Navigating the world of industrial sealing solutions can be challenging, particularly when considering the critical role of oil seals in machinery applications. When it comes to the NBR oil seal, often referred to as a nitrile rubber oil seal, expertise in selection and implementation can significantly enhance operational efficiency and longevity of equipment.
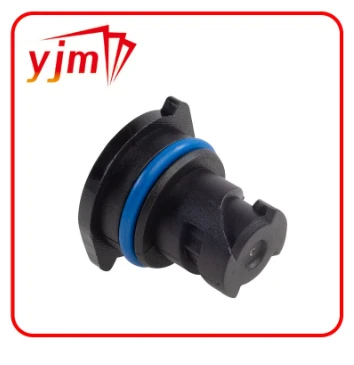
NBR (Nitrile Butadiene Rubber) oil seals are engineered for performance in environments where contact with oil and resistance to extreme temperatures are prevalent. Their design caters to industries ranging from automotive to manufacturing, thanks largely to their versatile chemical resistance. This adaptability makes NBR oil seals a cornerstone in ensuring operational integrity and fluid control.
The expertise surrounding NBR oil seals begins with a comprehensive understanding of their composition and capabilities. NBR, renowned for its resistance to petroleum-based oils and fuels, operates effectively in temperature ranges between -40°C and 120°C. This quality is essential for applications where fluctuations in operating conditions are frequent and demanding. Experts in the field emphasize selecting the correct seal size and compound to align with specific mechanical and environmental requirements.
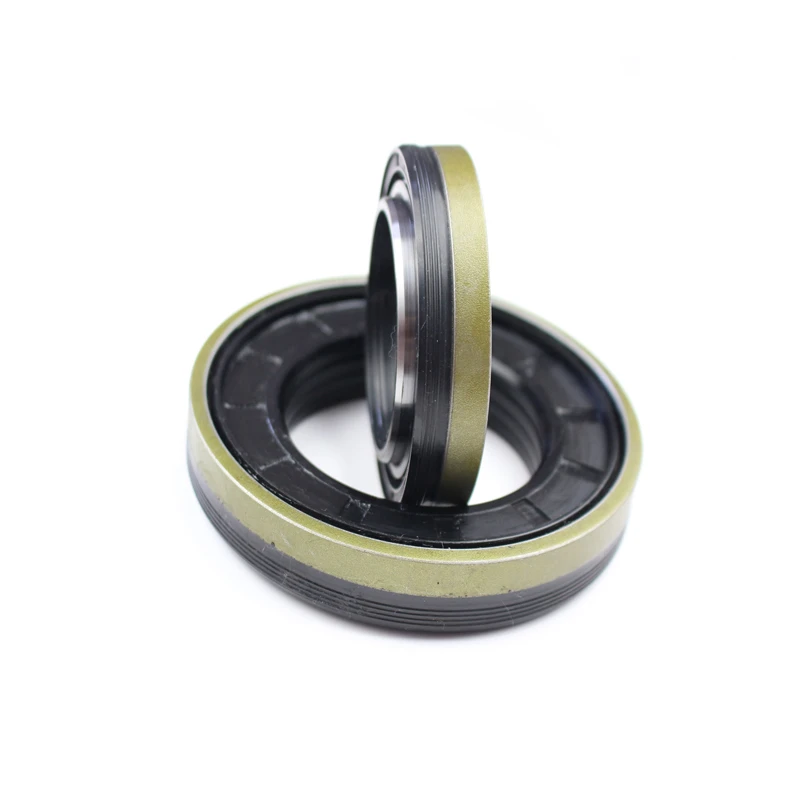
In addition to temperature resilience, NBR oil seals are celebrated for their wear resistance, which is crucial in high-friction environments. The integrity of these seals over an extended period can reduce maintenance frequency, thus offering substantial cost savings and minimizing downtime. Industry professionals often advocate for regular evaluation and timely replacement to preempt any performance degradation.
Authoritativeness in the application of NBR oil seals can be demonstrated through adherence to industry standards and guidelines. Collaborating with top-tier manufacturers that prioritize rigorous testing and quality assurance emphasizes reliability. Certifications such as ISO 9001 can be indicators of a manufacturer's commitment to quality, thereby enhancing trustworthiness in their products.
nbr oil seal
It is this trustworthiness that ultimately affects consumer confidence. NBR oil seals, when sourced from reputable suppliers, offer a credible solution to maintaining machinery efficiency. Working with certified professionals for installation further ensures that the seals are optimally positioned to prevent leakage and contamination, which can be catastrophic in precision industries.
Moreover, the incorporation of innovative technologies in the development of NBR oil seals sets authoritative brands apart. The use of advanced manufacturing techniques, such as CNC machining and 3D modeling, contributes to precise engineering and customization options — directly catering to unique industrial demands. These innovations not only extend the life expectancy of the seals but also enhance their functionality.
The application of NBR oil seals also extends beyond traditional boundaries in modern contexts. For instance, in the evolution of electric vehicles, where thermal management is crucial, NBR oil seals play an instrumental role in maintaining the performance of components like transmissions and E-axles, which are exposed to constant lubrication and cooling fluids.
Finally, real-world experiences validate the efficacy of NBR oil seals. Case studies highlight how industries, from automotive giants to aerospace sectors, rely on the bespoke design and durable nature of these seals to drive efficiency and reliability. Testimonials from industry veterans and engineers provide tangible evidence of their effectiveness, combining personal experience with empirical data to form a compelling narrative.
Investing in NBR oil seals is not just a decision, but a strategic move towards ensuring operational excellence. By leveraging professional expertise, authoritative sourcing, and technological advancements, businesses can optimize their machinery performance, thereby reinforcing their market position through prudent and informed sealing solutions.