Choosing the right O-ring type for your application can significantly impact the efficiency, reliability, and lifespan of your machinery or product. To navigate the complex world of O-rings, it is crucial to have an in-depth understanding of the various types available and their specific applications. This ensures that your choice fosters optimal performance and maintains the integrity of the entire system.
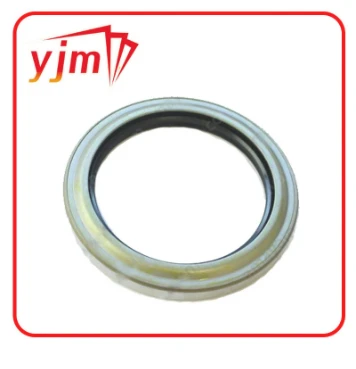
O-rings are versatile sealing elements that provide a crucial function in numerous industries, from automotive and aerospace to pharmaceuticals and petrochemicals. Their resilient design means they are invaluable in both static and dynamic applications, where they help prevent leaks, block contaminants, and maintain pressure.
A fundamental starting point in selecting an O-ring is understanding the material composition that best suits its intended environment.
There are several materials, each with distinct characteristics
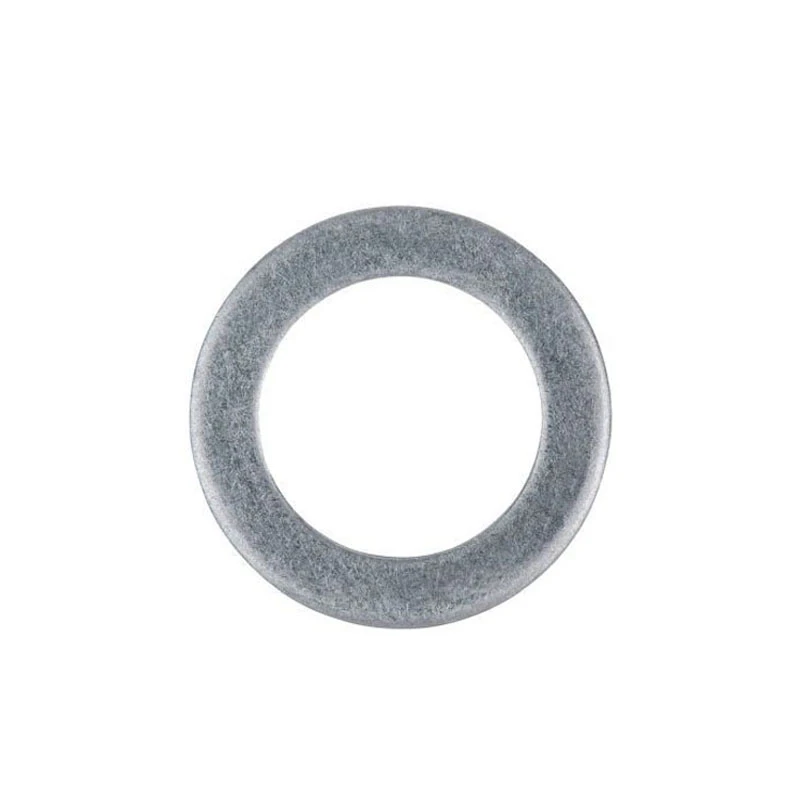
1. Nitrile Rubber (Buna-N) Nitrile is one of the most commonly used O-ring materials due to its excellent resistance to oil, fuels, and other petroleum-based products. It is ideal for automotive applications where exposure to these substances is routine. However, it is less effective in high-temperature settings or when exposed to ozone and weathering.
2. Fluorocarbon (Viton) Known for its outstanding thermal resilience and chemical resistance, Viton O-rings perform exceptionally in demanding environments such as aircraft engines and chemical processing. They offer a higher temperature range and better protection against aggressive fuels and chemicals compared to nitrile, making them invaluable in extreme environments.
3. Silicone Silicone O-rings are praised for their flexibility and excellent performance in a wide temperature range. They are particularly useful in static applications requiring a soft sealing material. However, they exhibit low tear strength and are not suitable for dynamic applications involving rapid motion.
4. EPDM (Ethylene Propylene Diene Monomer) Suitably resistant to weathering, ozone, water, and steam, EPDM O-rings are commonly used in the heating and plumbing industry. They offer significant advantages in outdoor settings and are excellent for applications involving strong acids and alkalis.
o ring types
5. PTFE (Polytetrafluoroethylene) PTFE O-rings are well-regarded for their superior chemical inertness and low friction. They are the go-to option for harsh chemical environments where other materials may degrade. Their mechanical properties, however, can be a limitation in high-stress applications.
Selecting the right O-ring also involves understanding the specific type of O-ring design—each suited for varying uses. Common O-ring types include
- Standard O-rings The most universally applied type, these O-rings can be used in numerous applications due to their basic but effective sealing capability.
- Back-up O-rings These are employed in conjunction with primary O-rings to prevent extrusion in high-pressure applications, thus enhancing the overall sealing system's durability.
- Square-cut O-rings Designed for enhanced sealing over their round counterparts, square cut O-rings can provide better contact surfaces in specific static applications.
When selecting an O-ring, precise sizing and understanding pressure dynamics are equally essential. Undersized or oversized O-rings can result in leakage, while inappropriate sizing can lead to excessive wear or a breakdown in the seal's efficiency. Precision in size and material ensures that the O-ring can withstand the application's pressure and temperature changes without compromising its sealing integrity.
Furthermore, the mounting hardware and gland design directly influence the O-ring's performance. Incorporating considerations for clearance, squeeze, and stretch during the design phase of your system prolongs the functional lifespan of the O-ring.
Achieving optimal sealing with O-rings is an intricate balancing act requiring detailed attention to the specific demands of your application and environmental conditions. By choosing the correct O-ring type and material, you're not only committing to enhanced operational reliability but also extending the life and safety of your systems. This systematic approach to O-ring selection underscores authority in engineering precision, delivering trustworthy performance solutions with long-lasting impacts on industrial productivity.