The bonded O-ring, despite its unassuming appearance, stands as a cornerstone component in countless industries, from automotive to aerospace, to even the food and beverage sectors. Its fundamental role in ensuring leak-proof seals in dynamic and static applications cannot be overstated, making it indispensable. This article dives deep into the workings, benefits, and distinct qualities of bonded O-rings, drawing attention to their design, uses, and the value they add to engineering and manufacturing processes.
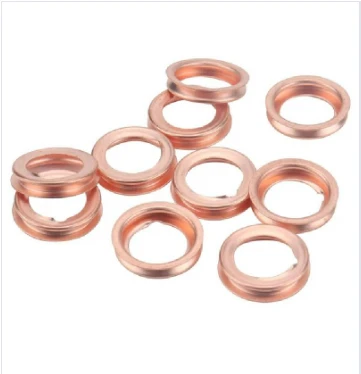
The engineering ingenuity behind bonded O-rings lies in their unique construction. Unlike traditional O-rings, bonded O-rings consist of an elastomeric ring fused to a rigid or semi-rigid material, often metal or plastic. This bonding process enhances the structural integrity of the O-ring, allowing it to withstand high-pressure environments and extreme temperature fluctuations. Such resilience is perfect for operations where traditional O-rings might fail. For engineers dealing with complex sealing systems, these advantages translate to longevity and less downtime, directly influencing productivity and cost savings.
In the realm of application, bonded O-rings demonstrate remarkable versatility. In the automotive industry, they can be found ensuring the durability of hydraulic systems or the tightness of fuel lines, where exposure to various chemicals and thermal changes are constant challenges. Similarly, in the aerospace sector, they provide essential seals in hydraulic systems and fuel systems where reliability is critical due to the extreme conditions of high altitude. Their ability to maintain a seal under significant environmental stress is a testament to the precision and expertise behind their design and manufacturing.
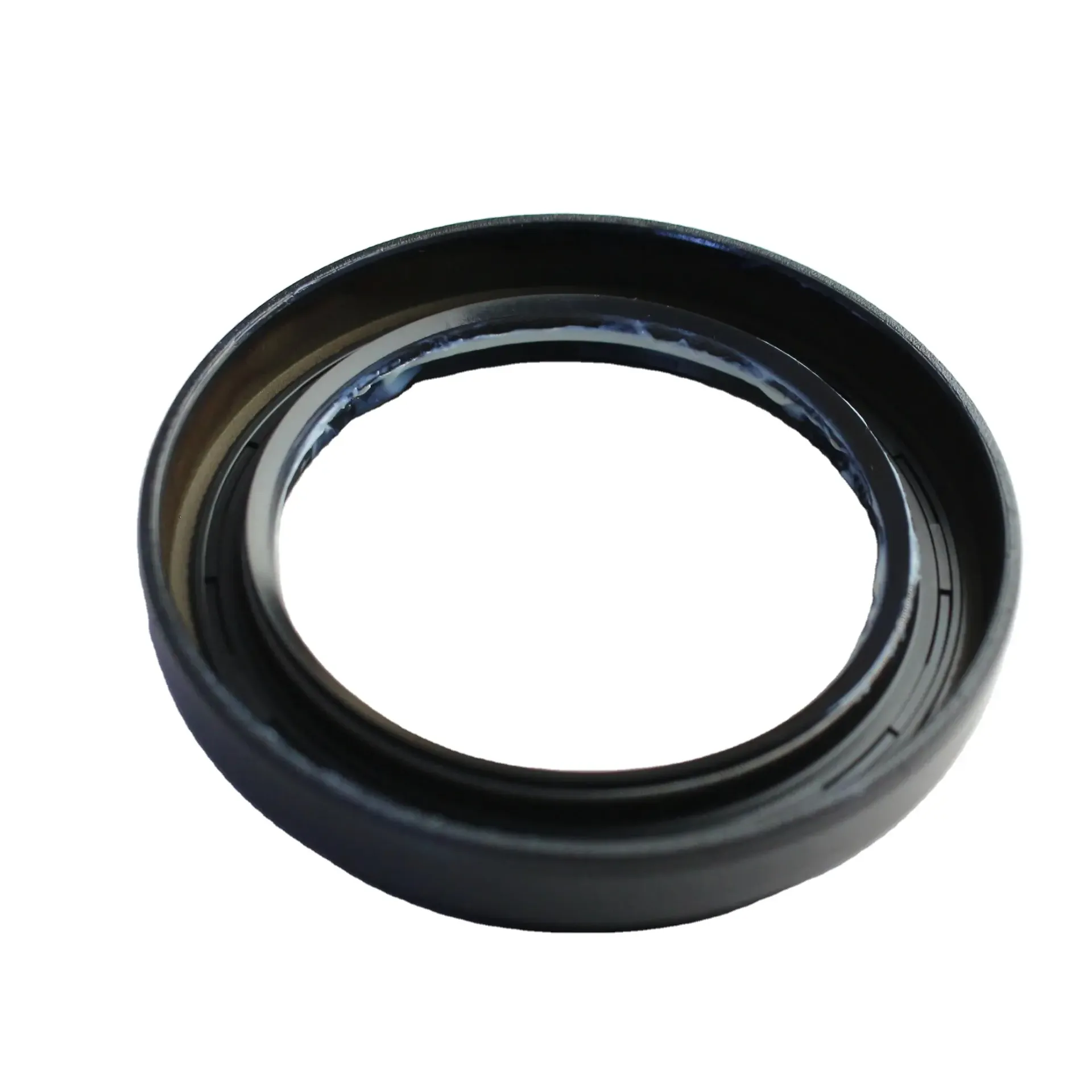
The material composition of bonded O-rings is a crucial factor in their performance. Selecting the right combination of elastomer and substrate is paramount, emphasizing the expertise required in their production. For example, in environments where chemical exposure is prevalent, fluorocarbon elastomers might be bonded to stainless steel to offer superior chemical resistance without compromising strength. Such informed material choices speak to the expertise of manufacturers who understand the unique demands of diverse industries and tailor their products to meet these challenges.
An authoritative perspective on bonded O-rings must include an acknowledgment of the rigorous testing they undergo. Companies adhering to international standards such as ISO and ASTM ensure that these O-rings meet stringent performance criteria. This dedication to quality control not only enhances the product’s reliability but also establishes trust with consumers who rely on these components for their critical operations.
bonded o ring
Moreover, trustworthiness in the supply chain of bonded O-rings is reinforced by transparency and compliance with industry regulations. Many manufacturers now offer detailed traceability for their products, providing insights into the production process—from raw material sourcing to the final product. This level of transparency has become increasingly important for industries like aerospace and pharmaceuticals, where adherence to safety standards is non-negotiable.
The push towards sustainability has also influenced the landscape of bonded O-ring manufacturing. As industries strive for more eco-friendly practices, modern manufacturing methods have adapted, with many producers seeking out sustainable materials or implementing greener production processes. This shift not only benefits the environment but opens up new pathways for innovation in material science, further enhancing the performance attributes of bonded O-rings.
Real-world experience with bonded O-rings affirms their critical role across various applications. Feedback from industries consistently highlights improvements in efficiency and reduction in maintenance when using these components. The enduring performance and reliability of bonded O-rings often lead to their selection over traditional sealing methods, and as innovations in materials and bonding techniques continue, their prevalence is set to grow.
In summary,
bonded O-rings epitomize engineering excellence and adaptability. Their design showcases a fusion of material science and precision engineering, embodying expertise and innovation. Through rigorous quality standards and a commitment to sustainable practices, these O-rings remain a trusted solution across multiple sectors, establishing themselves as a pivotal element in the machinery and systems that underpin modern industry.