In the world of mechanical engineering, the motor shaft seal is a crucial component that ensures the efficiency and longevity of machinery. These seals play an essential role in preventing lubricant leakage and contaminants from entering the system, which could otherwise lead to equipment failure. Understanding the intricacies of motor shaft seals can bring substantial benefits to those involved in maintenance and design, ensuring high performance and reducing unnecessary costs.
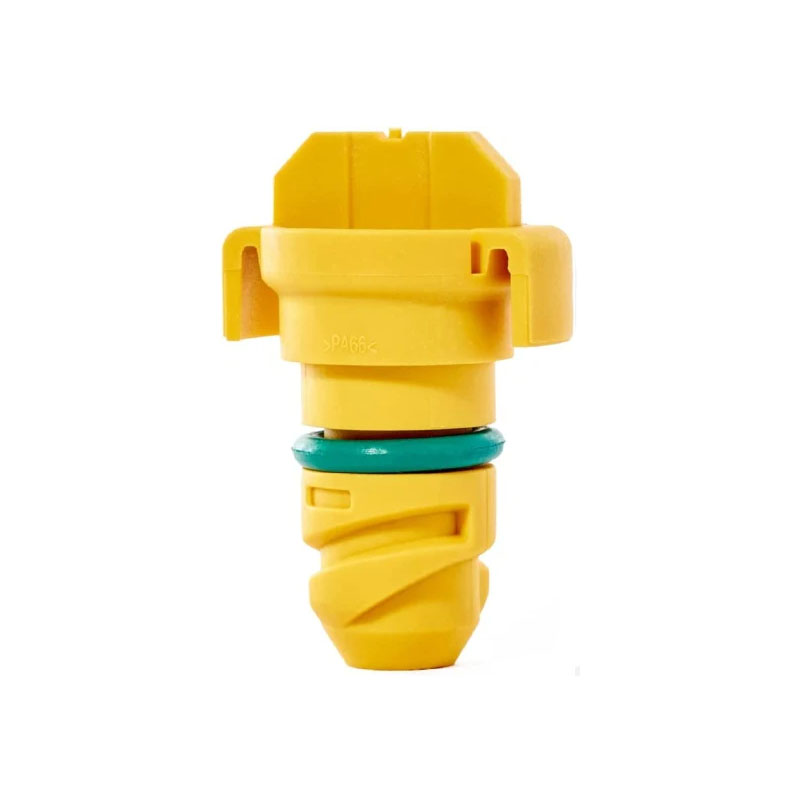
Motor shaft seals are designed to fit around a rotating shaft and provide a barrier between the internal and external environments of the motor. The primary materials used in these seals are nitrile rubber, silicone, and fluorocarbon, which are chosen based on their resistance to heat, pressure, and chemical exposure. The selection of the appropriate material is imperative for the seal's performance, as each application may have unique environmental conditions that impact the seal's longevity.
The importance of motor shaft seals cannot be overstated. According to expert sources, improper sealing can lead to bearing failures, increased friction, and unwanted downtime, which translates into financial losses. Experience has shown that industries that invest in high-quality motor shaft seals see a marked improvement in machine reliability and a decrease in maintenance costs. For example, in the automotive sector, where engines are subjected to high temperatures and pressures, a superior shaft seal can enhance vehicle performance and safety.
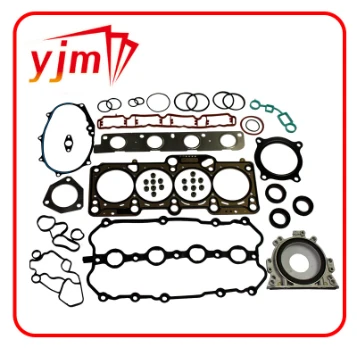
There are several types of motor shaft seals, including lip seals, T-seals, and labyrinth seals, each designed for specific functions. Lip seals are perhaps the most common, providing an economical and effective solution for most standard applications. They operate by maintaining a thin layer of lubricant on the shaft, which helps reduce wear and tear. More sophisticated seals, such as labyrinth seals, use a series of interlocking grooves to create a complex path that prevents fluid leakage. These are often employed in high-performance environments, such as aerospace engineering, where zero tolerance for leakage is critical.
motor shaft seal
The authority on motor shaft seals suggests regular inspection and preventive maintenance to ensure seals are functioning as expected. Replacing worn or damaged seals promptly can prevent extensive damage to the machinery. Innovative monitoring systems are now available that can predict seal degradation, providing timely alerts to maintenance teams.
From an industry perspective, the advancements in seal technology are noteworthy. New developments are continuously emerging, including self-healing materials that can extend the life of seals. Research and development in this field are driven by the demand for higher efficiency and lower environmental impact. Trustworthiness in suppliers and manufacturers is crucial, as not all seals are created equal. Leading companies provide detailed specifications, testing results, and certifications to verify their product's performance, giving assurance to engineers and procurement teams alike.
For those involved in product design, the role of motor shaft seals should be a primary consideration from the very beginning. Understanding the dynamics of the system and the operational environment will guide the selection of the appropriate seal. Consulting with knowledgeable seal manufacturers can provide insights into innovative solutions that might not be immediately apparent but can significantly impact the effectiveness and reliability of the final product.
In conclusion, motor shaft seals are a pivotal component in machinery that can influence performance, reliability, and cost-efficiency. Industry professionals must exercise expertise and thoroughness in selecting and maintaining these seals to leverage their full benefits. The continuous evolution in seal technology promises exciting prospects for enhanced machine longevity and sustainability. The authoritative knowledge and experience combined will ensure machinery operates seamlessly and economically over its intended lifecycle, underscoring the critical role motor shaft seals play in modern industrial applications.