The effective application of spring oil seals in industrial mechanics and automotive industries has been profound, fundamentally influencing fluid containment and machinery durability. Spring oil seals, pivotal in asset longevity, ensure the protection of machines against the ingress of contaminants while retaining essential lubricants in high-stress operations.
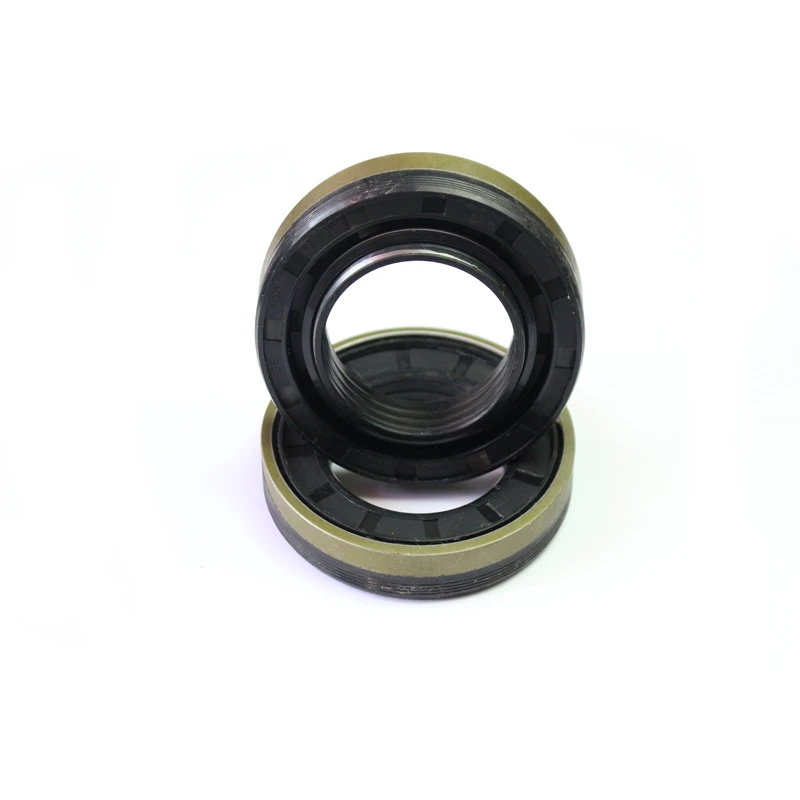
Spring oil seals, comprised of a metal casing and a synthetic rubber or elastomeric sealing element, maintain an essential equilibrium between resilience and flexibility. They work in conjunction with a garter spring, reinforcing the seal lip and constructing a barrier that sustains subjection to pressurized fluids, abrasive materials, and predictable vibrations. This resilience makes them indispensable in environments prone to aggressive contaminants.
Expertise in material selection is a primary determinant of application success for spring oil seals. High-grade materials like fluoroelastomers (FKM) offer superior chemical resistance and high-temperature endurance, vital for the rigorous conditions of heavy machinery or turbocharged automotive engines. Conversely, nitrile rubber suits lighter applications, offering a cost-effective alternative without compromising necessary durability. This knowledge is crucial for engineers optimizing for both performance and budgetary constraints in their designs.
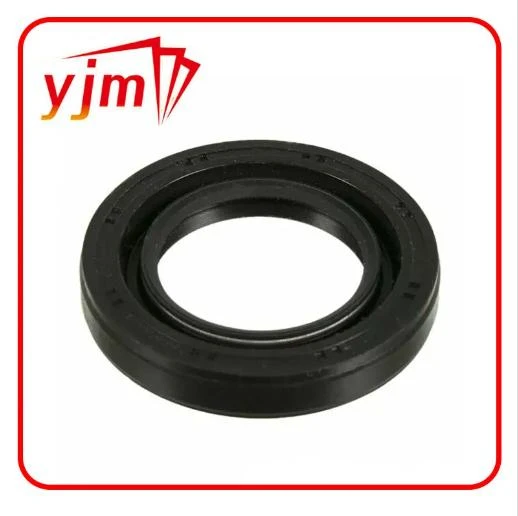
A scholarly understanding of load dynamics and kinematics is essential for selecting the appropriate spring oil seal. Seals are used in various rotational and linear applications, each demanding precise specification and installation. Engineers must consider shaft misalignments, surface finish, and concentricity to forestall premature seal failure. Field experience reveals that inadequately selected or installed seals lead to leakage, accelerated wear, and potential catastrophic failures.
spring oil seal
Increasingly, manufacturers across sectors align their practices with international standards like those from ISO and DIN, ensuring adherence to quality and consistency benchmarks in seal manufacturing.
These standards require a thorough comprehension of engineering tolerances and fortify trust in the seals’ reliability. Ongoing advancements in seal technology, such as the integration of unique lip geometries and low-friction materials, enhance performance, reduce energy consumption, and extend machinery lifespan.
Reliability in real-world applications accredits spring oil seals as a staple of engineering solutions. Mechanics have noted that repeated adjustments derived from hands-on experience—such as adjustments in seal lip configuration and spring tension—can have significant impacts on functional longevity. Technical support from manufacturers further complements such experiential knowledge, providing expert consultation that can pre-empt failures and maintenance surprises.
The intersection of theoretical knowledge and practical experience underscores the authoritative stance of spring oil seals as essential components in modern-day mechanics. They symbolize a fusion of traditional engineering principles with contemporary innovations that substantiate endurance and operational integrity. Trust in these components is a consequence of methodical testing, rigorous quality assurance procedures, and the continuous evolution of industrial seals to meet ever-evolving demands.
Corporations investing in dependable sealing solutions find a reduction in downtime and maintenance costs, substantiating their reliability. As industrial demands persist in complexity, the role of spring oil seals will continue to adapt, maintaining its quintessential position in the sphere of machine reliability and fluid dynamics, upheld by expertise and established authority in engineering practices.