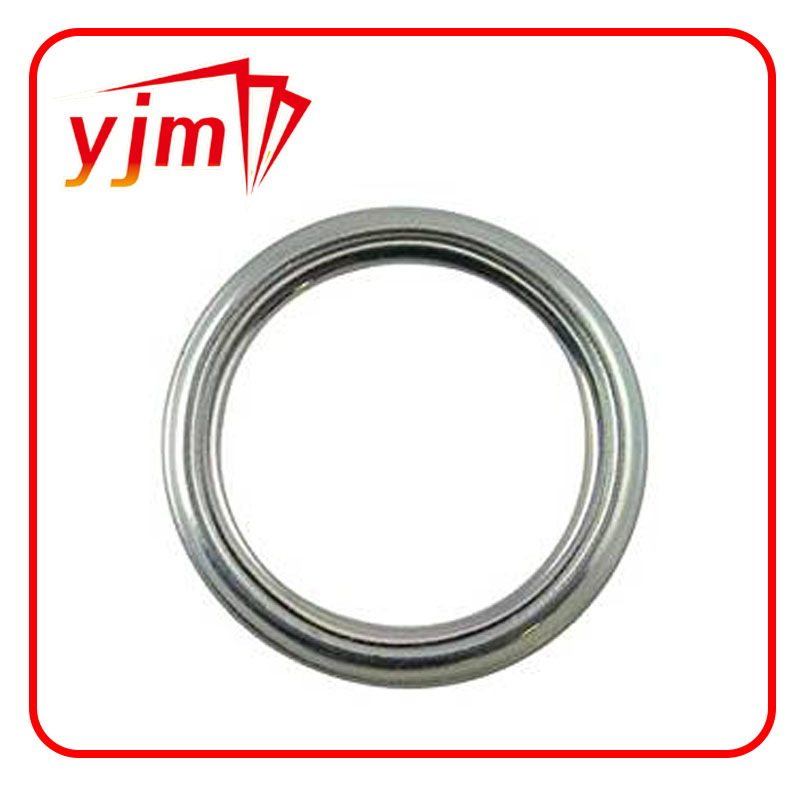
Flat gaskets are primarily noted for their simplicity and wide applicability in sealing two juxtaposed surfaces. One cannot overstate their reliability when it comes to preventing leaks of gases and liquids—critical in maintaining the integrity of mechanical systems. Engineered for versatility, flat gaskets are fabricated from an array of materials, each optimized for particular applications. This includes but is not limited to rubber, PTFE, graphite, and metal—each offering unique properties such as resistance to extreme temperatures, pressures, and chemical interaction.
In my extensive experience with industrial sealing technologies, I have observed that the choice of gasket material significantly dictates the performance and longevity of the seal. For instance, graphite flat gaskets are exceptional for high-temperature environments due to their resilience and thermal stability. Conversely, PTFE gaskets are preferred where chemical inertness is a priority. Thus, when selecting a flat gasket for a specific purpose, one must evaluate the operational environment's chemical, thermal, and physical demands to ensure optimal performance and durability.
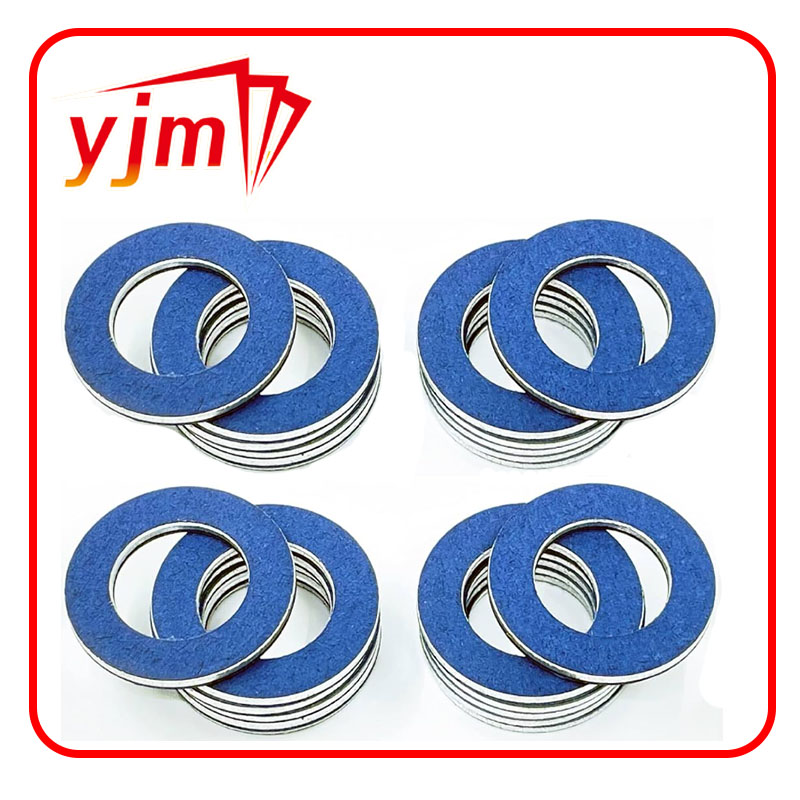
Expertise in gasket application is further demonstrated through the understanding of gasket standards and specifications. Compliance with leading standards such as those from the American National Standards Institute (ANSI) or the International Organization for Standardization (ISO) is crucial. These standards dictate everything from material properties to their pressure and temperature ratings, ensuring safety and efficiency within our systems. Gasket manufacturers often provide comprehensive specification sheets, which are indispensable for making informed decisions.
flat gasket
The authoritativeness of flat gaskets is reinforced through rigorous testing and research into their performances under different conditions. Industry leaders often conduct comprehensive tests to examine factors like compression set, tensile strength, and creep relaxation. Such tests not only validate the gasket's suitability for intended applications but also bolster consumer confidence in their reliability and durability.
Trustworthiness in the use of flat gaskets is equally vital. It is reassuring to know that when a high-quality flat gasket is installed correctly, it offers long-term solutions with minimal maintenance needs. My professional recommendation for ensuring gasket trustworthiness involves selecting products from reputable manufacturers with proven track records.
This ensures access to gaskets that not only meet but often exceed industry standards.
In conclusion, flat gaskets remain indispensable tools in modern engineering and manufacturing. Their simplicity and efficacy have cemented their role in providing reliable sealing solutions across diverse fields. With a wealth of materials and specifications available, professionals can select the optimal flat gasket that aligns perfectly with their project's unique demands. By focusing on the critical aspects of material selection, compliance with standards, rigorous testing, and choosing reputable manufacturers, one can ensure that installed flat gaskets will deliver top-tier performance and reliability. In doing so, industries across the globe can maintain efficient, leak-proof systems, safeguarding both their operations and the environment.