Axial O-Rings have become an essential component in various industrial and mechanical applications, ensuring fluid and gas sealing efficiency. Despite their small size, these components play a pivotal role in maintaining operational integrity and safety. With decades of proven reliability, experts have continually advanced their designs to enhance performance in complex environments, making them indispensable in industries ranging from automotive to aerospace.
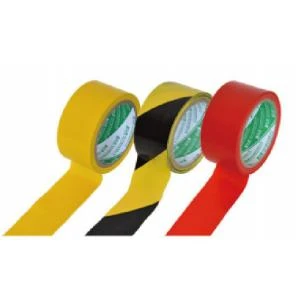
The efficacy of an axial O-ring lies in its unique design, which allows for seamless integration between surfaces to prevent the escape of fluids or gases under pressure. Unlike radial O-rings, which seal around a cylinder, axial O-rings are placed in a groove that runs perpendicular to the direction of pressure, providing a robust seal that withstands high-pressure environments.
The materials used in manufacturing axial O-rings are carefully selected to match specific application requirements. Common materials include nitrile rubber, silicone, fluorocarbon, and PTFE. Each material offers distinct properties such as temperature resistance, chemical compatibility, and flexibility. For instance, fluorocarbon O-rings are preferred in high-temperature settings due to their ability to withstand extreme heat without degradation, whereas silicone O-rings are renowned for their flexibility and capacity to maintain a tight seal in low-temperature environments.
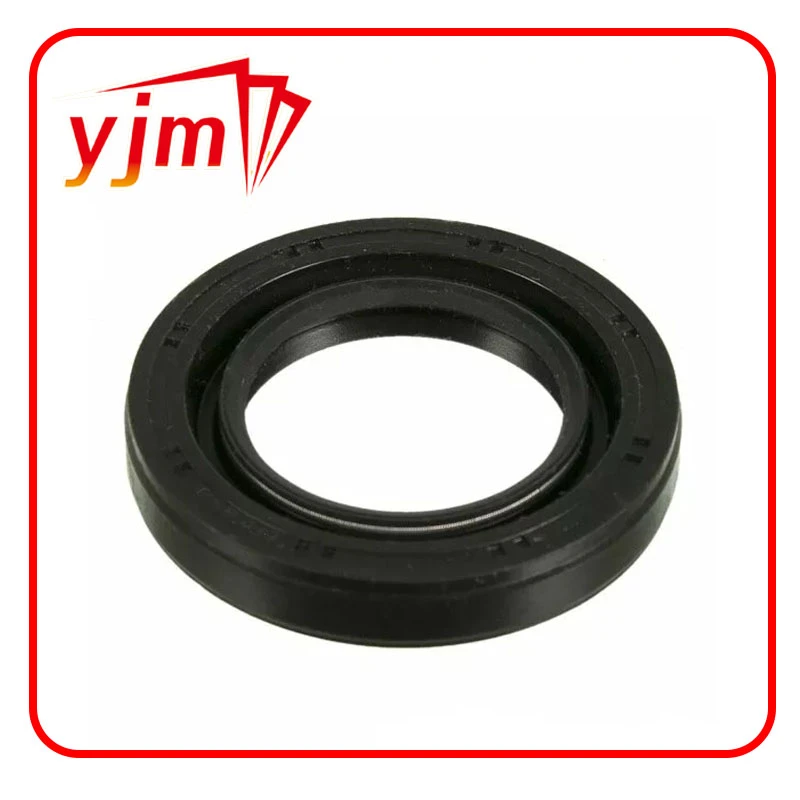
Expertise in choosing the right O-ring material significantly impacts the product's reliability and lifespan, and those tasked with this responsibility often possess deep industry knowledge and experience. Understanding the operational environment, including pressure levels, temperature fluctuations, and chemical exposures, is crucial. The wrong material choice can lead to premature failure, resulting in costly downtime or repairs.
A remarkable aspect of axial O-rings is their adaptability. They find usage not only in static applications—where the parts remain stationary—but also in dynamic settings that see regular movement or vibration. This versatility reinforces their importance in industries where conditions are constantly changing or highly variable.
axial o ring
Manufacturers emphasize not just on the choice of materials but also on precision engineering. Modern manufacturing techniques have significantly evolved, employing advanced technology like computer-aided design (CAD) and finite element analysis (FEA) to ensure that each O-ring meets strict industry standards. Such technological advances have enabled production of O-rings with enhanced tolerances and superior performance, even in the harshest conditions.
Professional consultation is invaluable when selecting the right axial O-ring for a particular application. Many manufacturers provide expert advice and technical support to guide clients through the selection process, ensuring all operational requisites are addressed. This professional relationship fosters trust and provides assurance that all specifications are meticulously evaluated and met.
Moreover, regular maintenance checks and replacements of axial O-rings are advisable to guarantee long-term effectiveness. Over time, even the best-designed and installed O-rings can exhibit wear or damage due to constant stress, chemical exposure, or extreme pressure cycles. Therefore, establishing a proactive maintenance routine can safeguard operations from unexpected failures.
The role of axial O-rings extends beyond their functional attributes and into the realm of sustainability. By preventing leaks and energy loss, these small components contribute significantly to the efficient use of resources and reduction of wastage in industrial systems. This positions them as not only an economic choice but also an environmentally responsible option in this age of heightened ecological awareness.
In conclusion, axial O-rings are a testament to the adage that good things come in small packages. Their simple yet effective design, coupled with advances in materials science and precision engineering, ensures they remain the backbone of sealing solutions in modern industry. The expertise required to select the appropriate O-ring and maintain its operation underscores their indispensable role in today’s technology-driven world. As industries continue to evolve, so too will the designs and applications of axial O-rings, maintaining them as a crucial element in ensuring the efficiency and safety of mechanical systems.