Understanding the importance of oil seals by dimension is crucial for industries that rely on machinery and equipment running efficiently. Oil seals, also known as shaft seals or rotary seals, play an indispensable role in preventing fluid leakage and protecting against dirt, dust, and other contaminants. The proper selection of these seals by dimension is not just a matter of fitting; it ensures the longevity and optimal performance of the machinery.
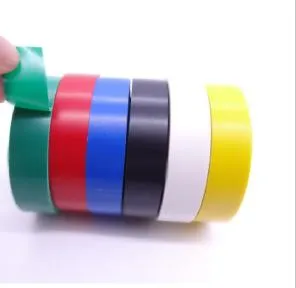
When selecting oil seals by dimension, experience dictates that accurate measurements are paramount. Precision in measuring the inner diameter, outer diameter, and width of the seal ensures compatibility with the machinery. Miscalculations can lead to operational inefficiencies, seal failure, and costly downtime. Expert insights suggest using calipers or other precise measuring tools for this task. Additionally, understanding the shaft's tolerance levels can prevent future complications.
Industries ranging from automotive to aerospace rely heavily on these seals, and expertise in materials science further refines the selection process. Depending on the operating conditions, oil seals may be made from materials such as nitrile rubber, silicone, or fluorocarbon.
Each material offers unique properties. For instance, nitrile rubber is resistant to petroleum oils and water, making it suitable for general applications. In contrast, fluorocarbon excels in high-temperature situations and exposure to aggressive chemicals. Therefore, expertise in the application environment aids in choosing the right material for maximum efficiency.
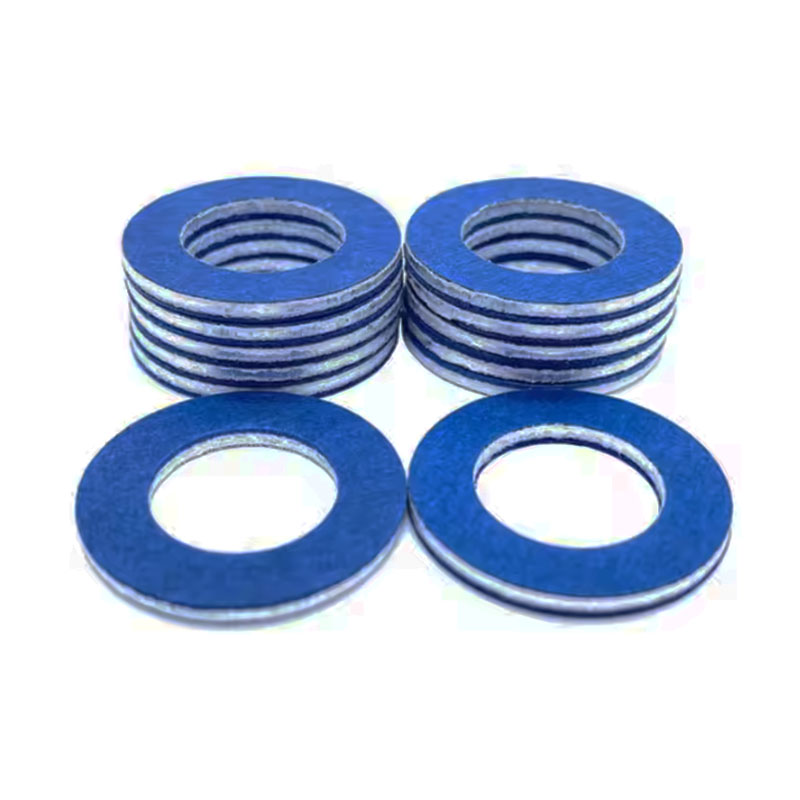
oil seals by dimension
Authoritativeness in the realm of oil seals is often established by adhering to international standards such as ISO or DIN, which provide guidelines on dimensions and material specifications. Manufacturers known for their compliance to these standards are typically more trustworthy as they provide a benchmark for quality and reliability. These standards ensure that the products meet specific performance criteria which can withstand rigorous industrial demands.
Trustworthiness is further reinforced by examining the manufacturer's track record and customer testimonials. Real-world case studies showcasing successful deployments of oil seals in varied applications can provide insights into their effectiveness. Additionally, partnering with suppliers who offer extensive warranties and post-sales support can add another layer of credibility. It is wise to select suppliers who have a transparent quality assurance process.
In conclusion, the meticulous selection of oil seals by dimension is a testament to both technical proficiency and practical wisdom. Products that are tailored to meet the specific demands of the machinery contribute significantly to operational stability and efficiency. Furthermore, the synergy between accurate measurements, material expertise, adherence to authoritative standards, and exercising due diligence in verifying supplier credibility cannot be overstated. This comprehensive approach ensures that the chosen oil seals not only fit perfectly but perform optimally under their specific operating conditions, setting the benchmark for industry best practices.