O-Ring Hydraulic Seals Essential Components in Fluid Power Systems
O-ring hydraulic seals, named after their distinctive O-shaped cross-section, play a crucial role in the efficient functioning of hydraulic systems. These seals, though seemingly small and insignificant, are the unsung heroes that ensure the integrity and performance of numerous industrial applications involving fluid power.
An o-ring is a doughnut-shaped elastomeric ring, typically made from materials like rubber, silicone, fluoroelastomer, or polyurethane. Their primary function is to prevent leakage and maintain pressure in hydraulic systems, which are integral to various industries, including construction, manufacturing, aerospace, and automotive.
The design of o-ring hydraulic seals is both simple and effective. The circular shape allows them to fit snugly into a groove, creating a barrier against fluid leakage when compressed between two mating parts. The elastomeric nature of the material enables them to deform under pressure, sealing the interface and preventing the escape of fluids. Moreover, they also protect against contamination, extending the lifespan of the hydraulic system.
One key aspect that makes o-rings versatile is their compatibility with a wide range of fluids, from oils and fuels to water and chemicals. They can withstand extreme temperatures, high pressures, and dynamic loads, making them suitable for diverse operating conditions. However, proper selection and installation are critical to ensure optimal performance. Factors such as system pressure, temperature, fluid compatibility, and dynamic or static application must be considered Factors such as system pressure, temperature, fluid compatibility, and dynamic or static application must be considered
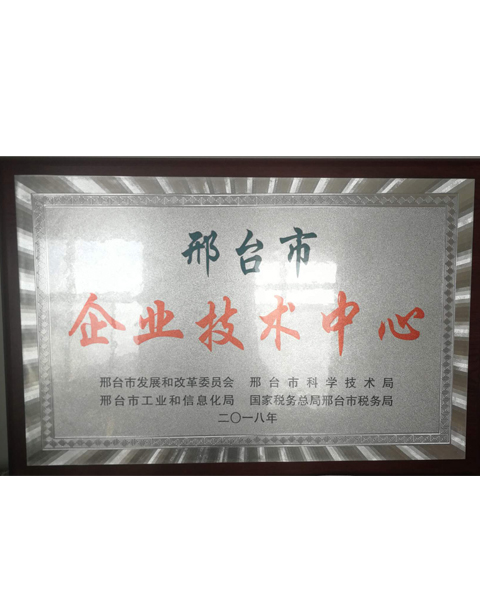
Factors such as system pressure, temperature, fluid compatibility, and dynamic or static application must be considered Factors such as system pressure, temperature, fluid compatibility, and dynamic or static application must be considered
o ring hydraulic seals.
Despite their durability, o-rings can degrade over time due to factors like chemical attack, ozone exposure, or mechanical wear. Regular inspection and timely replacement are necessary to prevent unexpected failures, which could lead to costly downtime and potential safety hazards.
Innovations in o-ring technology continue to push the boundaries of their capabilities. Advanced materials offer improved resistance to chemicals, higher temperature ranges, and better. Additionally, specialized designs like double o-rings, energized seals, and metal-inserted o-rings have been developed to cater to specific demanding applications.
In conclusion, o-ring hydraulic seals, while often overlooked, are indispensable components in hydraulic systems. Their effectiveness lies in their simplicity, versatility, and ability to withstand harsh environments. Understanding their function, selecting the right material, and maintaining them properly are vital for the reliable operation of any fluid power system. As technology advances, so does the potential for these humble seals to deliver even more robust and efficient sealing solutions.