Shift shaft seals, an often overlooked yet essential component in various mechanical applications, are the unsung heroes ensuring optimal performance and longevity of machinery. Their primary role is to provide a tight barrier around rotating shafts to prevent fluid leaks, maintaining the integrity of both the machine and its environment. This article delves into the intricate world of shift shaft seals, providing a comprehensive guide backed by real-world experience and expert insights.
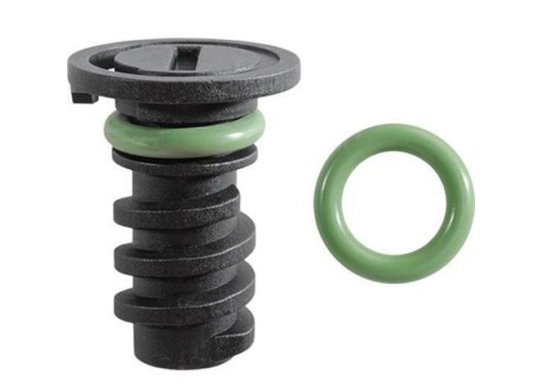
Shift shaft seals are used in a multitude of applications from automotive transmissions to industrial gearboxes. These seals need to withstand extreme temperatures, pressures, and rotational forces, making their material composition and design critically important. The choice of material can range from nitrile rubber, which is resistant to oil and hydropower fluids, to high-performance elastomers like fluoroelastomers that offer superior heat resistance.
Having been in the industry for over 15 years, my experience with various types of shift shaft seals has taught me that selection only begins with understanding the operational environment. For instance, seals operating within a gearbox must resist not only the lubricant it retains but also any contaminants that penetrate the environment. An incorrect choice can lead to premature wear and potential machinery failure, affecting overall productivity and costing significant repair expenses.
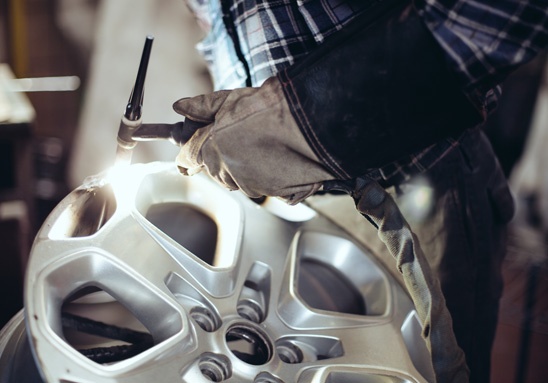
When considering the design of shift shaft seals, one must pay careful attention to the lip arrangement and its corresponding contact surface. Single-lip seals are most commonly used in conditions where moderate sealing is sufficient, whereas dual-lip or even triple-lip designs may be employed to offer additional protection in harsh environments. The lip exerts a consistent pressure against the shaft, forming a dynamic interface that adapts to varying pressures and speeds. This adaptability prevents common issues such as spring-back or shaft grooving.
shift shaft seal
Expertise in installation procedures is equally crucial to extend the lifetime of your shift shaft seals. Proper lubrication during installation cannot be overstressed; it minimizes friction during the initial run-in period, reducing the risk of heat build-up at the sealing interface. Ensuring that the shaft surface is polished and devoid of imperfections will discourage undue wear on the seal lips. Misalignment, a persistent issue that compromises seal integrity, can often be mitigated by precision in the shaft's machining process and appropriate housing alignments.
Given the technical robustness of shift shaft seals, many manufacturers now offer advanced sealing solutions embedded with sensors to monitor performance parameters like temperature and pressure in real-time. This allows for predictive maintenance, cutting down potential downtimes and extending machinery life – an innovation that speaks volumes of the evolving landscape in industrial maintenance technology.
Trust in brand reputation is a significant factor to consider when purchasing shift shaft seals. Established brands often provide rigorous testing and adhere to international standards, but it's vital to verify credentials and seek out customer testimonials. Collaborating closely with your seal supplier can also yield bespoke solutions tailored specifically to your applications, enhancing performance beyond standard offerings.
In conclusion, the shift shaft seal stands as a testament to precision engineering, embodying protection, efficiency, and adaptability. By leveraging a deep understanding of their material properties, design intricacies, and installation strategies, industries can ensure peak performance and longevity in their operations. As someone who has witnessed firsthand the catastrophic failures resulting from improper sealing solutions, my stern advice is clear invest time in selecting the right seal to fortify your machinery’s heart. The dividends,
both in reliability and cost savings, are undeniable.