The rondelle bonded seal, often simply referred to as a bonded seal, holds paramount importance in numerous industrial applications, especially in contexts where fluid integrity is crucial. The evolution and modern-day utilization of this small yet impactful component have made waves across hydraulic and pneumatic systems. The following exposition provides a nuanced perspective on the application, expertise, authority, and trustworthiness surrounding the rondelle bonded seal, framed for the discerning and technically-inclined audience.
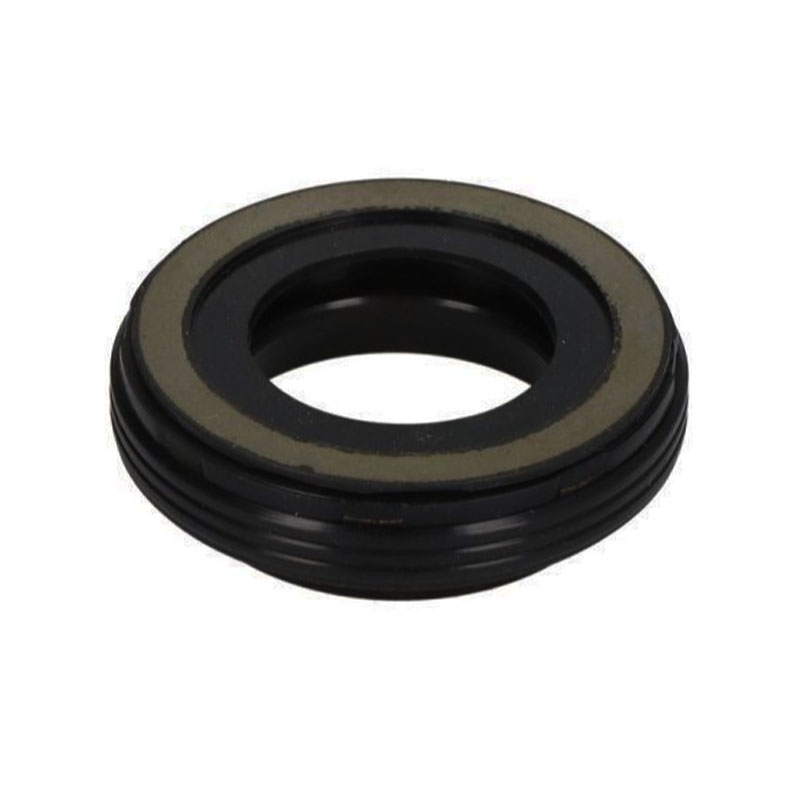
At the heart of industrial efficiency is the prevention of fluid leaks, which is where the rondelle bonded seal proves indispensable. This component exemplifies mechanical ingenuity by integrating a metal washer with a vulcanized rubber lip. The metal washer provides structural support and distribution of compression forces, while the rubber represents an adaptive barrier against fluid leakage. This symbiotic design is crucial in maintaining system integrity under varying pressure conditions.
Experience with bonded seals in high-temperature and high-pressure applications showcases their reliability. For instance, their deployment in hydraulic systems within the aerospace industry involves extreme operational contexts. An engineer noted their success in such environments, emphasizing the seal's endurance over extensive test flights and temperature variations. This is not an isolated incident; numerous industrial settings testify to the seal’s resilience and adaptability, further enhancing its credibility across multiple sectors.
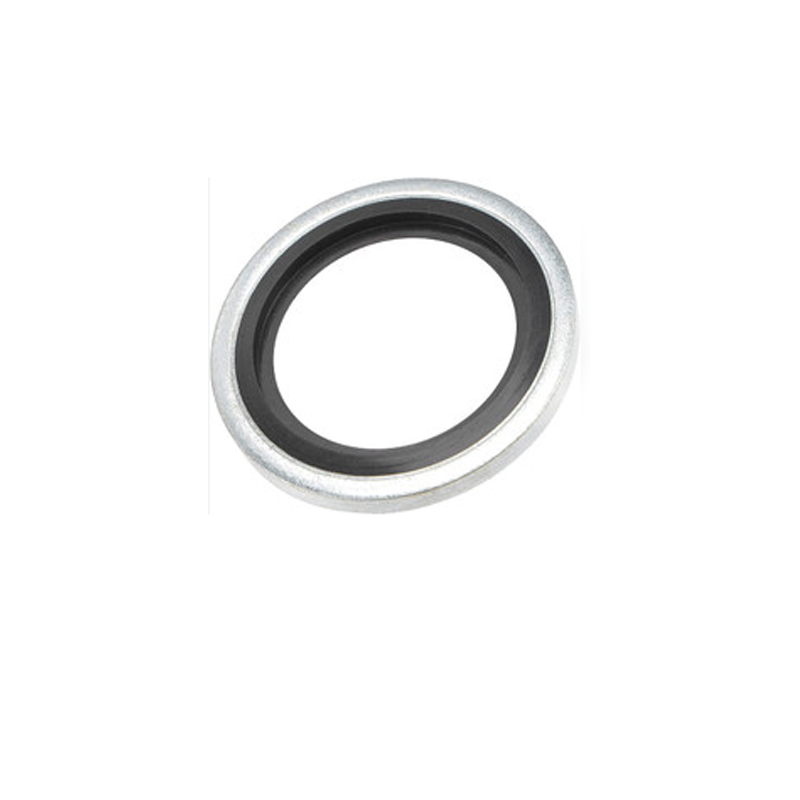
From an expertise standpoint, understanding the dynamics of material science and engineering involved in bonded seal production is essential. The choice of metals and elastomer types impacts the seal’s performance. Stainless steel, often used for its corrosion resistance and strength, accompanies elastomers like nitrile or Viton® for their differential thermal and chemical stability. Such expertise in material selection underscores the authority of manufacturers who ingeniously adjust compositions to meet specific industry requirements.
In sectors like automotive, oil and gas, and hydraulic equipment, where the cost of failure is exceedingly high, the authority of a well-designed bonded seal cannot be overstated. Systematic evaluations, including fatigue tests and failure mode analysis, ascertain the seal’s longevity and effectiveness. These critical assessments conducted by authoritative lab entities provide a benchmark for quality, enabling industries to adopt the best practices in their operations confidently.
rondelle bonded seal
Trustworthiness with rondelle bonded seals can be observed in their standardization and certifications. Compliance with international standards such as ISO 9001, and rigorous quality assurance protocols, establish the seal as a trustable component. Testimonials from leading industrial corporations often highlight the seal’s role in reducing maintenance downtime and operational hazards, further cementing trust.
The supply chain of bonded seals also operates on trust principles. Reputable manufacturers ensure consistent product quality and availability, vital factors for clients whose operations depend heavily on timely and reliable component supply. By leveraging advanced manufacturing techniques and quality controls, these suppliers mitigate risks associated with inferior product batches, delivering dependable seals that meet client expectations.
Rondelle bonded seals are integral to advancing the efficiency and safety profiles of modern machinery. Continuous innovations in seal design and material composition promise even more robust solutions for future cutting-edge technologies. The emerging applications in renewable energy systems, such as wind turbines and solar fields, offer new testing grounds for the seals, thus expanding their utility and proving their adaptability in innovative ways.
In conclusion, the rondelle bonded seal signifies a remarkable confluence of experience, expertise, authority, and trust. Its role transcends simple leak prevention, evolving into a critical enabler of industrial reliability and efficiency across diverse sectors. As technologies advance, so does the potential for these seals to contribute to safer, more sustainable industrial practices worldwide.