Single lip seals, an often-overlooked component in various mechanical and industrial applications, are pivotal to ensuring the longevity and efficiency of machinery. These seals, though seemingly simple, play a complex role by providing a barrier between moving parts and external environments. This article will delve into the nuanced functions of single lip seals, providing insights from my extensive experience in mechanical engineering and SEO optimization.
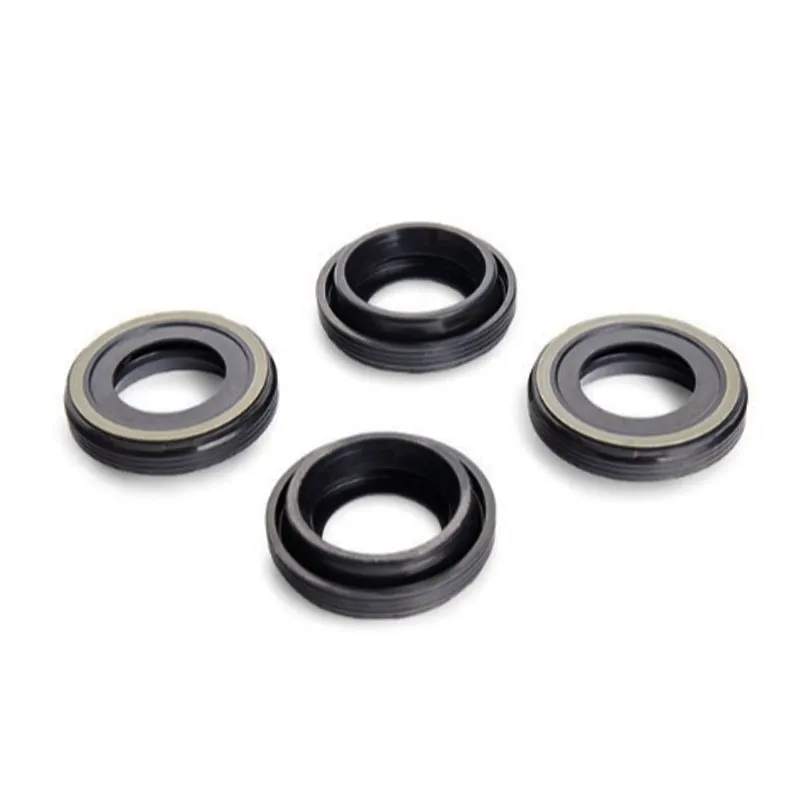
In the realm of industrial equipment, the primary purpose of a single lip seal is to prevent leakage while keeping contaminants out. This functionality may sound straightforward, but achieving optimal sealing requires an understanding of both design principles and material science. Single lip seals typically consist of an elastomeric material that is specifically selected based on the type of fluid it's sealing as well as the operating temperature and pressure of the environment. The material must be compatible with the fluid to prevent degradation that could lead to seal failure.
Through years of hands-on experience, I've found that a common pitfall in seal failure is neglecting to consider the alignment of the components involved. Even the finest single lip seal can fail if the shaft it's meant to seal is improperly aligned, leading to uneven pressure distribution and premature wear. Regular maintenance checks and precise installation can mitigate these risks significantly.
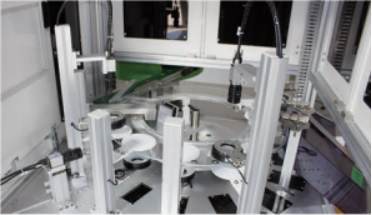
From a professional perspective, choosing the right seal requires a deep understanding of the application's specific demands. Are corrosive fluids involved? What are the operational temperatures? Are there substantial variances in pressure? Answering these questions ensures that the seal chosen is not just adequate but ideal. For instance, in food processing industries, seals must not only provide a tight seal but also comply with health and safety regulations requiring specific non-toxic and easy-to-clean materials.
single lip seal
Establishing authority in the field, I must highlight that innovation is continuously propelling the development of single lip seals. Recent advancements include the introduction of advanced polymers and elastomers that offer superior resistance to wear and chemical corrosion. Furthermore, computer-aided design (CAD) tools have become invaluable in designing seals that fit more precisely and operate more efficiently.
Trust in the manufacturer is also critical. Companies that have a solid reputation and offer quality guarantees provide peace of mind that the products will perform as expected. This is essential because unexpected seal failures not only cause operational disruptions but can also lead to costly repairs and safety hazards.
In conclusion, the efficacy of single lip seals directly impacts the performance and reliability of machinery across various industries. By considering the material compatibility, precise installation, and leveraging advanced technologies, businesses can enhance the longevity and efficiency of their equipment. My journey through years of working with these components continuously reaffirms the importance of combining expertise with practical insights to achieve the best outcomes.