Enhancing the efficiency and reliability of mechanical assemblies often hinges on the quality of seals preventing leaks and maintaining pressure. Among the myriad of sealing solutions, the O-ring face seal stands out for its versatility and effectiveness across various applications. This critical component, cherished by engineers and industrial designers, showcases a balance of simplicity and robustness, making it indispensable in both mundane and highly complex systems.
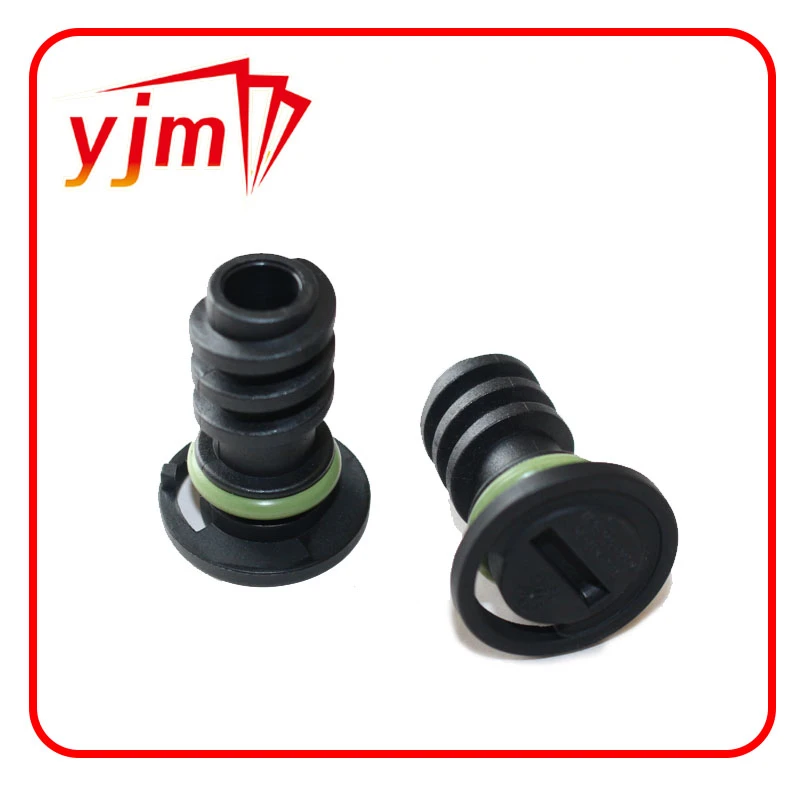
The O-ring face seal functions by creating a secure, leak-proof connection between mating surfaces in a mechanical assembly. Made primarily of elastomeric materials, these seals find usage in hydraulic systems, aerospace engineering, automotive assemblies, and even medical devices. Their widespread application is a testament to their unmatched reliability and adaptability in demanding environments.
From a specialist’s perspective, the selection and successful application of an O-ring face seal depend on several factors. First is the material composition, which determines the seal’s resistance to temperature fluctuations, chemical exposure, and pressure variations. Nitrile Rubber (NBR) is a common material offering excellent oil resistance, while Fluoroelastomer (FKM) provides superior temperature resilience, making it ideal for high-temperature applications.
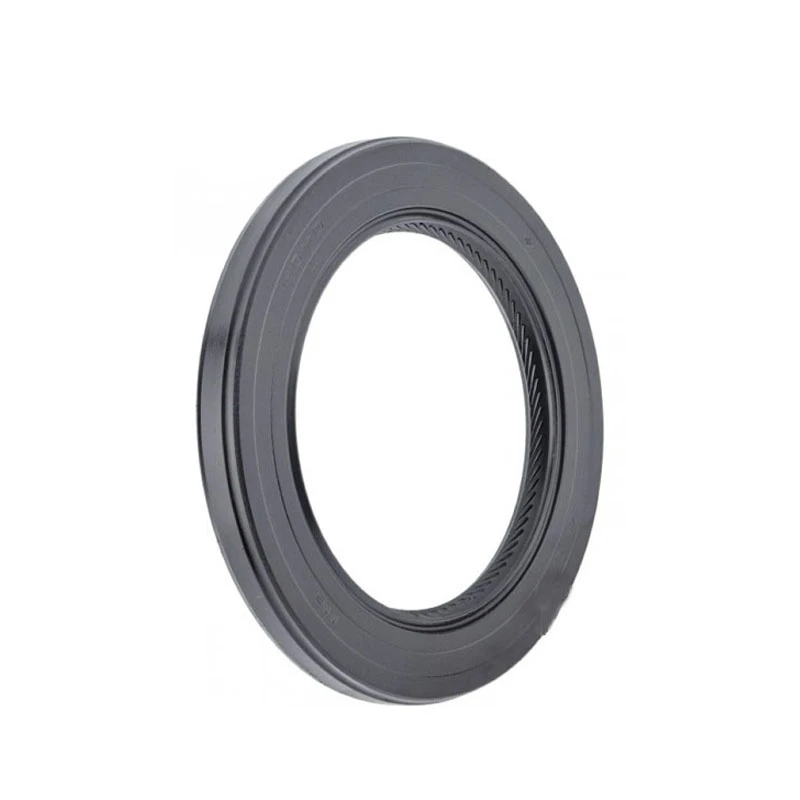
Expertise in this field acknowledges that appropriate sizing of the O-ring is crucial. The size must accommodate thermal expansion and contraction without compromising the seal's integrity. A misfit can lead to dire consequences, including system downtime and financial loss. Hence, precision in measuring the inner and outer diameters as well as the cross-section of the O-ring ensures optimal compatibility with the mating hardware.
Additionally, professionals emphasize the importance of understanding the application environment. An O-ring in a hydraulic pump, for instance, experiences different stressors compared to one used in a static seal for a flange joint. It's imperative to assess factors such as operational pressure, potential chemical interaction, and movement between surfaces to tailor the O-ring face seal for peak performance.
In terms of authority, the effectiveness of an O-ring face seal is supported by standardized testing methodologies like the ASTM D1414 – a benchmark in assessing O-ring materials’ tensile strength, elongation, and compression set. Such standards instill confidence, assuring consumers and OEMs of the seal's capability to meet rigorous operational criteria.
o ring face seal
Beyond technical specifications, trustworthiness in O-ring face seals is also forged through empirical evidence collected from field applications. Take, for example, the aerospace industry, which meticulously documents each seal's performance across thousands of flight hours. Such documented reliability bolsters the reputation of O-ring face seals, proving them time and again under extreme conditions.
Moreover, the trust placed in a manufacturer also weighs heavily in the decision-making process for procurement specialists and engineers. Reputable manufacturers who adhere to international quality controls, provide detailed documentation, and offer post-purchase support ensure that their O-ring face seals inspire confidence and readiness for various challenges.
However, even with a high degree of expertise and authority behind these seals, the application success significantly hinges on the end-user’s adherence to maintenance best practices. Regular inspections, accurate lubrication, and prompt replacement schedules ensure the longevity and reliability of O-ring face seals in service.
As industries continue to evolve with advancing technology and heightened performance demands, O-ring face seals adapt by incorporating innovative materials and precision engineering. This adaptability is not merely a trend but a necessity for maintaining operational excellence across industries globally.
In conclusion,
the significance of O-ring face seals extends beyond their physical presence in a mechanical assembly. They represent a confluence of material science, precision engineering, and practical expertise. By understanding their material characteristics, application contexts, and maintenance requirements, professionals across sectors can harness the full potential of these unassuming, yet critical components, ensuring sustained performance and operational success in diverse industrial landscapes.