Oil hub seals play a pivotal role in the performance of modern machinery across various industries. These components, though small in size, are integral in ensuring the efficient operation of equipment, minimizing maintenance costs, and prolonging the lifespan of machinery. Their primary function is to prevent oil leaks and keep contaminants away from sensitive parts of machines such as wheel hubs, pumps, and motors.
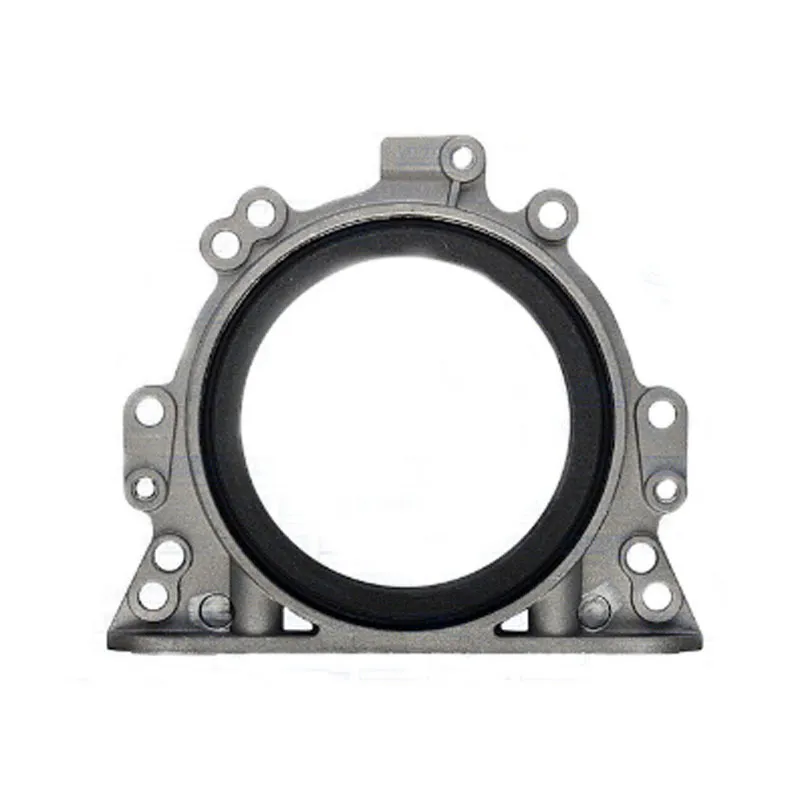
Experience in the field of industrial machinery highlights the importance of selecting and maintaining high-quality oil hub seals. Routine maintenance and occasional inspections can uncover wear and tear issues before they lead to larger, more expensive problems. A common mistake made by operators is neglecting seals during regular upkeep, which can result in significant downtime if a failure occurs. Understanding the intricacies of different types of seals, such as rotary shaft seals or labyrinth seals, and their appropriate use cases, can prevent such situations.
From an expertise standpoint, oil hub seals come in various materials and designs, each suited to specific applications. For example, seals made of nitrile rubber are effective for general purposes, enduring temperatures from -40°C to 120°C and resisting wear in environments where water and oils are present. In contrast, when dealing with more extreme temperatures or aggressive chemicals, Viton or silicone seals might be necessary. The selection of a suitable material directly correlates with the operational efficiency and longevity of equipment.
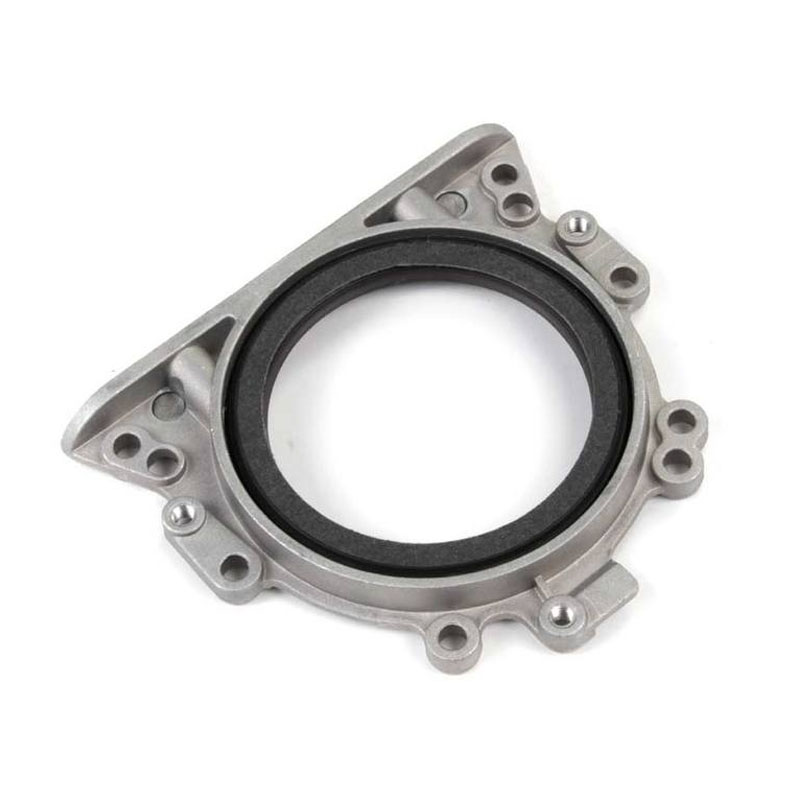
oil hub seal
Manufacturers and engineers often highlight the authoritativeness of using OEM (Original Equipment Manufacturer) parts when replacing oil hub seals. Although imitation parts may be enticing due to cost, they often lack the rigorous testing and quality assurance processes that OEM parts undergo. These standardized tests ensure that OEM seals can withstand specific pressures, temperatures, and environmental conditions likely to be encountered. Using OEM parts not only enhances performance but also aligns machines with warranty requirements, providing peace of mind for operators.
Trustworthiness in oil hub seal performance also revolves around proper installation techniques. Misalignment, over-tightening, or improper lubrication during installation can cause immediate seal failure or premature wear. Seeking guidance from trusted sources, such as manufacturer guidelines and certified technicians, is essential to guarantee the longevity of a new seal. Educational workshops and certified training programs for maintenance personnel can further reinforce correct practices, reducing human errors and ensuring consistent performance.
In summary, the vital role of oil hub seals in machinery cannot be overstated. Their contribution to reducing oil leakage, protecting against contaminants, and sustaining machinery operation underscores the need for high-quality materials, informed selection, and professional installation. As technology evolves, continuous advancements in seal technology, such as those utilizing renewable materials or enhanced friction-reduction properties, will further optimize their performance. For equipment operators and managers, prioritizing the integrity of these small, yet significant components translates into considerable savings in operational costs and enhanced machinery reliability.