Heat resistant O-rings have become indispensable components in various industries, providing effective sealing solutions in high-temperature environments. For businesses seeking reliable and durable sealing solutions, understanding the nuances of these crucial components can offer a competitive edge. With that in mind, this comprehensive guide offers insights grounded in expertise, authoritativeness, and trustworthiness to navigate the complexities of heat resistant O-rings.
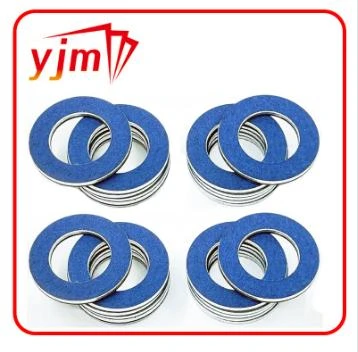
Products designed to withstand extreme temperatures often rely on the humble O-ring, whose simplicity belies its crucial function. Essentially, an O-ring is a loop of elastomer with a round cross-section, engineered to be seated in a groove and compressed during assembly between two or more parts. The resultant seal is designed to block the passage of liquids or gases, making it essential in maintaining system integrity in high-temperature applications.
In high-temperature contexts, the material of the O-ring is a critical factor. Silicone, fluorocarbon (Viton), and perfluoroelastomer (FFKM) are popular materials known for their superior heat resistance. Silicone O-rings, for example, can generally endure temperatures ranging from -60°C to 230°C, making them ideal for applications where both low and high temperature flexibility is required. On the other hand, Viton, with its high resistance to aggressive chemicals, performs exceptionally well between -20°C and 210°C, providing a robust solution where chemical and temperature resistance is paramount.
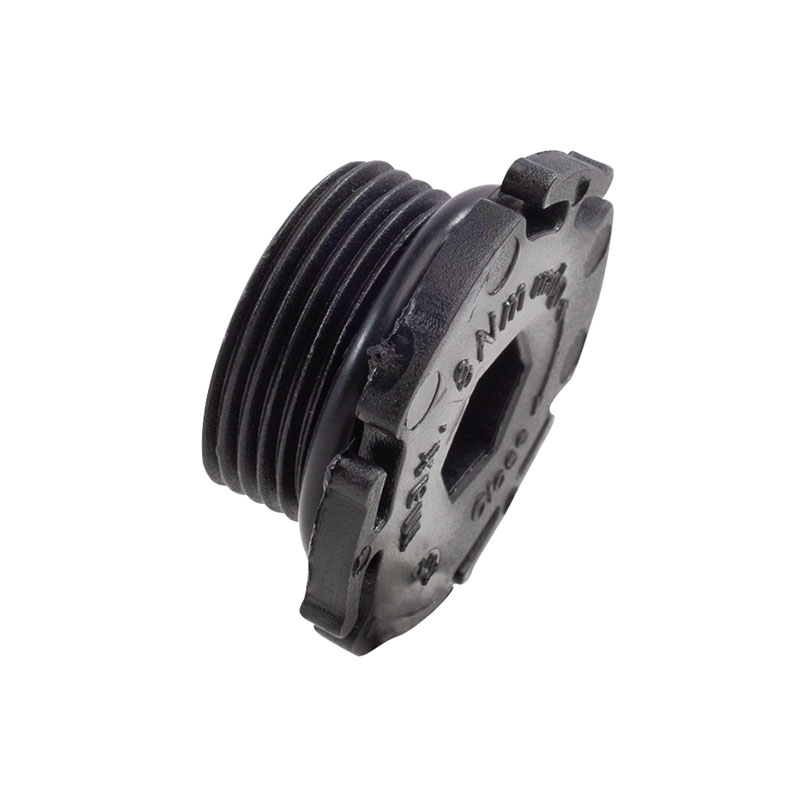
For environments with even more extreme temperatures, perfluoroelastomer O-rings are the go-to option, known for their performance in temperatures reaching as high as 327°C. These elastomers are renowned for their chemical inertness and can withstand reactive and high-temperature sealing applications better than most polymers. This makes them invaluable in industries such as aerospace, chemical processing, and oil and gas, where the cost of failure can be catastrophic.
Expertise in selecting the right O-ring also involves understanding the trade-offs inherent in design and material choice. While silicone provides excellent thermal stability and flexibility, it may not be the best choice for high-abrasion environments. Conversely, while FFKM offers unparalleled thermal and chemical resistance, it is often more costly compared to other elastomers. Employing a cost-benefit analysis, considering both material properties and operational demands, allows companies to make informed decisions in their component selection process.
heat resistant o rings
In practical application, beyond selection, proper installation and maintenance are equally important to ensure the longevity and function of heat resistant O-rings. Improper installation can lead to swift deterioration or failure, especially under thermal stress. Ensuring that installation tools and techniques are up to standard is fundamental. Routine inspections and maintenance play a pivotal role in foreseeing and preempting unnecessary operational shutdowns, enhancing trust in their continued performance.
The authoritativeness of expert suppliers cannot be overlooked. Choosing a manufacturer or supplier with a proven track record in heat resistant O-rings ensures reliable advice, quality, and often innovative solutions. Suppliers with extensive experience in specialized fields tend to have in-depth knowledge of specific industry challenges and opportunities, allowing for a more tailored approach to problem solving.
For industries ranging from automotive to aerospace, the trusted application of heat resistant O-rings comes from a combination of targeted education, reliable supply sources, and a clear understanding of application-specific challenges. This confidence is built on a foundation of proven expertise and experience, leading to enhanced performance and reliability under demanding circumstances.
In conclusion, when choosing O-rings for high-temperature applications, understanding the material science, application requirements, and supplier reliability is crucial. As technology evolves, new materials and composite technologies promise even greater heat resistance, efficiency, and durability. By staying informed and partnering with reputable suppliers, businesses can enhance system integrity, operational efficiency, and above all, safety, while navigating the complexities of high-temperature sealing solutions.