Exploring the world of oil seals and rubber products unveils a realm of engineering that forms the backbone of several critical industries. Through years of experience working with these essential components, I've observed the profound impact they have on machinery efficiency and longevity.
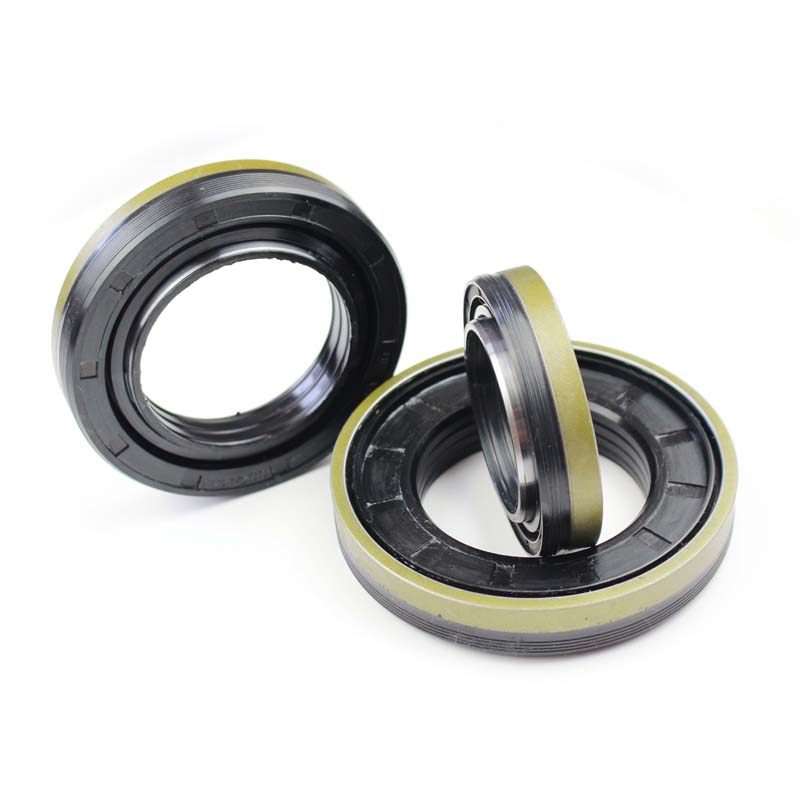
Oil seals, often referred to as 'shaft seals' or 'lip seals,' are key players in preventing the leakage of fluids in machinery. Their primary function is to retain lubricants while excluding contaminants, a task that requires both precision and resilience. The rubber used in oil seals must endure a wide array of temperatures and pressures, often against demanding environmental conditions. This is why materials like nitrile and fluorocarbon rubbers are commonly employed, owing to their superior resistance to oils, heat, and wear.
In my professional journey, the expertise in selecting the right oil seal has proven indispensable. Proper selection hinges on understanding the operational conditions such as rotational speed, temperature range, and exposure to chemicals. For instance, in high-temperature applications, seals made from silicone rubbers are preferred due to their excellent thermal stability. Conversely, for applications involving aggressive chemicals, fluorocarbon rubbers are unmatched, offering superior chemical resistance.
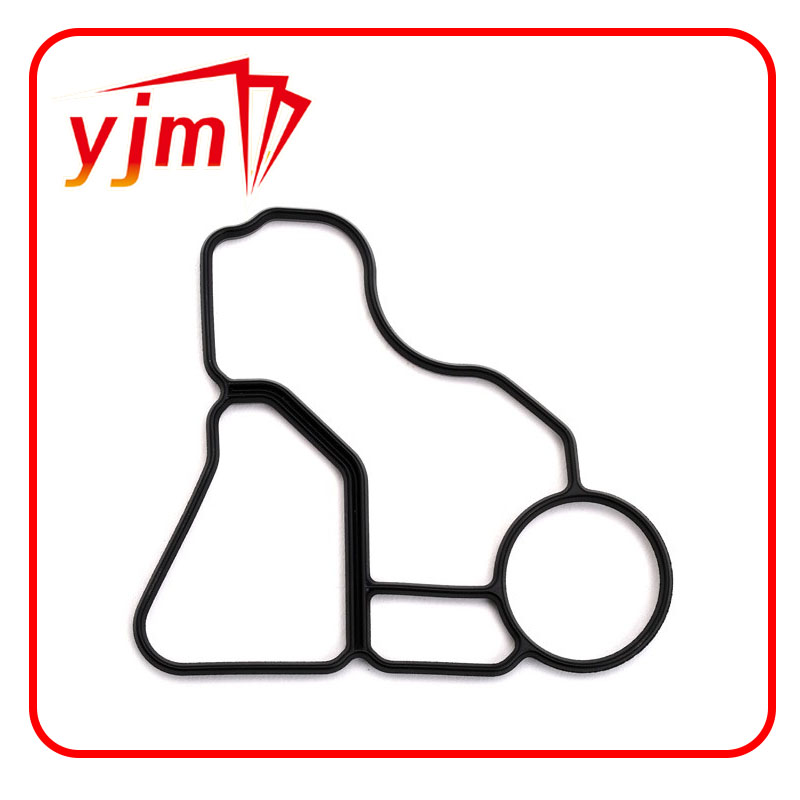
The authority of oil seals and rubber products extends beyond their functional roles—they are crucial for maintaining the operational efficiency of systems. Poor-quality seals can lead to fluid leakage, which not only hampers performance but also poses significant safety risks. In industrial settings,
a failed seal can halt entire production lines, leading to costly downtimes. Thus, ensuring the reliability of these products is paramount, a standard best achieved by sourcing from reputable manufacturers who emphasize stringent quality control processes.
oil seal & rubber products
Trustworthiness in the realm of oil seals and rubber products is built on a foundation of rigorous testing and compliance with international standards. Products that meet ISO and other relevant certifications assure users of their quality and reliability. It's crucial for suppliers to maintain transparency regarding the material specifications and testing methodologies employed, fostering trust with their clients.
In practice, one of the most telling experiences involved a large-scale manufacturing operation where seal failure was significantly impacting machinery uptime. Through diligent analysis and consultation, we implemented seals constructed from hydrogenated nitrile butadiene rubber (HNBR), chosen for its exceptional strength and resistance to heat and oil. This change not only eradicated the leakage issues but also enhanced the machinery's operational lifespan, emphasizing the critical role of insightful expertise in product selection.
Overall, the intersection of engineering skill, material science, and industry standards shapes the field of oil seals and rubber products. It is a testament to the necessity of expertise and authority in ensuring these components serve their vital roles—enhancing machinery performance, ensuring safety, and supporting industrial productivity.