The Shocking Truth about Oil Seal Failures
In the world of mechanical engineering, few things are as critical to the smooth operation of machinery as the humble oil seal. Yet, when these components fail, the results can be nothing short of shocking. This is particularly true in scenarios where an oil seal breach leads to a catastrophic failure, not only compromising the integrity of the equipment but also posing significant safety risks.
Oil seals, often made from materials such as rubber or synthetic compounds, are designed to prevent lubricants from leaking out of joints and to keep contaminants from entering the system. They perform this role silently and effectively, often going unnoticed until something goes awry. When they do fail, it can be likened to a dam bursting; the consequences are both sudden and severe.
Imagine the pistons within a high-performance engine, each stroke delivering power with precision timing. An oil seal failure here could result in oil spilling into combustion chambers, leading to a loss of compression and potentially dangerous engine fires An oil seal failure here could result in oil spilling into combustion chambers, leading to a loss of compression and potentially dangerous engine fires
oil seal shock. In industrial machinery, a similar scenario could lead to the contamination of products or even the breakdown of production lines, causing economic losses that reverberate across entire supply chains
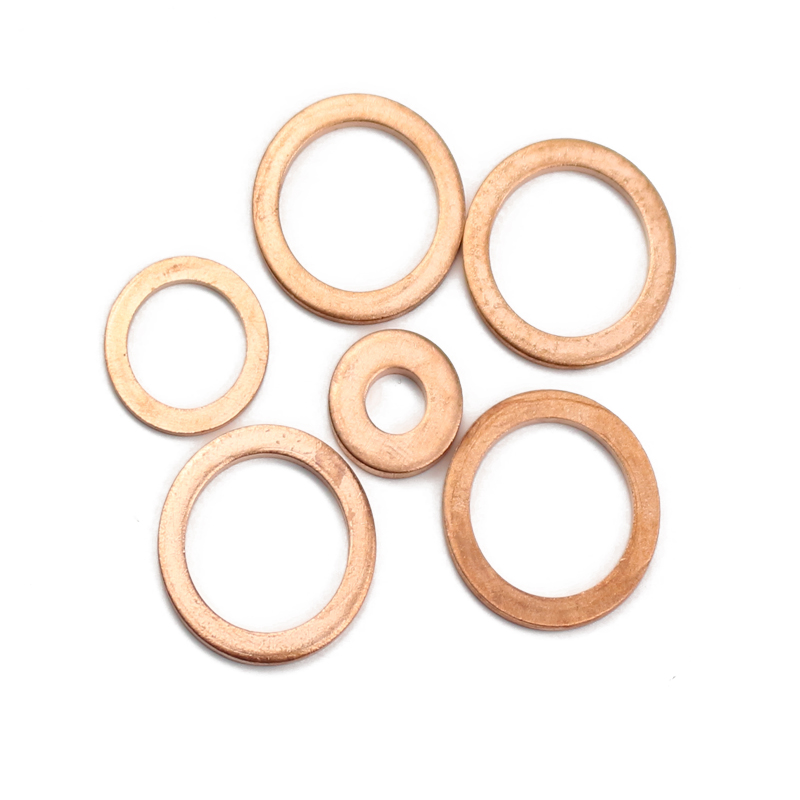
.
The shockwaves from an oil seal failure extend beyond immediate operational concerns. Environmental impacts become evident as oil leaks into ecosystems, harming wildlife and polluting natural resources. Moreover, the cost of cleanup and replacement parts, along with potential downtime, can quickly accumulate, making the prevention of oil seal failures a financially prudent measure.
Preventing such shocking incidents involves rigorous maintenance schedules, regular inspections, and prompt replacement of aging seals. It also requires a deep understanding of the operating environments where these seals are deployed, including temperature extremes, chemical exposure, and mechanical stresses.
In conclusion, while the term 'shock' may typically be associated with electrical systems, in the context of oil seals, it symbolizes the jolt of surprise and concern that comes with their unexpected failure. By recognizing the critical role these unassuming components play, we can work to mitigate the shocks and ensure the reliable operation of our machinery.