In the bustling world of manufacturing and machinery, the efficiency and smooth operation of various equipment depend significantly on the small yet mighty components concealed within. Among these components, oil seals play a pivotal role in ensuring that machinery runs effectively without the risk of leakage or contamination. One specific model, the 25 35 7 oil seal, has gained significant traction as a reliable safeguard in multiple applications, offering an optimal balance of durability, efficiency, and utility.
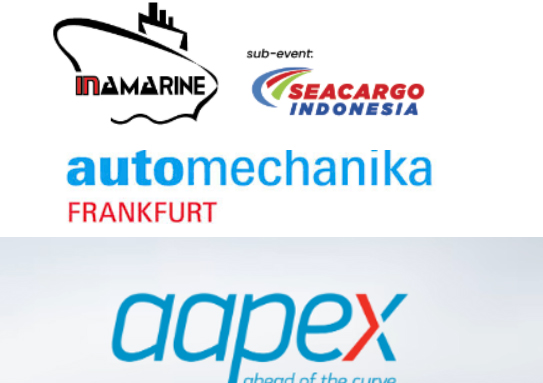
The 25 35 7 oil seal is not just a random collection of numbers; it signifies specific dimensions and characteristics that are crucial for machinery's functionality. The numbers represent the internal diameter (ID), outer diameter (OD), and thickness, respectively, all measured in millimeters. Each of these dimensions plays a critical role in defining the seal's performance and suitability for different applications.
When selecting an oil seal, real-world experience indicates that the precision of these dimensions is non-negotiable. The internal diameter needs to adhere closely to the shaft it encases, ensuring there are no gaps for fluid escape. Meanwhile, the outer diameter must perfectly fit the housing bore to prevent both fluid leakage and the ingress of contaminants. The thickness or width contributes to the seal's ability to maintain its structural integrity under varying levels of pressure and motion.
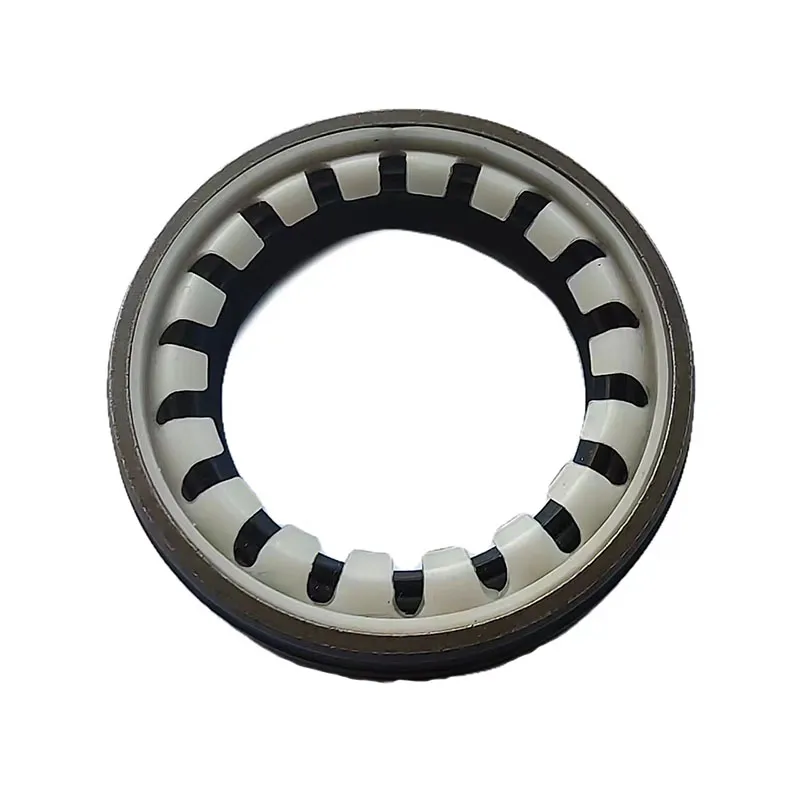
In heavily industrialized scenarios, where machinery experiences high rotational speeds, temperature fluctuations, or exposure to abrasive substances, the quality of oil seals can often define production efficiency. A compromised seal can lead to catastrophic machine failure, resulting in costly downtimes and repairs. However, industry professionals repeatedly affirm that the 25 35 7 oil seal strikes a harmonious chord between robustness and adaptability, making it a go-to solution for engineers and maintenance crews.
25 35 7 oil seal
The composition of the oil seal also plays a crucial role in its functionality. These seals are often made from materials like nitrile rubber, fluoroelastomers, or silicone, each chosen based on specific operational requirements. Nitrile, for example, offers strong resistance to oils and certain chemicals, making it an ideal choice in automotive and other similar applications. Conversely, fluoroelastomers provide excellent thermal and chemical resistance, catering to industries where extreme conditions are the norm.
A common concern among machinery operators revolves around the oil seal's longevity and reliability under intense usage. Expertise shared by engineers often points to the need for meticulously following manufacturer guidelines during installation. Proper installation tools, such as seal drivers or presses, ensure an even fit without causing damage to the seal lip—a vital part of the seal that prevents leaks. Moreover, regular maintenance checks and replacing seals as part of scheduled servicing can significantly extend machinery life, maintaining optimal injection, compression, and sealing capabilities.
Trustworthiness in this context stems from choosing oil seals that are manufactured by reputable companies adhering to global quality standards. As validated by numerous businesses, sourcing seals from manufacturers holding ISO certifications or those that adhere to rigorous quality control processes mitigates risks associated with lower grade parts. These trusted seals have consistently proven their mettle in high-stakes applications, from heavy-duty vehicles to various intricate machinery types.
In summation, the specificity and precision embodied by the 25 35 7 oil seal underline its indispensable nature in contemporary machinery applications. Its proven track record in terms of durability, adaptability to different environmental conditions, and compatibility with various types of machinery highlight its credibility. For businesses prioritizing efficiency and reliability, opting for high-quality oil seals can translate into prolonged machinery lifespans, reduced maintenance costs, and uninterrupted operations—pivotal factors reinforcing an enterprise's competitive edge in industrial domains.