The double lip shaft seal, a seemingly simple component of machinery, holds a place of paramount importance in various industries including automotive, marine, and manufacturing. Its prime functionality—to prevent leakage and maintain optimal lubrication—ensures the efficiency and longevity of equipment. As industrial applications and technological innovations evolve, understanding the nuances of this seal, its applications, and maintenance has never been more integral.
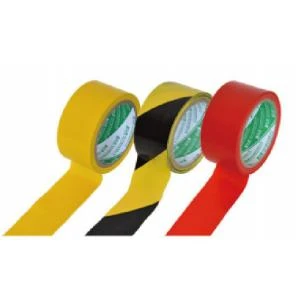
In practical experience, the double lip shaft seal impresses with its dual-lip design. While the primary lip ensures that fluids retain their place within a system, preventing leaks, the secondary lip acts as a guardian against external contaminants such as dust, mud, and debris. This dual functionality extends the life of the seal itself, as well as the components it protects. For example, in the automotive industry, where shaft seals are exposed to varying temperatures and contaminant levels, their capability to prevent external contamination while resisting internal fluid leaks can greatly enhance the lifespan of automobile parts, reducing maintenance costs and ensuring driver safety.
Expertise in the selection and implementation of double lip shaft seals is crucial to optimize their performance.
Material selection plays a decisive role in the seal's effectiveness. Nitrile rubber is commonly used for general purposes due to its good wear resistance and reasonable temperature range. However, for applications involving extreme temperatures or aggressive media, fluoroelastomers or silicone materials might be recommended. Precise selection considers the operating environment, including temperature ranges, fluid types, and pressure conditions. Failure to consider these factors can lead to premature seal failure and increased equipment downtime.
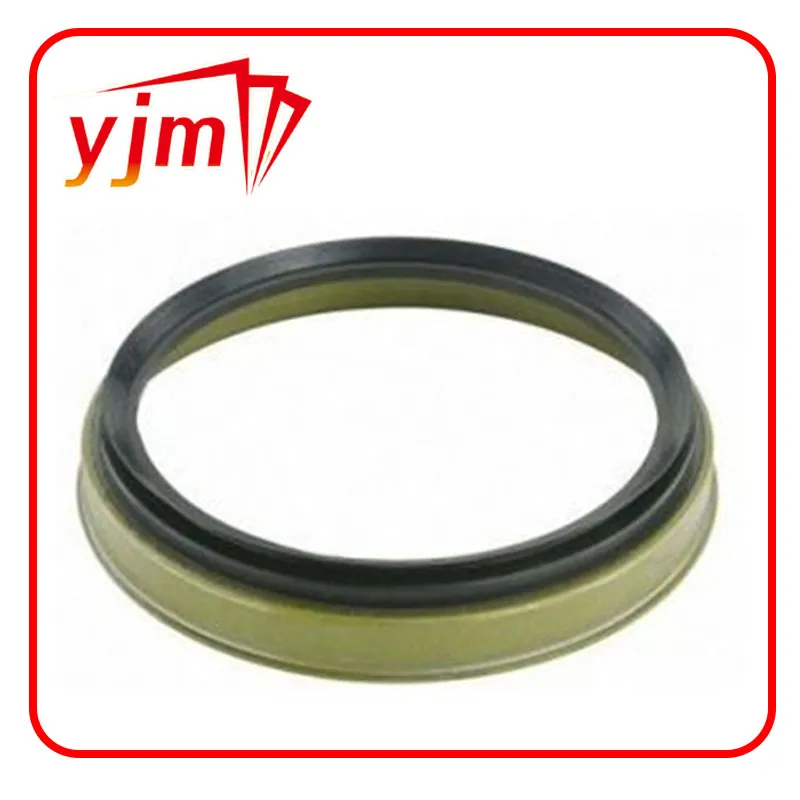
Authoritativeness in the domain of double lip shaft seals is enforced by various industry standards and regulations. Organizations such as the Society of Automotive Engineers (SAE) and International Organization for Standardization (ISO) have set guidelines to ensure seals meet specific performance criteria. Compliant seals not only offer superior performance but also instill confidence in users regarding their reliability. Industry professionals and engineers adhere to these standards for selecting and testing seals to ensure they meet or exceed operational demands.
double lip shaft seal
Trustworthiness, the final component, stems from proven performance and adherence to best practice maintenance. Regular and meticulous inspection of the seals for signs of wear, such as cracking, flattening, or hardening, ensures they function as intended. Moreover, understanding that a seal's lifespan can be affected by shaft surface finish, eccentricity, and improper installation underscores the importance of professional installation and maintenance. Users must regularly measure shaft conditions and verify alignments to prevent undue strain upon the seal, thereby maximizing its service life.
In terms of emerging innovations, advances in seal materials and designs are noteworthy. Novel polymer composites and self-lubricating materials promise to revolutionize the industry. These materials can offer enhanced chemical resistance and reduce friction, further extending the lifespan of both the seals and the machinery they protect. Additionally, the integration of sensors within seals to monitor real-time performance indicators could be a game-changer, paving the way for predictive maintenance and reducing the risk of unexpected machinery failure.
The double lip shaft seal, simple yet sophisticated, exemplifies the intricate engineering that keeps machines across industries running smoothly and efficiently. With careful consideration of material suitability, compliance with established standards, and rigorous maintenance practices, the use of these seals can contribute significantly to operational success. As industries lean more towards automation and smarter systems, the adaptability and resilience of double lip shaft seals affirm their irreplaceable role in modern mechanical systems.