Flat gasket seals are indispensable components in various industrial applications, offering a reliable solution for creating a secure seal between two surfaces. These seals are critical for ensuring the integrity of assemblies in sectors ranging from automotive to aerospace, plumbing to process engineering. They play a pivotal role in preventing leakage of liquids, gases, and other substances, which could otherwise lead to operational failures or environmental hazards.
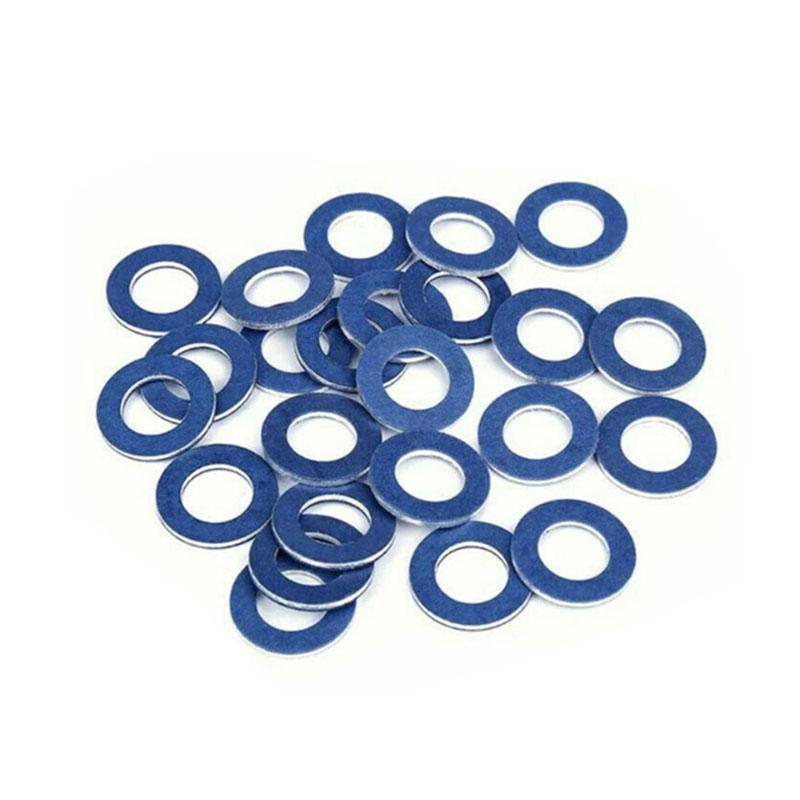
A key aspect of flat gasket seals is their versatility in handling different materials and environments. Depending on the application, these gaskets can be manufactured from rubber, cork, metal, or composite materials.
Each material offers distinct advantages. For instance, rubber gaskets are highly flexible and efficient at sealing joints with minor surface imperfections, making them ideal for plumbing or automotive applications. Metal gaskets, on the other hand, provide exceptional durability and resistance to temperature extremes, commonly used in high-pressure environments like aerospace and industrial machinery.
When selecting a flat gasket seal, understanding the operational environment is crucial. Factors such as temperature extremes, chemical exposure, and pressure conditions will influence the choice of gasket material. For applications involving high temperatures or aggressive chemicals, materials like PTFE or expanded graphite may be preferred due to their superior resistance properties. This tailored approach ensures that the sealing solution is both effective and long-lasting, reducing maintenance needs and associated downtime.
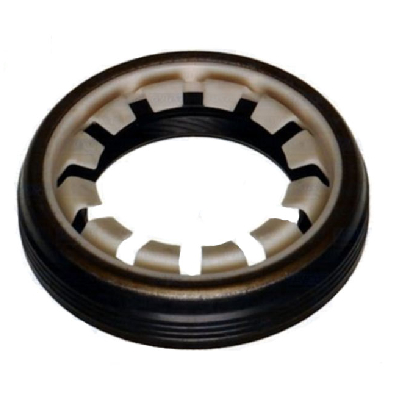
The installation of flat gasket seals is another area where expertise is essential. Proper installation techniques can significantly affect the performance and lifespan of the seal. A common mistake is over-tightening the gasket, which can lead to material deformation and eventual failure. It is advisable to employ a calibrated torque wrench to apply even pressure, ensuring the integrity of the seal without compromising its structural properties. Moreover, surfaces should be clean and even before installation to prevent any undue stresses that might lead to leaks.
Incorporating advanced technologies in the manufacturing of flat gasket seals has also propelled their efficiency and application scope. Laser cutting and computer-aided design (CAD) systems allow for highly accurate gasket fabrication, accommodating intricate designs and specifications. This precision ensures that the gaskets fit perfectly within their applications, enhancing their sealing capabilities and reducing the likelihood of leakage.
flat gasket seal
Expertise in flat gasket seals also entails staying abreast of regulatory standards and compliance requirements. Industries such as food processing or pharmaceuticals have stringent safety and hygiene regulations regarding seal materials and compositions. Compliance with these standards not only ensures operational safety but also builds trust with clients and regulatory bodies.
Authoritativeness in the field can also be demonstrated through continuous innovation and product testing. Developing new materials and designs that meet evolving industry needs can provide significant competitive advantages. Conducting rigorous in-house and third-party testing can further establish a company's credibility, proving that their products withstand real-world conditions and are of the highest quality.
Finally, trustworthiness is rooted in transparency and communication. Providing clear, accessible product information and guidance empowers clients to make informed decisions. Offering technical support and customization options can bolster customer satisfaction, leading to long-term business relationships. Trust is also reinforced by warranty offerings and service guarantees, providing clients with assurance in their investments.
Overall, flat gasket seals are not just mundane components but are crucial elements ensuring the seamless operation of complex systems. Their role in safeguarding against leaks, maintaining operational integrity, and complying with industry standards underscores their importance. Mastery of these seals, through expertise, experience, and authoritative industry knowledge, guarantees not only enhanced product performance but also an establishment's reputation as a reliable partner in industrial solutions.