An oil crush washer, though seemingly a minor component, plays a crucial role in the maintenance and efficiency of vehicles. Its primary function is to create a secure seal between the bolt and the surrounding surface, typically in an engine, to prevent leakage of oil or fluids. Despite its small size, the expertise required in selecting and installing the right oil crush washer cannot be overstated.
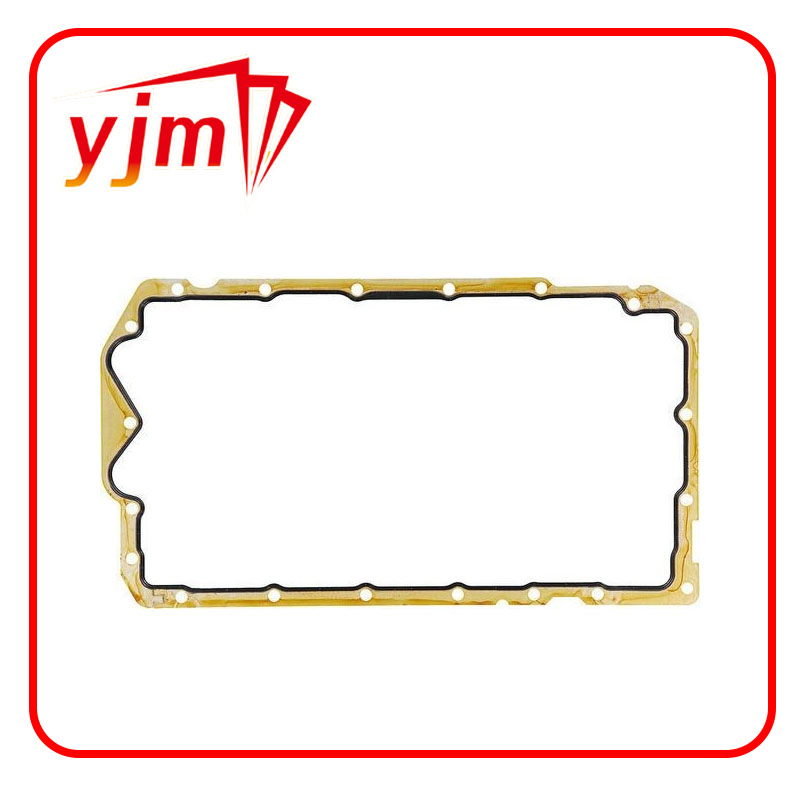
One of the standout features of oil crush washers is their ability to deform under pressure, thus ensuring a tight seal. This characteristic stems from the material typically used in their construction—softer metals like aluminum or copper. These metals are chosen for their ductility, allowing the washer to squash effectively under the bolt’s torque, conforming to the imperfections of the mating surfaces.
Choosing the correct oil crush washer fundamentally involves understanding the specifications of your vehicle or machinery. Given the variations in bolt sizes and pressure needs, a washer that fits one application may not necessarily be suitable for another. Always refer to the vehicle’s manual or consult an experienced technician to ensure compatibility. It’s vital to acknowledge that reusing a crush washer is generally not recommended due to its design for single-use purposes. Once compressed, its ability to seal effectively diminishes, leading to potential leaks and mechanical issues.
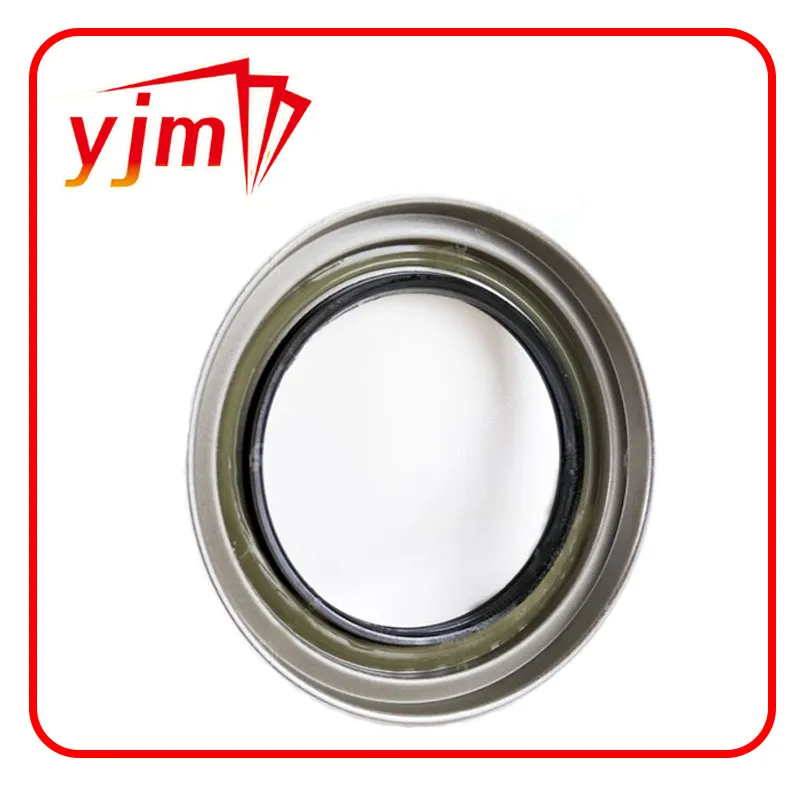
Installation of an oil crush washer demands a meticulous approach. Begin by cleaning the surfaces it will contact to remove any debris or oil residue. Placement should be precise, aligning with the bolt and ensuring no contamination occurs during the installation. When tightening the bolt,
applying the correct torque is paramount. Over-tightening can not only damage the washer but also strip threads on the bolt, leading to costly repairs.
The authority of an oil crush washer in automotive maintenance is undeniably significant. Experts within the field attest to the preventable issues that arise from neglecting this small component. Inadequate seals can lead to oil leaks, which not only decrease performance efficiency but can also cause environmental harm and pose safety risks, especially if oil leaks onto engine parts and causes a fire hazard.
oil crush washer
In terms of product expertise, understanding the material differences can enhance maintenance effectiveness. Aluminum crush washers, for example, are preferred in applications with higher thermal demands due to their superior heat dissipation properties. Copper washers, on the other hand, offer excellent corrosion resistance, making them ideal for environments exposed to moisture or chemicals.
Trusting in the right oil crush washer also relates to the reliability of suppliers and manufacturers. Ensure that the washers are sourced from reputable brands that adhere to quality standards and manufacturing precision. This attention to quality minimizes the risks of premature failures and inefficiencies, fostering greater confidence in vehicle operations.
The importance of oil crush washers is often highlighted by automotive specialists who view them not merely as accessories but as integral parts of the vehicle's operational integrity. Regular inspections should include checking for oil leaks at connection points, ensuring that washers are in optimal condition. Replacement should be a routine part of any oil change process, integrating seamlessly into the vehicle's maintenance schedule.
An authoritative tip from industry veterans is to stock an assortment of crush washers as part of a vehicle’s emergency toolkit. This ensures that in the event of a need, replacements are readily available whether during routine maintenance or unforeseen circumstances.
In sum, the underrated oil crush washer serves as a pivotal component in maintaining vehicle health and performance. Its straightforward design belies the sophisticated role it plays in sealing and protection. For any vehicle owner or mechanic, expertise in the use and replacement of oil crush washers is indispensable, contributing to longevity and reliability. By prioritizing quality materials and employing careful installation practices, this small element makes a profound impact on the overall operation of automotive and industrial systems.