Understanding the intricacies of bonded seal dimensions is crucial for industries reliant on high-pressure systems and certified sealing solutions. Bonded seals, often dubbed 'washers with an attitude,' play critical roles in the engineering landscape due to their enhanced sealing capabilities. This is primarily attributed to their unique structure a metal washer and a vulcanized elastomeric sealing lip. As automation and optimization continue to shape manufacturing processes, the emphasis on precision in the dimensions of bonded seals cannot be overstated.
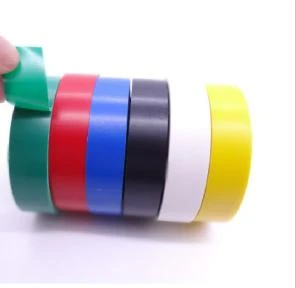
The dimensions of a bonded seal—specifically, its inner diameter (ID), outer diameter (OD), and thickness—are pivotal. Each dimension must be tailored to precisely fit the application it is meant for. Incorrect sizing can lead to inefficient sealing, resulting in potential leakage, system failures, or compromised safety standards. As a professional who has studied various industrial applications, the criticality of selecting the right bonded seal size becomes apparent through hands-on experience.
Experts in mechanical engineering assert that the bonded seal's dimensions directly influence its performance under pressure and varying temperatures. To illustrate,
consider the inner diameter. This particular dimension is essential in ensuring that the bonded seal correctly fits around a bolt or pipe it is meant to secure. A seal that is too tight could impede installation, while one too loose could diminish its ability to provide a proper seal. It's a delicate balance that only trial, error, and expert input can perfect.
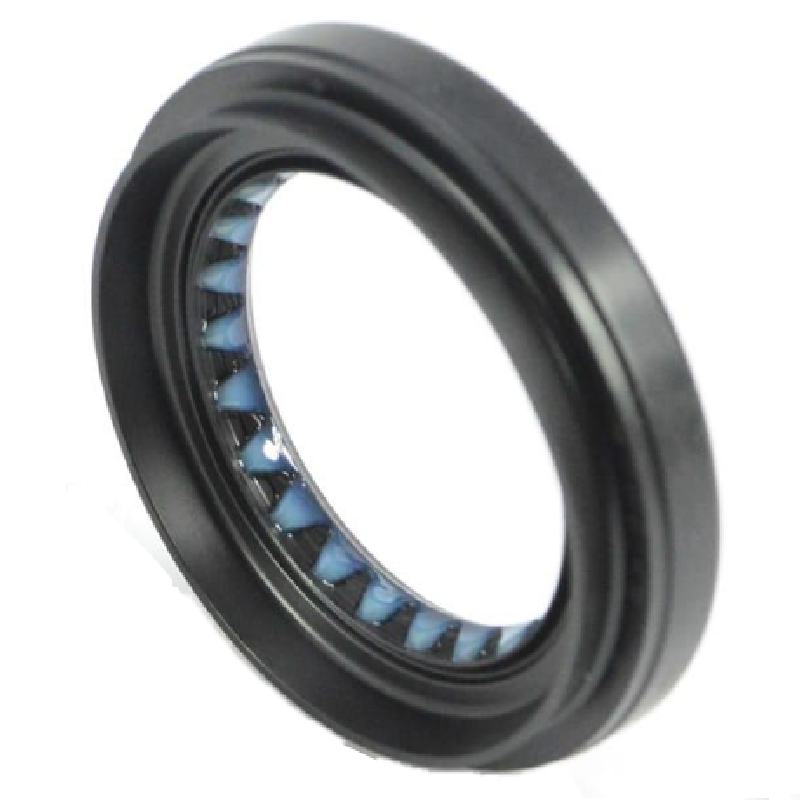
The outer diameter, by contrast, interacts more directly with the housing or cavity in which the seal rests. This dimension helps in maintaining the seal's position and preventing any displacement during operation. Industry standards often dictate a slight interference fit, meaning the OD should be marginally larger than the cavity it sits within. This provides the necessary compression for the elastomeric lip to engage effectively with the mating surfaces.
Thickness, often the unsung hero, dictates the seal's ability to resist extrusion and remain resilient under operational stressors. A well-calibrated thickness ensures that the seal withstands pressure differentials and surface irregularities without succumbing to deformation. The expertise of material scientists has dramatically advanced the elastomer compounds used, leading to seals that maintain integrity even in harsh environments with extreme temperature variations and exposure to chemicals.
bonded seal dimensions
In terms of authority and trustworthiness, manufacturers of bonded seals continuously engage in research and development, refining these dimensions to adhere to international standards. The rise of digital modeling and simulation tools heralds a new era where prototypes can be tested in virtual environments to ensure optimal dimensioning before physical production. This ensures reliability, as seals undergo rigorous quality control checks based on their specified dimensions, ensuring they provide consistent and reliable performance.
When selecting a bonded seal, understanding dimension specifications from technical datasheets is invaluable. These datasheets serve as the roadmap for engineers and procurement specialists, especially when custom sizes are required, as is often the case in specialized applications. The specificity of these documents highlights both the trust in accurate dimension practices and the engineering expertise applied during production.
Real-life application scenarios further underscore the importance of proper bonded seal dimensions. In hydraulic systems, where failure can lead to extensive downtime and financial losses, these seals act as guardians of system integrity. Similarly, in the petrochemical industry, their reliability is critical, where leaks not only risk environmental damage but also safety hazards.
In summary, the dimensions of bonded seals are not mere numbers; they are the backbone of performance, longevity, and safety in mechanical systems. Only through the intertwining of experience, expert knowledge, and adherence to authority-backed standards can one appreciate the true importance of selecting the correct bonded seal dimensions. Whether you are an engineer, a procurement officer, or a facility manager, a nuanced understanding of these dimensions equips you to make informed decisions that resonate with efficiency, reliability, and peace of mind for all stakeholders involved.