Metric bonded seals, often referred to as Dowty seals, play a crucial role in ensuring leak-proof sealing in various industrial applications. Their significance has grown exponentially with the advancement of technology and demanding industry standards. These seals are predominantly used in hydraulic and pneumatic systems, where they provide a reliable seal between threaded components.

A unique feature of metric bonded seals is their dual-material construction, combining a metallic ring with a bonded rubber component. This composition enhances the seal's mechanical strength while ensuring flexibility and adaptability to various flange and thread designs. The metal ring, commonly made of steel or stainless steel, provides structural support and resistance to pressure, while the rubber layer, often made of nitrile, fluorocarbon, or EPDM, ensures a reliable seal by accommodating surface irregularities.
The experience of many industrial professionals underscores the seals’ effectiveness in high-pressure environments. For example, in automotive engineering, metric bonded seals are preferred for their ability to prevent fluid contamination and maintain system integrity under rapid pressure fluctuations. Similarly, in the aerospace industry, these seals are valued for their lightweight properties and resistance to extreme temperatures and pressures, making them indispensable in the manufacture of efficient and reliable aircraft systems.
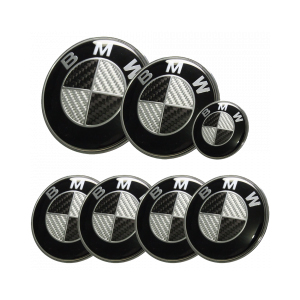
Expertise in selecting the right metric bonded seal involves understanding the application's specific requirements, such as operating temperature, pressure conditions, and fluid compatibility. For instance, an application dealing with hydraulic oils may necessitate a seal with a fluorocarbon rubber to ensure long-term reliability, whereas a system exposed to brake fluids might require an EPDM seal to avoid degradation.
metric bonded seals
Authoritativeness in the field of metric bonded seals is showcased by manufacturers who adhere to stringent quality control processes and international standards like ISO 3601. Companies that have established a strong reputation in the industry often offer seals that have been rigorously tested for burst pressure limits, temperature resilience, and chemical compatibility. This ensures that their products not only meet but exceed the expectations of high-stakes industrial applications.
Trustworthiness of metric bonded seals can be evaluated by considering customer testimonials and case studies that highlight successful implementations. For example, maintenance reports from heavy machinery industries often illustrate the reliability of these seals in preventing leaks and reducing downtime, translating into cost savings and increased operational efficiency. These real-world examples serve as a testament to the seal's capability and longevity under demanding conditions.
In conclusion, metric bonded seals stand out as indispensable components across various sectors, owing to their robust design, versatile application range, and proven reliability. Whether in automotive, aerospace, or heavy machinery, selecting the right bonded seal backed by authoritative testing and stringent quality assurance can significantly enhance system performance and longevity. Users and manufacturers alike benefit from understanding the seals' materials and design intricacies, enabling them to tailor solutions that meet specific industrial needs and establish trust in the seamless operation of their systems.