Oil seals, vital components in mechanical systems, are instrumental in maintaining system efficiency and longevity. Among them, the 35 72 10 oil seal stands out for its unique specifications and applications, which are crucial in a myriad of industries.
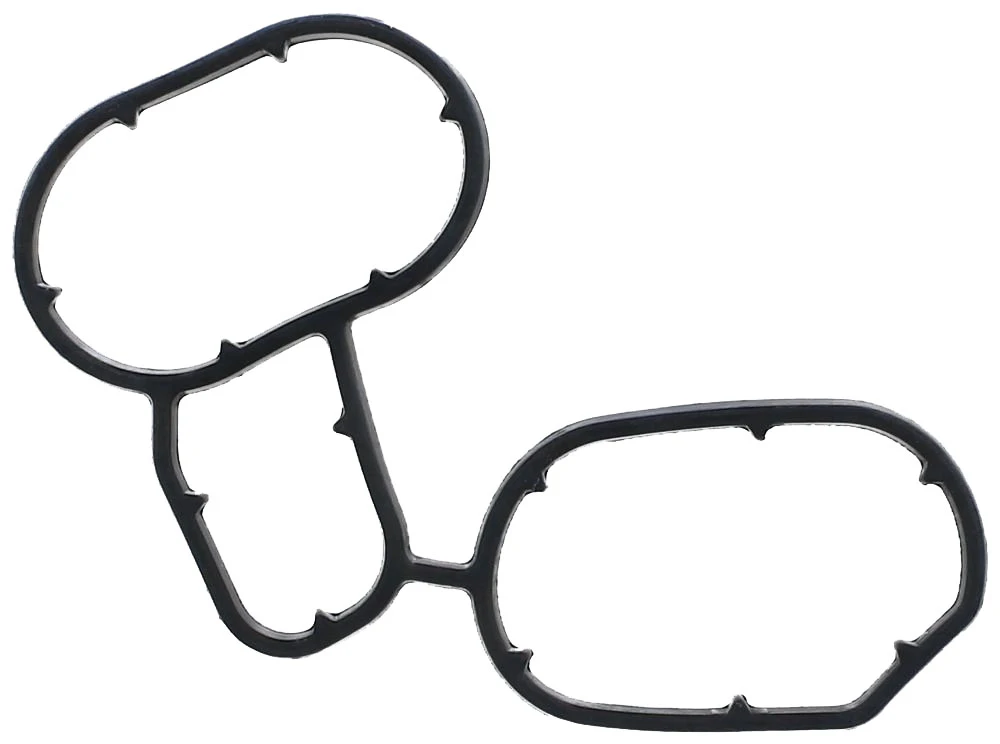
In mechanical design, oil seals are often the unsung heroes, vital yet frequently overlooked. Their role is to protect equipment from dust, dirt, and moisture while simultaneously retaining lubricants within the system. This ensures effective performance and mitigates wear and tear. The dimensions indicated by 35 72 10 refer to its size specifications an inside diameter of 35mm, an outside diameter of 72mm, and a width of 10mm. While these numbers might seem like trivial details, they are critical for ensuring compatibility and functionality in machinery.
Professionals in engineering and maintenance fields recognize the significance of precise measurements. An oil seal that fits perfectly prevents leakage, which can otherwise lead to catastrophic machinery failures. A 35 72 10 oil seal is a common choice in automotive, manufacturing, and industrial applications where this specific sizing is required. Its utilization ensures components remain lubricated, reducing friction and extending the lifecycle of the machinery.
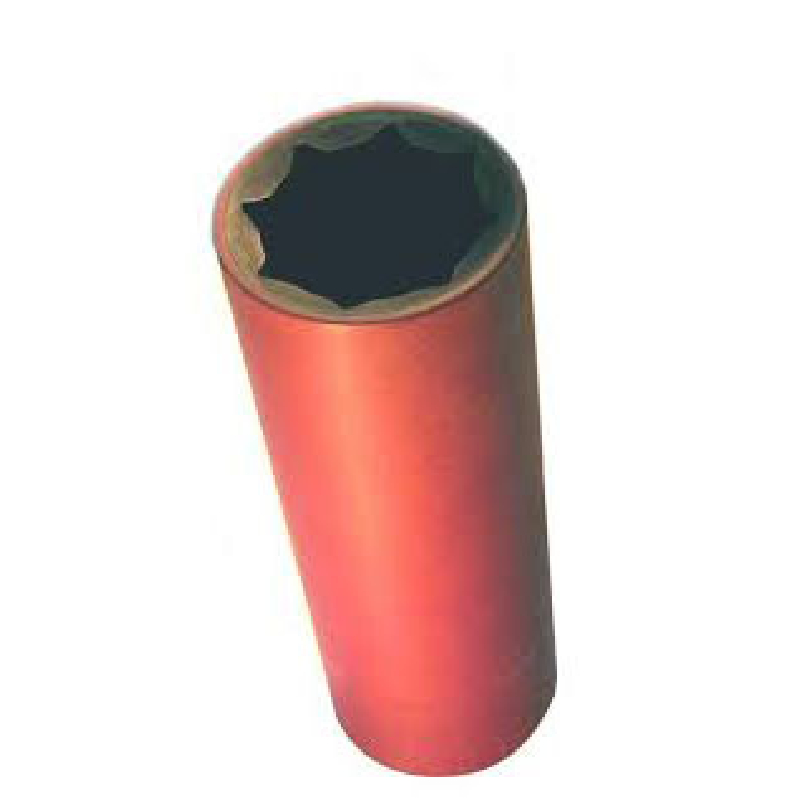
Beyond simple dimensions,
the quality of an oil seal is paramount. Material composition, for instance, is a defining factor. Nitrile rubber, Viton, and silicone are commonly used materials, each offering different properties. For instance, Viton provides exceptional chemical resistance and performance under high temperature, making it suitable for automotive and aerospace industries. Nitrile rubber excels in resistance to oils and fuels, while silicone remains flexible at lower temperatures, ideal for consumer product applications.
The 35 72 10 oil seal is not merely a product but a solution to an array of engineering challenges. Its design takes into account the forces exerted upon it, the substances it is meant to contain, and the environmental conditions it will face. Engineers rely on these seals to maintain the integrity of hydraulic systems, gearboxes, engines, and pumps, among other systems. In hydraulic systems, a compromised seal could lead to significant fluid loss, diminished force transmission, and ultimately system failure.
35 72 10 oil seal
Installation expertise also contributes to an oil seal’s effectiveness and longevity. Proper alignment and placement prevent premature wear. Engineers often undergo specialized training to install and replace these seals, understanding that even slight misalignments can jeopardize system integrity. In industries where equipment downtime can result in substantial financial losses, ensuring seals are correctly installed is imperative.
The authority on oil seals, particularly the 35 72 10 variety, often stems from manufacturers and suppliers who dedicate significant resources to research and development. These entities invest in advanced technologies and robust testing methodologies to produce seals that meet rigorous industry standards. Their authority grows as they continually refine and enhance the durability and performance capabilities of their products.
Moreover, trustworthiness in choosing the right supplier cannot be overstated. Reputable suppliers provide certification of adherence to industry standards, ensuring quality and reliability. Many offer guarantees and after-sales support, underscoring their commitment to customer satisfaction and product efficacy. By selecting trustworthy suppliers, companies mitigate risks associated with product failure, safeguarding operational continuity.
In conclusion, the 35 72 10 oil seal is a cornerstone of mechanical efficacy. Its precise dimensions cater to specific needs across various industries, ensuring optimal performance. Backed by expertise in materials science and engineering design, it remains an authoritative choice for professionals seeking to enhance equipment reliability. Trustworthy suppliers further solidify its standing through quality assurance and robust support, establishing it as a go-to component in maintaining industrial machinery.