Understanding Oil Seals by Dimension A Comprehensive Guide
In the world of mechanical engineering, oil seals play an indispensable role in preventing fluid leakage and maintaining system efficiency. These seemingly small components are critical to the overall performance and longevity of various machines, especially those that rely on lubrication systems. Understanding oil seals by dimension is essential for proper selection, installation, and maintenance.
An oil seal, also known as a lip seal or shaft seal, is a mechanical device designed to prevent the passage of oil or other fluids while allowing the rotation or linear movement of a shaft or housing. The primary function of an oil seal is to create a barrier between the lubricant and the environment, ensuring optimal machinery operation.
The dimensions of an oil seal are typically defined by three key parameters inner diameter (ID), outer diameter (OD), and width (W). These measurements are crucial for ensuring a proper fit and sealing effectiveness.
The ID refers to the inner circumference of the seal that fits around the shaft. It's essential to choose a seal with an ID that matches the shaft's diameter precisely to avoid any gaps that could compromise the seal's integrity. Oversized seals can cause damage, while undersized ones may not provide adequate sealing.
The OD, on the other hand, determines the seal's size relative to the housing it will be installed in. The OD should be slightly smaller than the housing bore to allow for a snug fit without causing deformation. A proper fit ensures the seal's lip can maintain contact with the shaft surface, creating a seal line A proper fit ensures the seal's lip can maintain contact with the shaft surface, creating a seal line
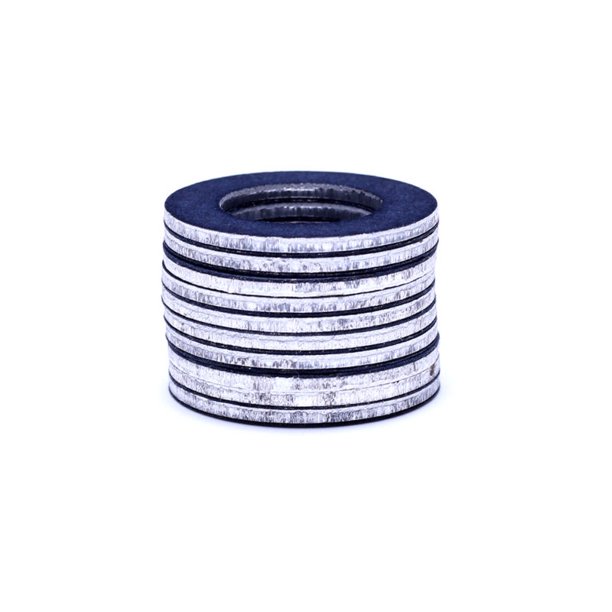
A proper fit ensures the seal's lip can maintain contact with the shaft surface, creating a seal line A proper fit ensures the seal's lip can maintain contact with the shaft surface, creating a seal line
oil seal by dimension.
Width, or the cross-sectional thickness of the seal, impacts its durability and sealing force. Thicker seals generally offer better resistance to pressure and wear but may require more force for installation. Conversely, thinner seals may be easier to install but may have a shorter lifespan.
When selecting an oil seal by dimension, it's crucial to consider factors like operating temperature, pressure, speed, and the type of fluid being sealed. Different materials, such as rubber (NBR), fluoroelastomer (FKM), or polyurethane (PU), have varying compatibility with different fluids and operating conditions.
Furthermore, dimensional tolerances are essential. While nominal dimensions provide a starting point, understanding the allowable variations is necessary for a successful seal. Tighter tolerances ensure a better fit but can increase manufacturing costs.
In conclusion, understanding oil seals by dimension is a critical aspect of ensuring efficient machinery operation. Accurate measurement and selection, based on the specific application and environmental conditions, are key to maximizing the seal's performance and longevity. Always consult manufacturer guidelines and, if possible, seek professional advice to ensure the right oil seal is chosen for the job at hand.