Understanding the significance of an axial shaft seal in industrial applications is crucial for maintaining equipment efficiency and longevity. In the complex world of mechanical engineering, these seals ensure that machinery operates smoothly, free from the potential dangers of fluid leakage which can lead to equipment damage or environmental hazards.
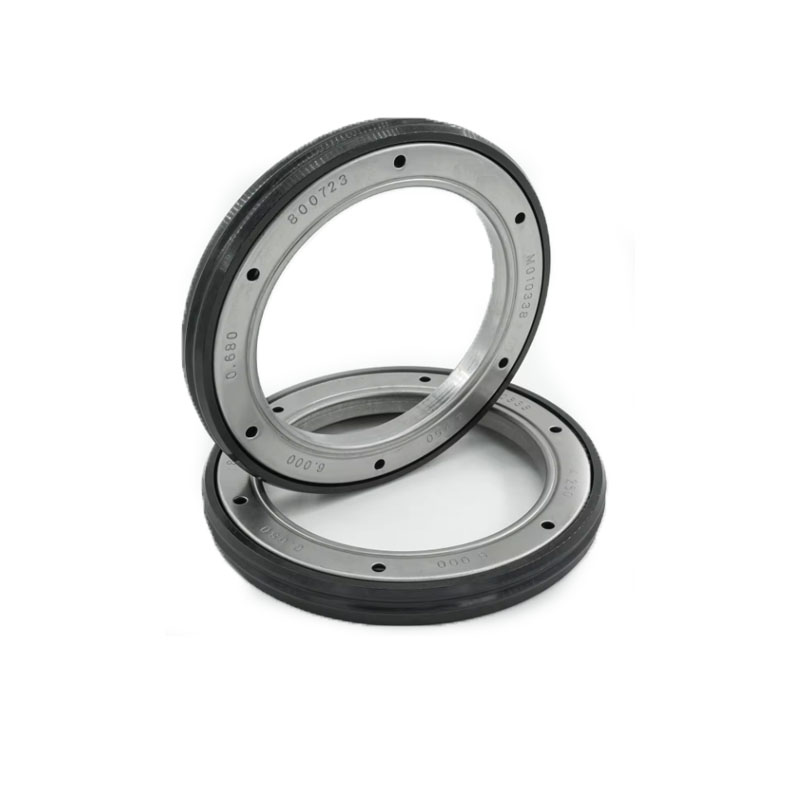
Axial shaft seals play a pivotal role in various industries, from automotive to aerospace, acting as a blockade against fluid escape while simultaneously preventing contamination from entering the mechanical system. Their design and application require meticulous attention to detail, drawing on extensive expertise to ensure optimal functionality.
In the automotive sector, for instance, the role of an axial shaft seal is indispensable. Given its exposure to a variety of conditions, from high-speed rotations to temperature fluctuations, the seal’s ability to withstand these variables is evidence of superior engineering. Materials such as elastomers and plastics are often preferred due to their durability and flexibility, which accommodate the extensive range of motion and stress levels experienced by rotating shafts.
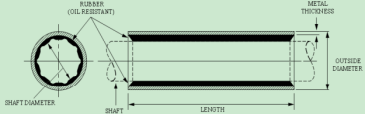
Choosing the right axial shaft seal requires expert knowledge of the operating environment. For instance, in an application where chemical exposure is prevalent, seals made from PTFE or similar materials are favored due to their chemical resistance. This underscores the importance of not only understanding material properties but also having the authoritative insight to match these properties with the specific demands of the application.
In circumstances involving high-pressure applications, such as in hydraulic systems, the integrity of an axial shaft seal is vital.
These seals must be crafted from materials capable of withstanding substantial pressure while maintaining a perfect seal. Here, metallurgical expertise plays a crucial role in defining the seal's durability and performance, often integrating reinforced materials that provide enhanced pressure resistance.
axial shaft seal
The critical nature of axial shaft seals also extends to the domain of aerospace engineering, where precision and reliability are non-negotiable. In such high-stakes environments, these seals undergo rigorous testing to ensure they meet stringent safety standards, further highlighting the blend of expertise and trustworthiness required in their development.
It's essential for industry specialists to consider lifecycle cost analysis when selecting axial shaft seals. A seal that demands frequent replacement or leads to unscheduled downtimes due to failure can exponentially increase operational costs. Therefore, investing in high-quality axial shaft seals, although possibly more expensive initially, can offer significant cost savings over time. Experience has shown that durable, well-designed seals reduce the risk of catastrophic failure, translating to minimized maintenance costs and prolonged machinery life.
Collaborating with manufacturers who have established a reputation for quality and innovation can strengthen trust in axial shaft seal performance. These manufacturers invest heavily in research and development, continually enhancing seal technology to meet evolving industrial requirements. Seeking partners with proven track records of delivering seals that exceed industry standards reinforces confidence in long-term operational stability.
Moreover, proper installation and maintenance are equally crucial. Even the most expertly designed seals can fail if not installed correctly or if subjected to irregular maintenance schedules. This necessity for precision in installation emphasizes the need for skilled technicians who understand the intricate dynamics of axial shaft seals in the broader mechanical system.
Ultimately, the role of axial shaft seals is indispensable in the effective operation of machinery across various industries. Their significance reaches beyond mere mechanical components; they embody the culmination of expertise, authority, and trust in engineering solutions. By selecting the appropriate seal and ensuring meticulous care in their installation and maintenance, businesses not only safeguard their operational integrity but also optimize performance, reliability, and cost-efficiency.