Oil seals, commonly known as rotary shaft seals, are crucial components in various industries, ranging from automotive to manufacturing. They play a vital role in maintaining lubrication, preventing contamination, and ensuring smooth operation within systems. Understanding the different types of oil seals is essential for selecting the right product for specific applications, enhancing equipment longevity and efficiency.
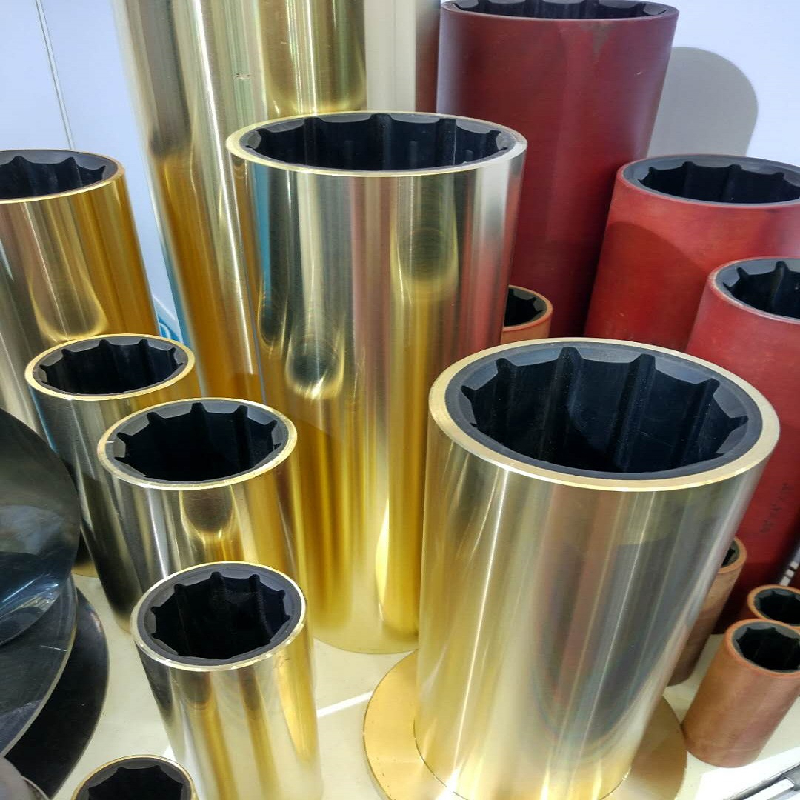
Oil seals are designed to close spaces between stationary and moving components and are primarily used to retain lubricants while keeping contaminants at bay. They achieve this by employing different sealing elements, which vary depending on the seal type, composition, and intended use.
Let's delve into the diverse categories of oil seals and their specific applications.
Radial Oil Seals are the most common type, featuring a flexible lip that maintains contact with a rotating shaft. They are typically used in high-speed applications, such as automotive engines and industrial machinery. These seals are designed to handle both high and low-pressure environments, making them versatile for various industries.
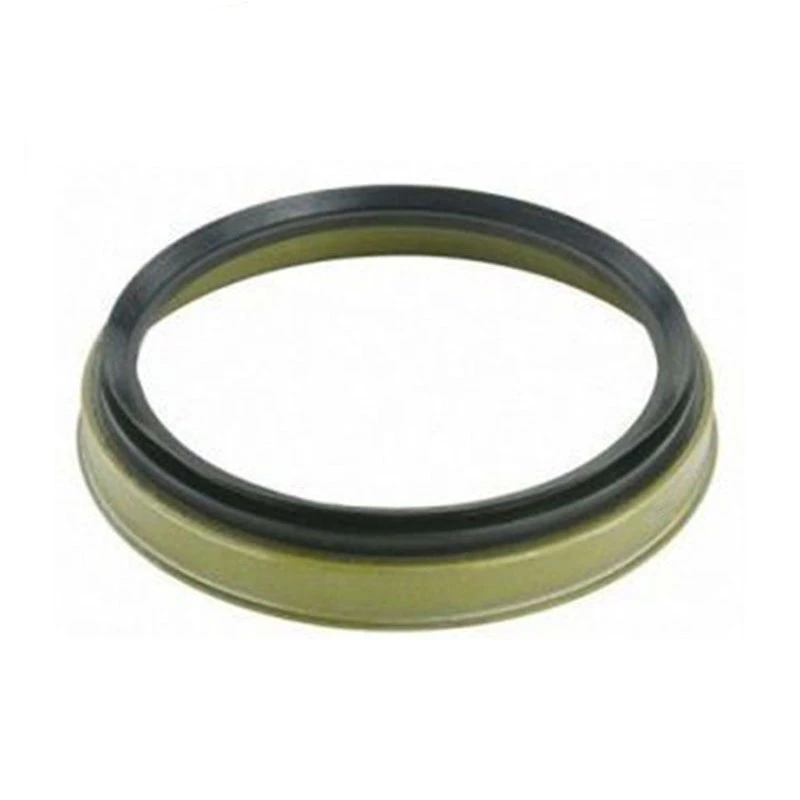
Axial Oil Seals, unlike their radial counterparts, are designed to work with axial motion. They are ideal for applications where there is a significant axial displacement between the components. These seals are commonly used in applications like oscillating mechanisms or linear actuators where radial seals might not perform effectively.
U-cup Seals are another variety, particularly favored in hydraulic and pneumatic applications. Their U-shaped lip design provides an excellent seal performance, especially in dynamic applications where bidirectional operation is required. These seals are appreciated for their ability to adapt to pressure fluctuations, ensuring reliability over prolonged use.
different types of oil seals
V-ring Seals are unique because they fit directly on the shaft and rotate with it, without contacting the housing. This makes them an excellent choice for sealing against dust, dirt, or water from entering into bearings, particularly in agricultural machinery where such external contaminants are prevalent.
End Cap Seals serve a dual purpose by acting as both a seal and a protective end cover for rotating shafts. They are perfect for sealing housings in gearboxes and other stationary structures, offering both dust prevention and lubricant retention to ensure efficient operation of machinery.
Metal-Faced Seals, sometimes referred to as cassette seals, incorporate a metal housing that provides enhanced protection against external impacts and abrasions. Their robust design makes them ideal for extreme environments, such as construction equipment and mining operations where they prevent the ingress of harsh substances and debris.
Material composition is critical when selecting oil seals, as the environment and type of medium encountered have significant implications on the seal's durability and performance. Nitrile rubber is popular due to its cost-effectiveness and resistance to oil and grease. However, for applications involving higher temperatures or chemically aggressive environments, materials like fluorocarbon (Viton) or silicone should be considered due to their superior resistance properties.
In conclusion, selecting the appropriate oil seal requires a comprehensive understanding of the application's mechanical and environmental demands. By acknowledging the unique features of each seal type and carefully considering their material composition, industries can substantially reduce downtime, extend machinery lifespan, and improve overall efficiency. Employing high-quality oil seals results in trustworthy performance and long-term cost savings, underscoring their indispensable role in machine maintenance and operational success.