When selecting the right shaft seal for any engineering project, specifically a 3 8 shaft seal, one must deeply understand the nuances that define their application, performance, and longevity. A 3 8 shaft seal isn’t just a mere component; it is an integral part of an entire mechanical system designed to prevent leakage, maintain pressure, and enhance the efficiency of machines. Selecting the proper shaft seal involves examining multiple facets, ranging from material composition to environmental adaptability.
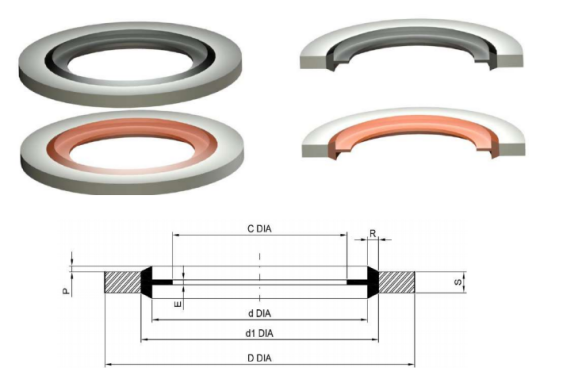
Experience plays a crucial role when dealing with shaft seals. Engineers and technicians must have practical hands-on understanding garnered from real-world applications. This experience spans from recognizing common operational failures related to seals, such as wear and tear issues, to identifying the subtle signs of impending seal failure. For instance, a seasoned engineer would know that excessive vibration could lead to gradual material degradation in seals. Consequently, this knowledge allows for preemptive measures to be taken, enhancing the seal's lifecycle and effectiveness in maintaining system integrity.
In terms of expertise, a deep dive into the material science behind 3 8 shaft seals reveals that seals can be composed of a variety of materials, including but not limited to, elastomers, polymers, and even metals in certain applications. Each material offers different properties. Elastomer seals, for instance, provide excellent flexibility and resilience, making them ideal for applications involving variable pressures. On the other hand, metal seals might be used in high-temperature scenarios where conventional materials would fail. Understanding the distinct properties each material offers ensures that the appropriate selection aligns with the operational requirements of the respective machinery.
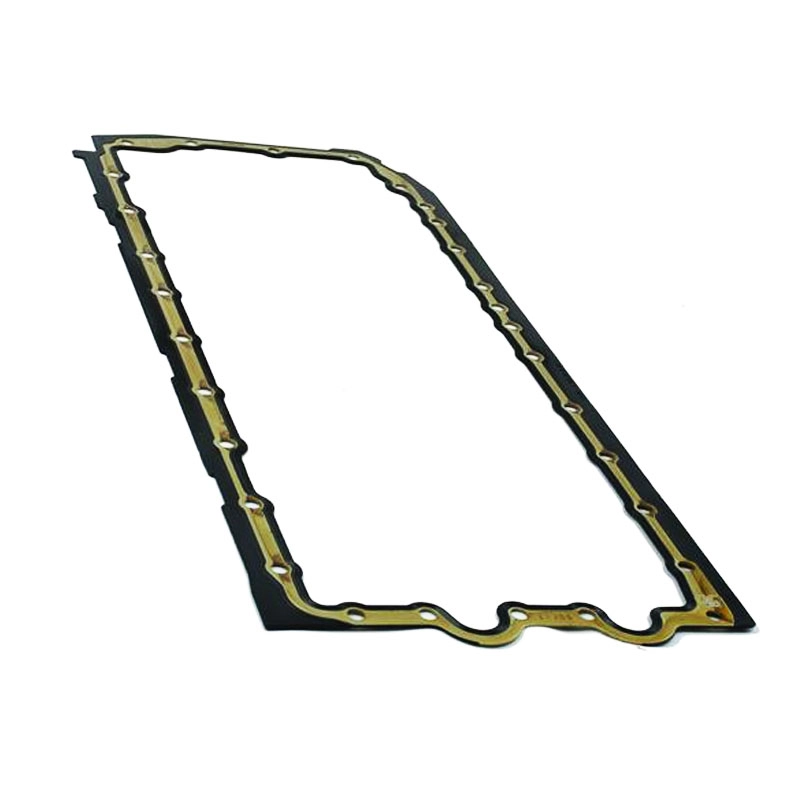
Drawing on authoritativeness, manufacturers of 3 8 shaft seals have continually invested in research and development to innovate seal technologies that are tailored to withstand the increasing demands of modern machinery. Authoritative sources, such as industry journals and certified testing agencies, provide detailed reports and white papers that highlight the performance benchmarks of various seals. It's within these documents one finds evidence-based data supporting the longevity, endurance, and efficiency of certain seal designs over others, making them essential reads for professionals seeking to make informed decisions on shaft seal supplies.
3 8 shaft seal
Trustworthiness is another vital attribute when dealing with components as critical as shaft seals. Ensuring that each 3 8 shaft seal complies with stringent industry standards, such as those outlined by organizations like the American National Standards Institute (ANSI) or the International Organization for Standardization (ISO), guarantees that the product meets or exceeds the expected performance criteria. Furthermore, testimonials and case studies from current users of these seals can provide practical insights into their reliability and performance in various conditions, be it under extreme heat, cold, or continuous operation.
It’s also essential to consider the auxiliary benefits that a correctly selected seal brings to a project. Beyond merely preventing leaks, a well-functioning shaft seal can contribute to reducing energy consumption by maintaining optimal pressure levels within an engine or pumping system. This efficiency ultimately leads to prolonged equipment life and reduced maintenance costs, providing both economic and operational benefits.
Moreover, modern trends have seen a shift towards environmentally sustainable manufacturing of shaft seals. Many manufacturers have adopted eco-friendly practices, producing seals that do not just meet the engineering requirements but also have a minimal environmental footprint. Selecting such products supports global efforts towards sustainability without compromising on quality or performance.
In summary, choosing a 3 8 shaft seal involves a careful consideration of several critical factors. Professionals must leverage their experience and expertise in material science and engineering principles to select the right seal. Meanwhile, reliance on authoritative and trustworthy sources furnishes the necessary data to back these decisions. As technology advances, the development of more efficient and sustainable seals enhances the capabilities of the machinery they serve, affirming the importance of making informed, precise choices in this field. By prioritizing these aspects, professionals ensure their machinery performs optimally, with reduced downtime and extended service life, achieving the ultimate goal of operational excellence.