Choosing the right oil seal is critical to ensuring the optimal performance and longevity of machinery across numerous industries. This intricate process goes beyond merely selecting seals based on price or availability. As many seasoned engineers and maintenance professionals will attest, a well-chosen seal can prevent costly downtimes and enhance the efficiency of equipment.
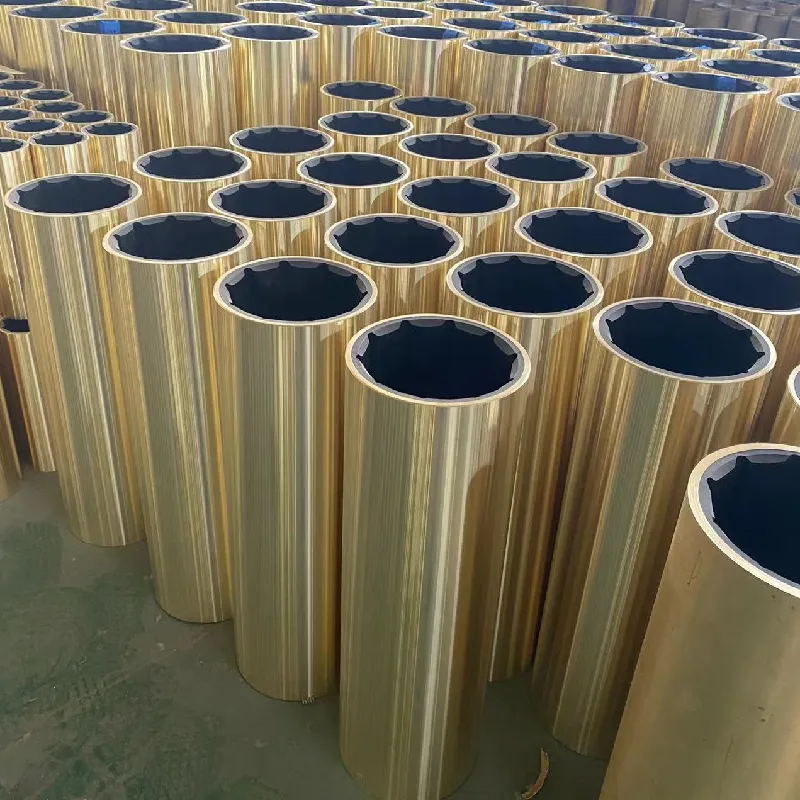
Oil seals, also known as rotary shaft seals, play a vital role in preventing lubricants from leaking out of machinery and stopping contaminants from seeping in. One fundamental consideration when selecting an oil seal is the material. There is a wide variety of materials available, including nitrile rubber, silicone, fluoroelastomer, and polytetrafluoroethylene (PTFE). Each material has innate properties suited for different environments. For example, fluoroelastomer comes highly recommended by experts for applications exposed to high temperatures and aggressive chemicals, owing to its excellent heat and chemical resistance.
Size and fit are also crucial factors in selecting the right oil seal. An ill-fitting seal can lead to leakage or premature wear, compromising the machinery it is meant to protect. Measuring the shaft, housing bore, and seal width accurately ensure a proper fit and, subsequently, system efficiency. Some experts advocate for using advanced tools, such as vernier calipers or micrometers, for precision, particularly in systems where minute discrepancies can lead to significant issues.
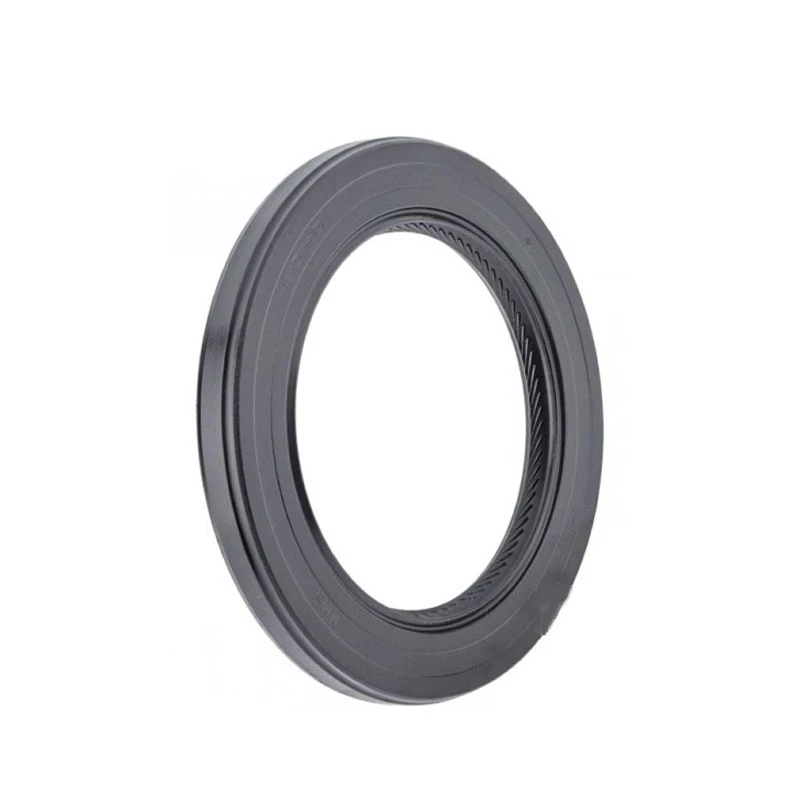
Compatibility with the lubricant or fluid being sealed is another aspect to consider. Different fluids react differently with seal materials, potentially leading to swelling, cracking, or degradation if mismatched. Engineering authorities frequently stress the importance of consulting compatibility charts or conducting laboratory tests under real-world conditions to ascertain that the material holds up well in its actual working environment.
oil seal selection
When selecting oil seals, consider the operational environment, including temperature extremes, pressure variations, and exposure to dirt or water. High-pressure applications, for instance, often require seals designed with reinforced construction to withstand the additional stress. Experienced professionals often recommend seals with metal or fabric reinforcement, or those incorporating double lip designs for added protection in such demanding environments.
Reputation and quality of the seal manufacturer also bear significant weight in selection decisions. Manufacturers with a track record of reliability and innovation tend to provide not only high-quality products but also essential support services such as technical documentation and tailored recommendations. Some industry leaders also offer software tools that allow engineers to input specific parameters and receive customized seal suggestions, directly tapping into the latest advances and knowledge in sealing technology.
Finally, collective wisdom emphasizes the necessity of regular inspection and maintenance of oil seals once they are in service. Detecting wear and tear early can prevent potential failures and extend the life span of both the seal and the accompanying machinery. Advanced diagnostics, such as infrared thermography and ultrasound, are recommended by experts for accurate monitoring, providing insights into potential issues before they escalate.
In conclusion, oil seal selection is an intricate process grounded in expertise and experience. By paying meticulous attention to factors such as material compatibility, proper sizing, environmental conditions, and manufacturer credibility, alongside implementing vigilant maintenance practices, businesses can achieve prolonged machinery life and efficiency. This expertise-driven approach manifests trustworthiness, assuring stakeholders of the enduring performance and reliability of their equipment.