Navigating the world of piston seals can often seem intimidating due to the technical aspects and myriad options available. However, the bonded piston seal stands out as a revolutionary component that facilitates enhanced efficiency and reliability in various mechanical systems. This article offers insights drawn from expert knowledge and real-world applications while emphasizing the importance of authority and trust in selecting the right piston seal.
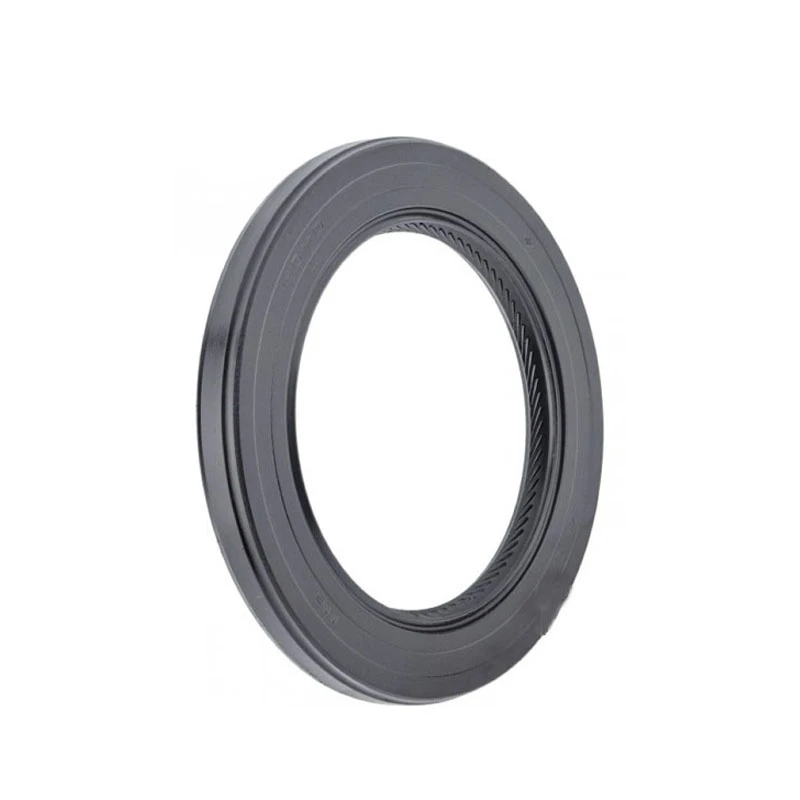
When it comes to heavy-duty machinery and dynamic hydraulic systems, the bonded piston seal has become a component of choice due to its superior sealing capabilities and durability. Unlike traditional piston seals, which are often susceptible to wear and tear under high pressure, bonded seals are designed to withstand extreme conditions. This advantage arises from their unique construction, where a rubber sealing element is chemically bonded to a metal carrier. This configuration ensures that the seal remains intact and effective, even under significant mechanical stress and thermal fluctuations.
The experience of utilizing bonded piston seals in industrial applications is telling of their reliability. For instance, in the automotive industry, these seals are critical for ensuring that hydraulic cylinders and shock absorbers function properly. The bonded seal's capability to maintain integrity over time results in fewer maintenance requirements and longer service life for vehicle components. This durability extends to a variety of sectors, including construction, aerospace, and manufacturing, making them indispensable in systems where precision and longevity are paramount.
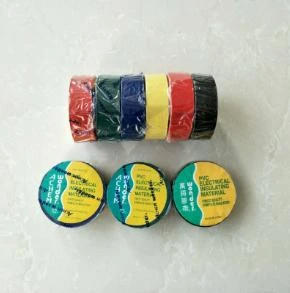
Professional expertise in manufacturing bonded piston seals reveals their meticulous production process. Leading manufacturers invest heavily in research and development to incorporate state-of-the-art materials and bonding technologies. The selection of material, typically a high-grade elastomer such as NBR (nitrile butadiene rubber) or FKM (fluoroelastomer), is crucial. These materials are chosen for their excellent resistance to oils, chemicals, and extreme temperatures, which enhances the overall reliability of the seals.
bonded piston seal
Moreover, authoritative testing methodologies in the industry further assert the superiority of bonded piston seals. Rigorous testing, including pressure, temperature cycling, and longevity tests, simulate real-world operating conditions. This rigorous testing provides data that reinforces the bonded seal's reputation for exceptional performance.
Consequently, engineers and purchasing managers can trust these seals to meet and exceed their specific requirements.
Trustworthiness of bonded piston seals also comes from the transparent supply chain and adherence to international quality standards. Suppliers who certify their products with ISO standards, for example, demonstrate a commitment to quality and consistency. Customers, thus, gain confidence in their purchase, knowing the product's specifications have been verified and validated.
In conclusion, the bonded piston seal represents a pinnacle of engineering innovation, providing unmatched performance in demanding applications. Whether it's sustaining the pressures within hydraulic systems or surviving the harsh conditions of an industrial environment, these seals set a benchmark for performance and reliability. By understanding the experience, expertise, authority, and trust that underpin the use of bonded piston seals, stakeholders can make informed decisions that enhance their operational efficiency and longevity. The adoption of such seals is not just a choice; it's an investment in the future stability and success of their machinery.