The oil seal, measuring 14x22x5 millimeters, might appear as an inconspicuous component in the grand scheme of machinery. However, its role is both crucial and complex, serving as the unsung hero that ensures the seamless operation of countless mechanical systems.
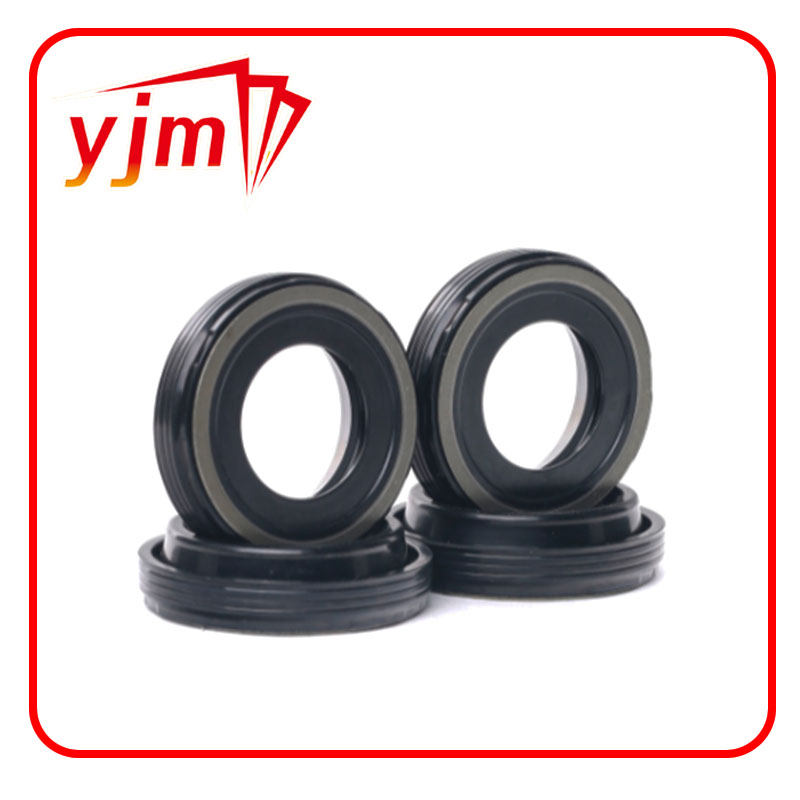
In the realm of industrial machinery and automotive applications, the oil seal operates as a barrier, preventing the escape of lubricants and the intrusion of contaminants. Its dimensions, 14x22x5, not only specify the seal's size but also dictate the particular applications it is best suited for. The 14mm inner diameter fits a specific shaft, while the 22mm outer diameter corresponds with the housing, and the 5mm thickness reflects its ability to withstand pressure and maintain its form.
The expertise involved in selecting the correct oil seal is critical for machinery operators and engineers. Choosing the wrong seal can lead to lubricant leaks, increased friction, and ultimately, machinery breakdown. An expert understands the nuances of oil seal materials, such as nitrile rubber, silicone, and fluorocarbon, each offering varying levels of resistance to temperature, pressure, and chemical exposure. For example, nitrile rubber is renowned for its abrasion resistance and compatibility with a diverse range of oils, making it a popular choice for general applications. In contrast, fluorocarbon seals are preferred in high-temperature environments due to their superior heat resistance.
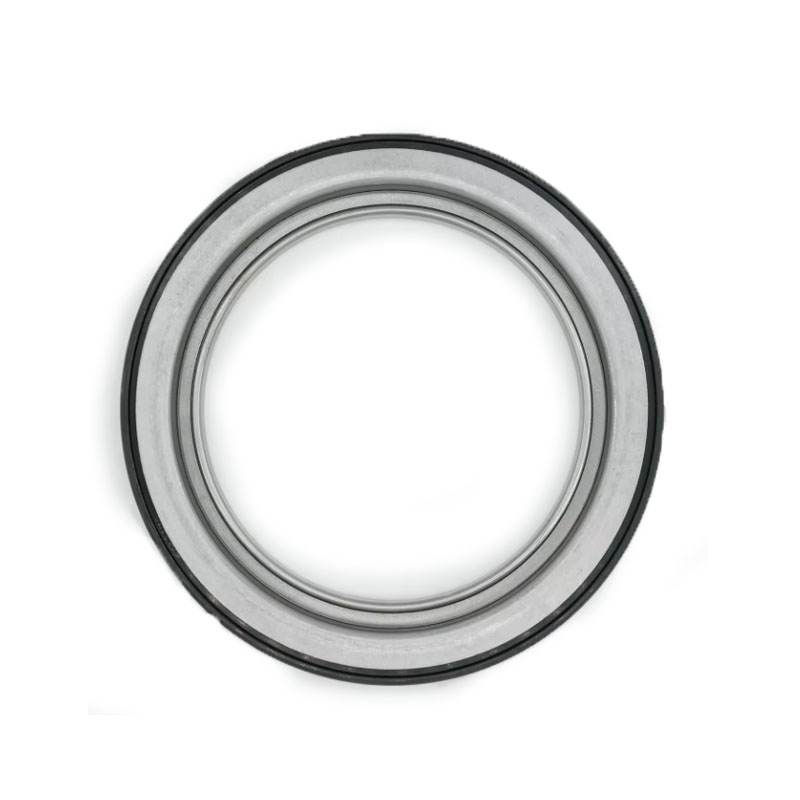
Experience plays a pivotal role in understanding when a 14x22x5 oil seal is the appropriate choice. Experienced engineers and mechanics recognize patterns of wear and failure that inform not only when to replace seals but also how to preemptively schedule replacements to avoid costly downtime. Observations from the field often reveal that while seals of this size serve well in compact engines and small pumps, exceeding their operational parameters by subjecting them to excessive forces or incompatible fluids can result in premature seal failure. Thus, practical experience supplements theoretical knowledge, shaping maintenance strategies that enhance machinery longevity.
oil seal 14x22x5
The authoritativeness of manufacturers and suppliers in producing and distributing oil seals cannot be overstated. Leading manufacturers adhere to rigorous quality standards, such as ISO 9001 certification, to ensure each seal's precision and durability. Top-tier brands continually invest in research and development, pushing the boundaries of seal technology by integrating advanced materials and engineering innovative designs, like double lip seals, which offer enhanced protection against dust and debris. Authoritative sources provide not only products but also valuable insights and technical support, guiding users in achieving optimal seal performance.
Trustworthiness is established through demonstrating the performance of 14x22x5 oil seals across diverse applications and collecting user testimonials. When an industrial plant reports significant reductions in maintenance costs due to the reliability of these seals, or an automotive workshop cites fewer customer returns attributed to effective sealing solutions, trust is built upon verified performance. Transparency in the manufacturing process, including material sourcing and testing protocols, further reinforces consumer confidence in the durability and integrity of the seals.
In conclusion, the 14x22x5 oil seal embodies a confluence of precision engineering and practical application. Its small stature belies its critical function; as a safeguard for lubrication systems, it quietly ensures the efficient operation of myriad machines. Success in utilizing such seals hinges on understanding their materials and limitations, leveraging both expertise and experience to preclude mechanical failures. Authoritative producers provide reassurance of quality, while trusted performance data solidifies confidence in this essential, yet often overlooked, component.